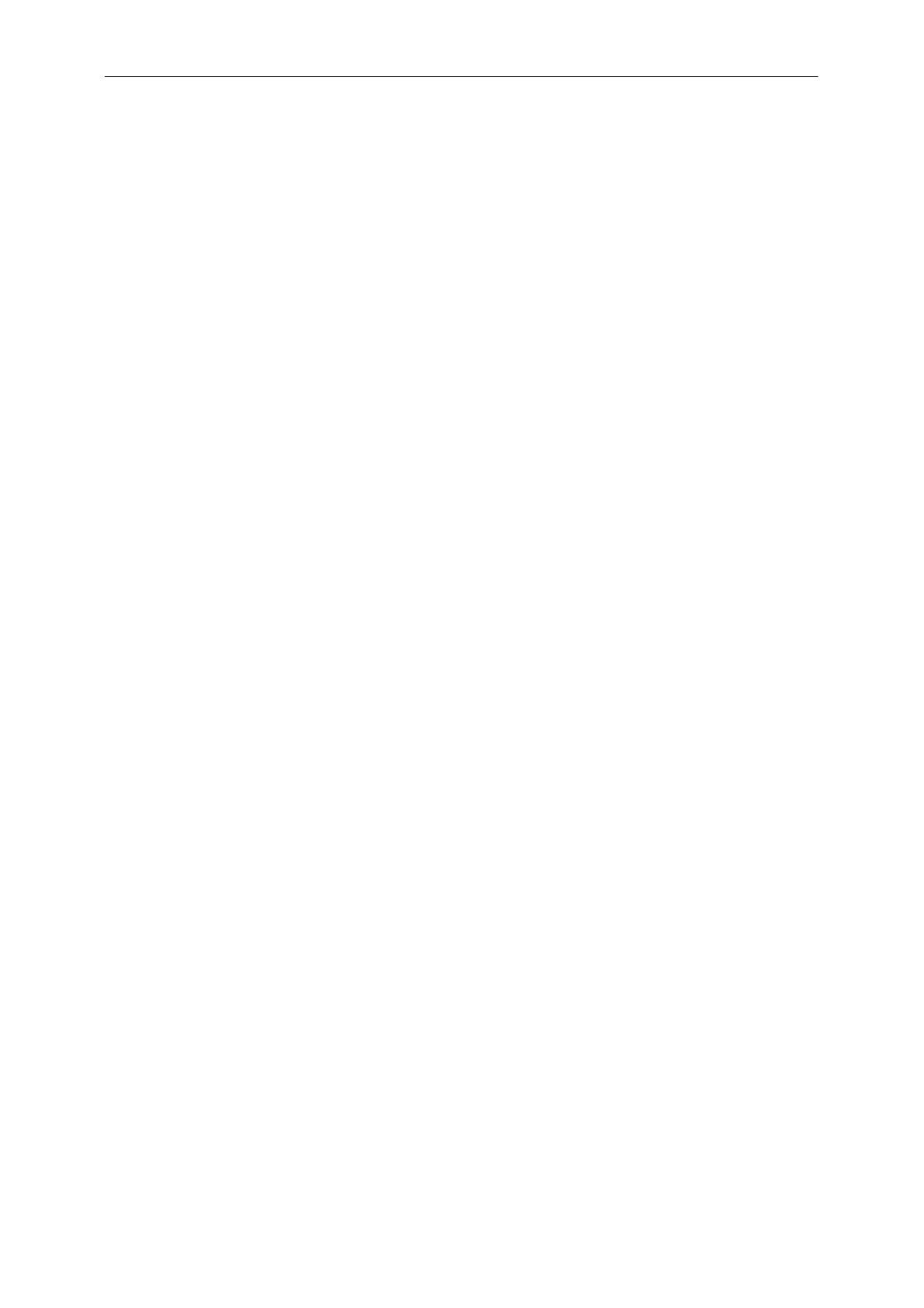
Nomenclature
3
Nomenclature
AAire du fond de piston m2
aDistance vertical entre le sommet de la jupe et l’axe de piston m
bDistance vertical entre le sommet de la jupe et le centre de masse m
cJeu radial entre le piston et le cylindre à température ambiante m
Cg Désaxage du centre de gravité m
Cp Désaxage piston – axe m
dHauteur de la dénivellation à la moitié de la jupe du piston m
eh , eb Excentricité du haut et du bas de la jupe m
FPortance du film hydrodynamique N
Force de connexion agissant le long de la bielle
FgForce des gaz de combustion N
FIC Force d’inertie due à la masse du piston N
FIP Force d’inertie due à la masse de l’axe du piston N
hEpaisseur de film lubrifiant m
Ipist Moment d’inertie du piston par apport à l’axe Kg.m2
LLongueur de la jupe du piston m
lLongueur de la bielle m
fForce de frottement N
MMoment hydrodynamique par apport à l’axe N.m
MIC Moment d’inertie du piston N.m
maxe Masse de l’axe Kg
mpist Masse du piston Kg
PPression hydrodynamique Pa
PgPression des gaz de combustion Pa
PPPerte de puissance instantanée W
RRayon du piston m
rRayon du vilebrequin m
tTemps s
UVitesse axiale du piston m/s
yCoordonnée mesurée à partir du haut de la jupe du piston m
Angle de basculement du piston rad