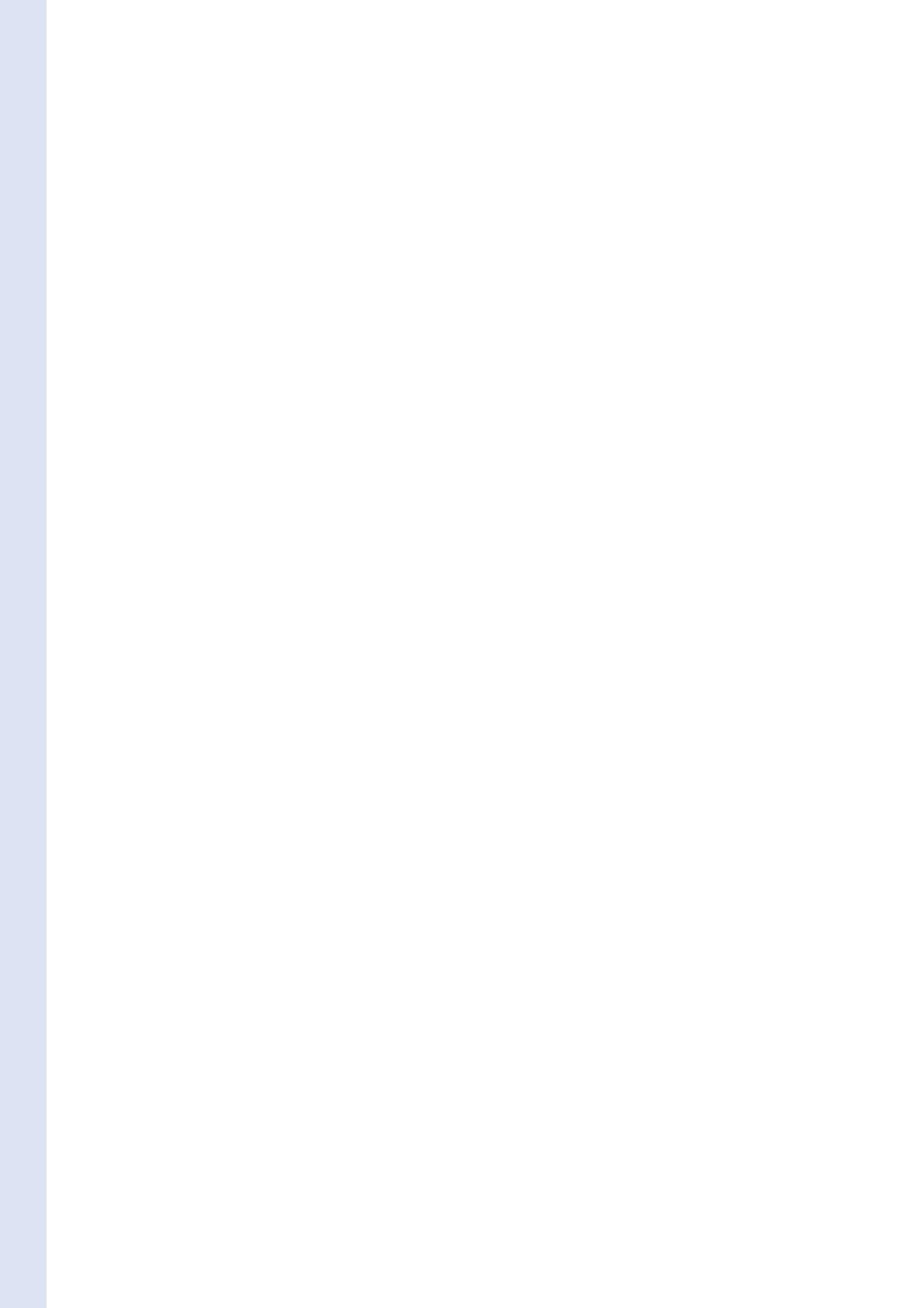
R
EMERCIEMENTS
Je tiens à remercier en premier lieu M. J.-C. V
ANNIER
,
directeur du département
d’Électrotechnique et de Systèmes d’Énergie de Supélec, pour m’avoir accueilli au sein de
son département et dans le cadre de l’union de laboratoires S
PEE
L
ABS
et pour son
implication dans la recherche d’un sujet de recherche qui s’est avéré être une passion.
