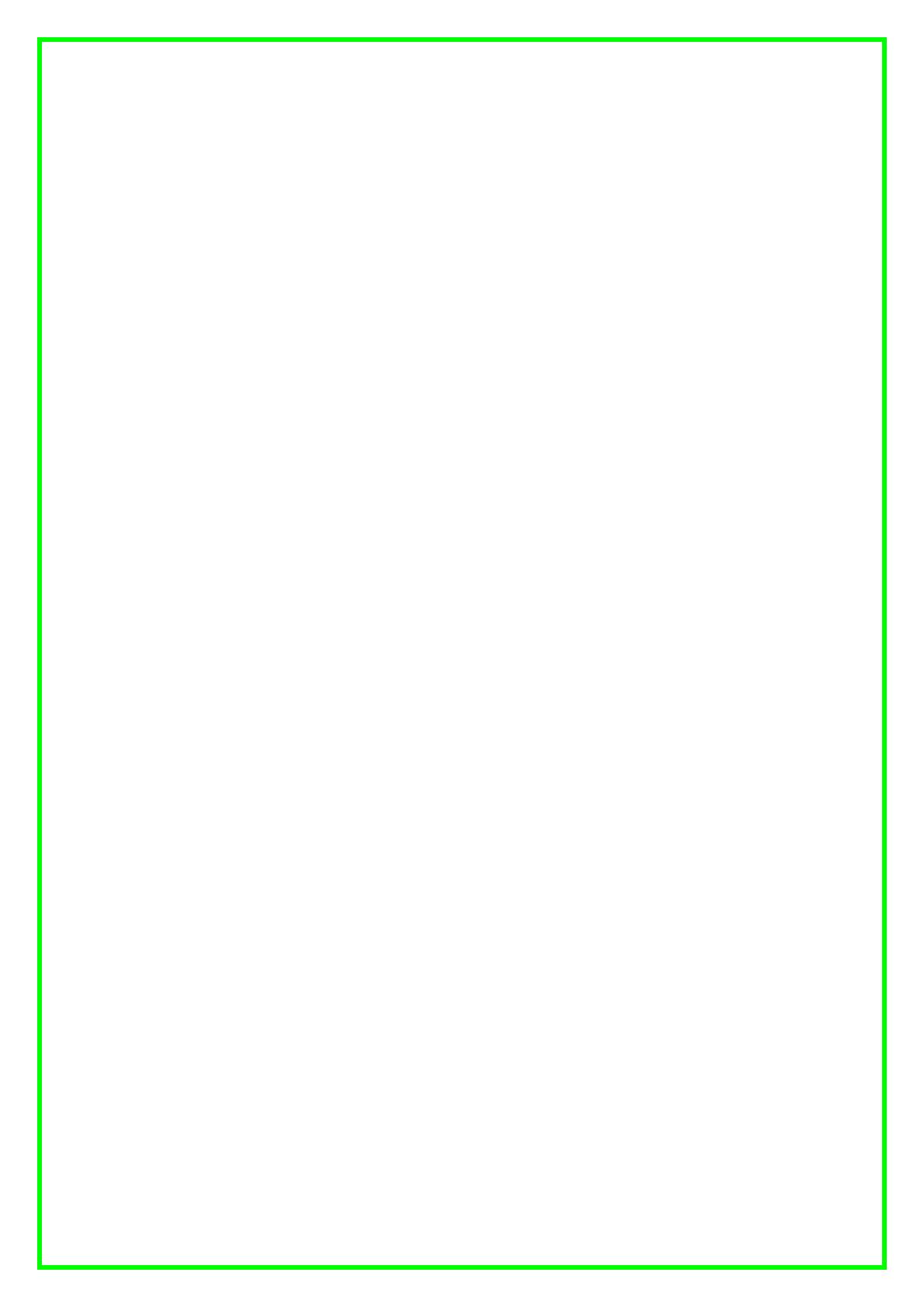
« Lean Manufacturing : application aux entreprises algériennes»
Résumé :
L’entreprise algérienne, particulièrement la petite et moyenne entreprise (PME), est soumise à
une phase de mutations majeures dont l’objectif se situe dans la recherche d’une amélioration de la
performance. Cette amélioration vise à la rendre plus compétitive pour faire face aux menaces et à
relever les défis auxquels elle est aujourd’hui confrontée. Pour renforcer ses capacités de
production et améliorer significativement sa compétitivité en s’alignant sur les standards internationaux
d’organisation et de gestion, les pouvoirs publics algériens ont mis en œuvre une multitude de
programmes de mise à niveau. Cependant, les résultats sont mitigés. Dans ce contexte, nous
préconisons aux entreprises algériennes d’adopter le Lean Manufacturing qui est une démarche
d’amélioration continue concentrée sur la réduction des gaspillages pour une production et un
rendement plus juste. Nous proposons un environnement d’application de la démarche, basé sur
l’intégration des outils Lean. Le but est de proposer un ensemble de solutions ayant pour objectif le
renforcement de la compétitivité de l’entreprise algérienne.
Mots clefs : Lean Manufacturing, PME, Mise à Niveau, Compétitivité, Performance, Diagramme
d’Ishikawa, 5S, Value Stream Mapping, Roue de Deming
« Lean Manufacturing: application to the Algerian firms »
Abstract:
The Algerian firm, particularly the small and medium-sized enterprise (SME), is subjected to a phase of
major transformations the objective of which is situated in the research for an improvement of the performance.
This improvement aims at making it more competitive to face the threats and to meet the challenges with which
it is confronted today. To strengthen its production capacities and improve significantly, its competitiveness by
aligning itself with the international standards of organization and management, the Algerian public authorities
implemented a multitude of programs of upgrade. However, the results are mitigated. In this context, we
recommend to the Algerian firms to adopt Lean Manufacturing which is a continuous improvement approach
concentrated on the reduction of the wasting for a production and a more just efficiency. We propose an
environment of application of the approach, based on the integration of tools Lean. The purpose is to propose a
set of solutions having for objective the strengthening of the competitiveness of the Algerian firm.
Key words: Lean Manufacturing, SME (Small and Medium-Sized Enterprise), Upgrade,
Competitiveness, Performance, Diagram of Ishikawa, 5S, Value Stream Mapping
Lean Manufacturing
:
Lean
Manufacturing
Lean Manufacturing
- - -- - Lean Manufacturing:
Value Stream Mapping -5S-(