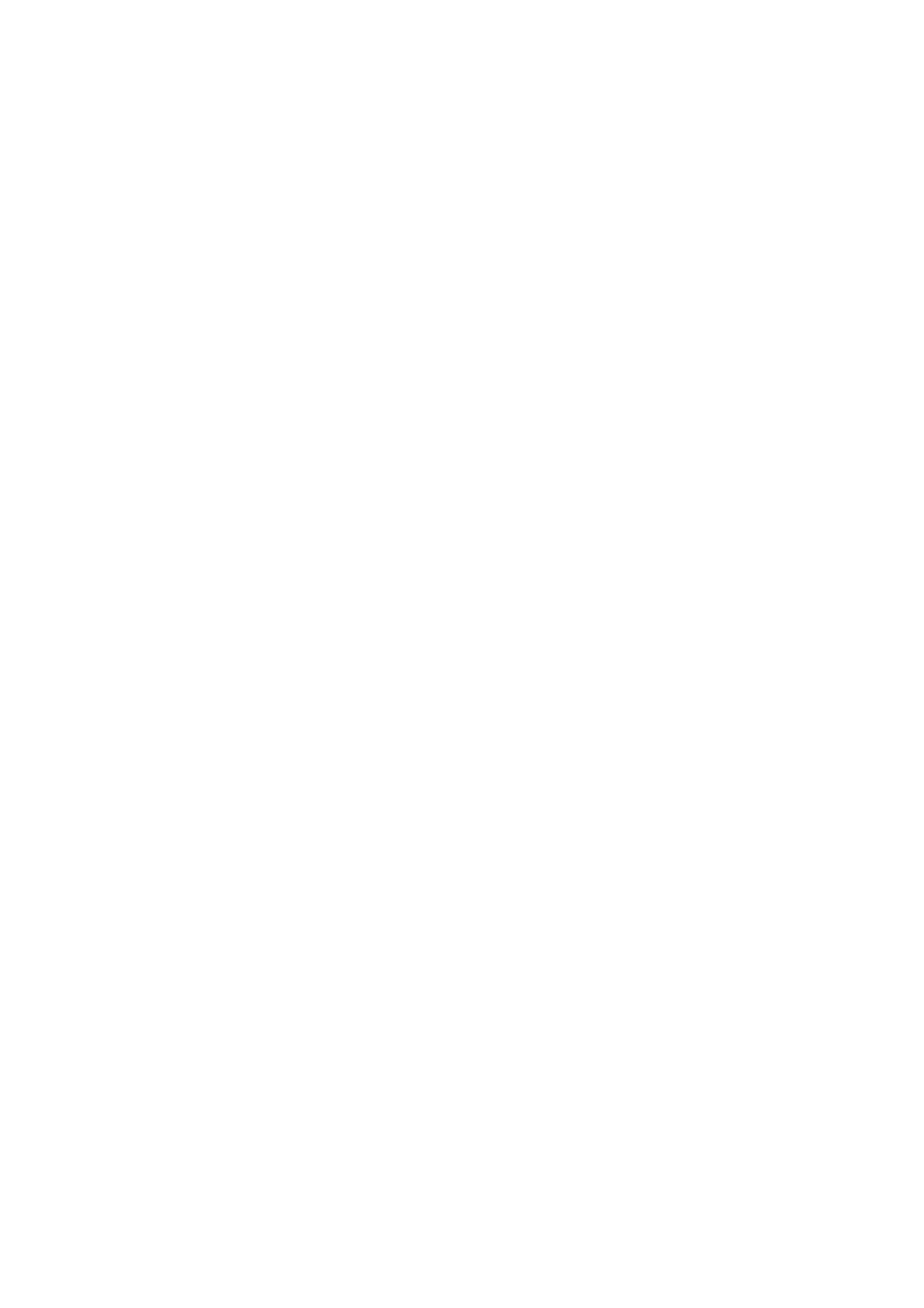
II.3 CONDITIONS ET TECHNIQUES ELECTROCHIMIQUES------------------------------------------------ 22
II.3.1 Conditions électrochimiques ----------------------------------------------------------------22
a. L’électrolyte-------------------------------------------------------------------------------------22
b. Les électrodes-----------------------------------------------------------------------------------22
II.3.2 Méthodes électrochimiques------------------------------------------------------------------22
II.3.2.1 Chronopotentiométrie -------------------------------------------------------------------23
II.3.2.2 La voltamètrie----------------------------------------------------------------------------23
II.3.2.3 Spectroscopie d’impédance électrochimique-----------------------------------------27
II.4 OBSERVATIONS MICROSCOPIQUES ET ESSAIS DE MICRODURETE----------------------------- 31
II.4.1 Observation microscopique------------------------------------------------------------------31
a. Polissage mécanique ---------------------------------------------------------------------------31
b. Attaque chimique-------------------------------------------------------------------------------31
c. Microscopie optique ---------------------------------------------------------------------------32
II.4.2 Microdureté------------------------------------------------------------------------------------32
a. Dispositif expérimental-------------------------------------------------------------------------------32
CHAPITRE III -------------------------------------------------------------------------------------------------------------- 34
RESULTATS ET DISCUSSIONS --------------------------------------------------------------------------------------- 34
INTRODUCTION----------------------------------------------------------------------------------------------------------- 34
III.1 DETERMINATION DES ZONE LES PLUS SENSIBLES A LA CORROSION ET
COMPREHENSION DES PROCESSUS AYANT LIEU A L’INTERFACE METAL/SOLUTION------- 35
III.1.1 Soudure de la tôle de livraison-------------------------------------------------------------36
a. Courbes chronopotentiomètriques---------------------------------------------------------------36
b. Voltamétrie----------------------------------------------------------------------------------------37
b.1 Les courbes cathodiques ---------------------------------------------------------------------38
b.2 Les courbes anodiques -----------------------------------------------------------------------39
b.3 Courbes de Tafel------------------------------------------------------------------------------40
c. Spectroscopie d’impédance électrochimique --------------------------------------------------41
d. Observations microscopiques--------------------------------------------------------------------43
e. Essais de microdureté-----------------------------------------------------------------------------44
III.1.2 Assemblage de deux tôles saines----------------------------------------------------------45
a. Courbes chronopotentiométriques---------------------------------------------------------------45
b. Voltamétrie-----------------------------------------------------------------------------------------46
b.1 Les courbes cathodiques ---------------------------------------------------------------------47
b.2 Les courbes anodiques -----------------------------------------------------------------------48
b.3 Courbes de Tafel------------------------------------------------------------------------------48
c. Spectroscopie d’impédance électrochimique --------------------------------------------------50
d. Observations microscopiques--------------------------------------------------------------------52
e. Essais de microdureté-----------------------------------------------------------------------------53
III.1.3 Assemblage de deux tôles usagées---------------------------------------------------------54
a. Courbes chronopotentiométriques---------------------------------------------------------------54
b. Voltamétrie-----------------------------------------------------------------------------------------55
b.1 Les courbes cathodiques ---------------------------------------------------------------------56
b.2 Les courbes anodiques -----------------------------------------------------------------------57