Cette thèse n’aurait pas eu lieu sans le concours de la société Moteurs Leroy-Somer
qui a proposé et financé ce sujet d’étude. Ce fut un très grand plaisir d’avoir pu travailler dans
ce contexte d’échange industriel et scientifique de très grande qualité et avec beaucoup de
liberté dans l’exploration de différentes voies. Je suis donc extrêmement reconnaissant à
MM. F.
P
ELTIER
, C.
P
ETIT
, C.
P
LASSE
, J.
S
AINT
-M
ICHEL
, C.
A
NDRIEUX
et M.
T
IENTCHEU
.
C’est également avec beaucoup d’enthousiasme que je les rejoins à l’issue de cette thèse avec
la volonté de continuer à apprendre de leurs grandes expériences.
Je tiens à exprimer toute ma gratitude à M. D.
S
ADARNAC
, mon directeur de thèse,
ainsi qu’à MM. M.
G
ABSI
(S
ATIE
E
NS
Cachan), C.
M
ARCHAND
(L
GEP
) et J.-C.
V
ANNIER
,
mes encadrants, pour leur disponibilité et pour les réponses et conseils qu’ils ont su
m’apporter lors de nos discussions tout au long de ces années de travail. Ils m’ont donné le
goût et la passion des machines électriques ainsi que la rigueur dans le travail.
Je souhaite également associer à ce travail les enseignants de Supélec MM. P.
D
ESSANTE
et P.
L
EFRANC
pour les multiples échanges fructueux de fichiers, d’idées et de
points de vue.
Je veux maintenant faire part de toute ma reconnaissance aux membres de mon jury
de thèse et particulièrement à Mme
A.
L
EBOUC
(G2
E
L
AB
) pour m’avoir fait l’honneur de le
présider. Que Mme
J.
S
OULARD
(K
TH
) et M.
P.
B
ROCHET
(L2
EP
) trouvent ici mes plus vifs
remerciements pour l’intérêt qu’ils ont porté à ce travail en acceptant la lourde tâche d’en être
les rapporteurs. Ainsi que MM. M.M.
R
ADULESCU
(U
NIVERSITATEA
T
EHNICÃ
C
LUJ
-
N
APOCA
) et A.
R
AZEK
(L
GEP
) pour m’avoir fait le plaisir d’examiner cette thèse.
Il est temps maintenant de remercier ceux qui font partie des « à côtés » du doctorat
mais qui ont une contribution inestimable de part l’ouverture scientifique et les moments de
détente qu’ils m’ont apportés. Je veux remercier tout particulièrement Pierre qui a d’abord
été mon collègue de bureau puis mon ami pendant ces trois années. Nous avons partagé
ensemble de très nombreuses idées et progressé dans notre construction intellectuelle ainsi
que dans notre pratique de la pêche sportive ! Je dois exprimer à reconnaissance à Amir qui
m’a mis le pied à l’étrier en ce qui concerne l’enseignement et pour m’avoir transmis une part
de ses grandes qualités pédagogiques. Je remercie tous mes camarades doctorants : Ange,
Delphine, Maialen, Natalie, Soukayna, Wilfried, Hermann, Miguel, Adel, Jing, Christophe,
Mathieu, Nicolas, Haitham, Christophe, Nam, Gilbert et Benjamin (qui reprend le flambeau)
pour les discussions agréables lors de nos pauses café.
Je conclus cet exercice difficile en remerciant ma famille et ma compagne, Sandra,
pour m’avoir encouragé à faire cette thèse tant que j’étais dans la continuité de ma formation
initiale ; pour m’avoir supporté (dans plusieurs des sens de ce terme) toutes ces années.
tel-00565693, version 2 - 2 Jul 2013