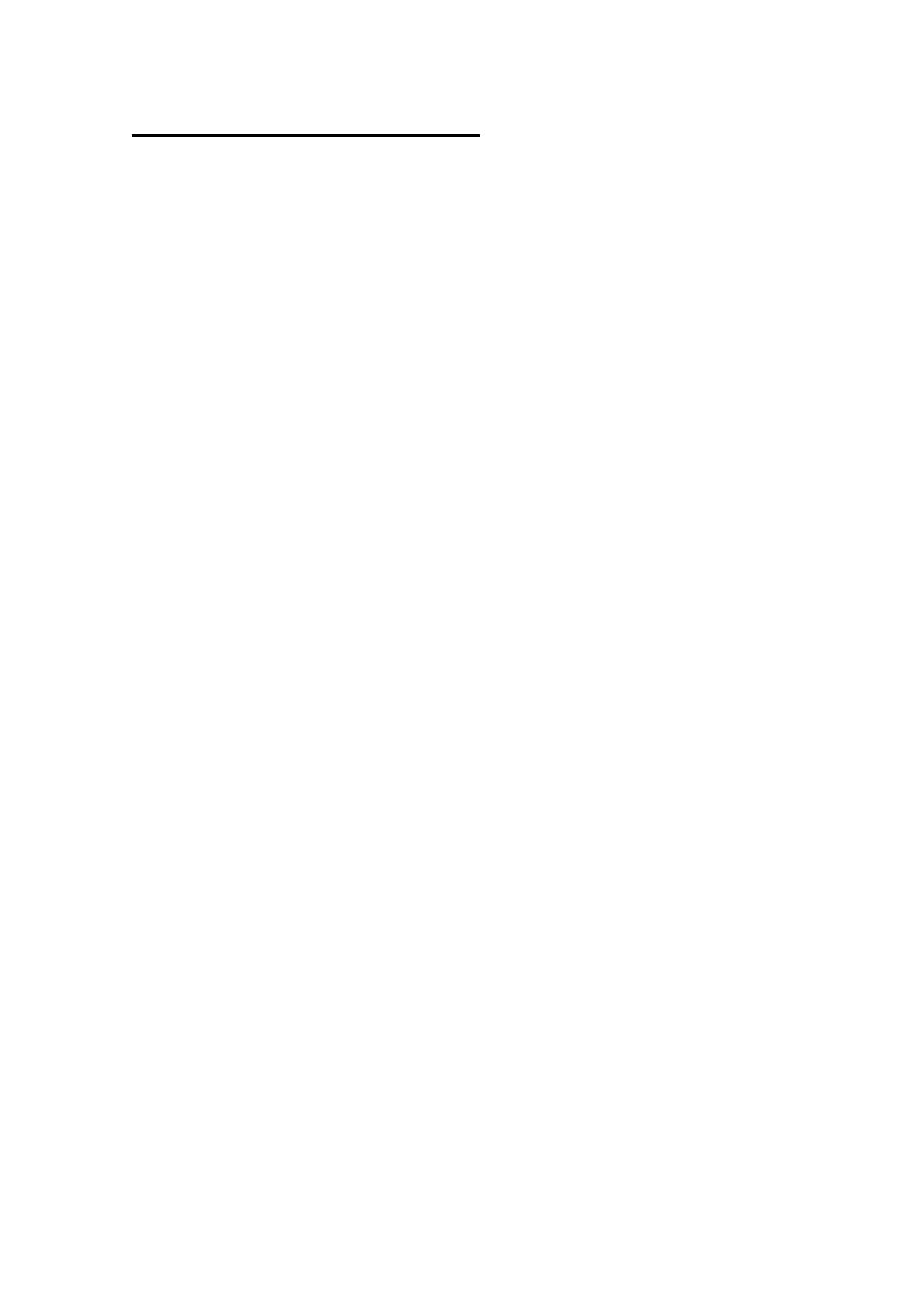
3
Remerciements
Cette étude, réalisée au Laboratoire Central des Ponts et Chaussées (LCPC) en
partenariat avec le Laboratoire de Génie des Procédés Plasma et Traitement de
Surface (LGPPTS) de l’Ecole Nationale Supérieure de Chimie de Paris (ENSCP), a
pu être effectuée grâce au soutien du Laboratoire Central des Ponts et Chaus-
sées et du Laboratoire de Recherche des Monuments Historiques (LRMH) via
l’intermédiaire du Ministère de la Culture.
Je suis reconnaissante à Madame PEBERE et Monsieur GALLIAS d’avoir accepté
d’être rapporteurs de ce mémoire, et je remercie les autres membres du jury :
Mesdames MARIE VICTOIRE et MABILLE ainsi que Monsieur TRIBOLLET qui a accep-
té de présider ce jury.
Je remercie Monsieur le Professeur FIAUD, directeur de cette thèse, ainsi que Ma-
dame MABILLE pour l'aide et la réflexion qu'ils m'ont apportées tous les deux du-
rant cette étude.
Je remercie Monsieur le Professeur AMOUROUX, directeur de l'Ecole Doctorale de
Chimie Appliquée et de Génie des Procédés Industriels, de m'avoir acceptée au
sein de cette formation, et de ce fait de m'avoir permis d'effectuer cette thèse.
Je remercie Mmes TEXIER et MARIE VICTOIRE du LRMH d’avoir participé à cette
étude et suivi régulièrement ce travail.
Je remercie Monsieur ANDRÉ, chef du service Physico-Chimie des Matériaux au
Laboratoire Central des Ponts et Chaussées, et Monsieur CHAUSSADENT, mon tu-
teur au LCPC, de m'avoir permis d'effectuer cette étude, ainsi que l'ensemble du
service de m'avoir accueillie.
Je remercie grandement Fabienne FARCAS de son investissement dans ce travail
et de l’aide précieuse qu’elle m’a apportée pour finaliser cette étude.
Je remercie Madame BOUTEILLER et Monsieur RAHARINAIVO, d'avoir été disponi-
bles et de bons conseils lorsque j'en ai eu besoin.
Je remercie Nathalie, Brice, Houda, Sévérine, Sophie, Najet et Sabah, les stagiaires
dont l'aide a été utile et appréciée pour ce travail de recherche.