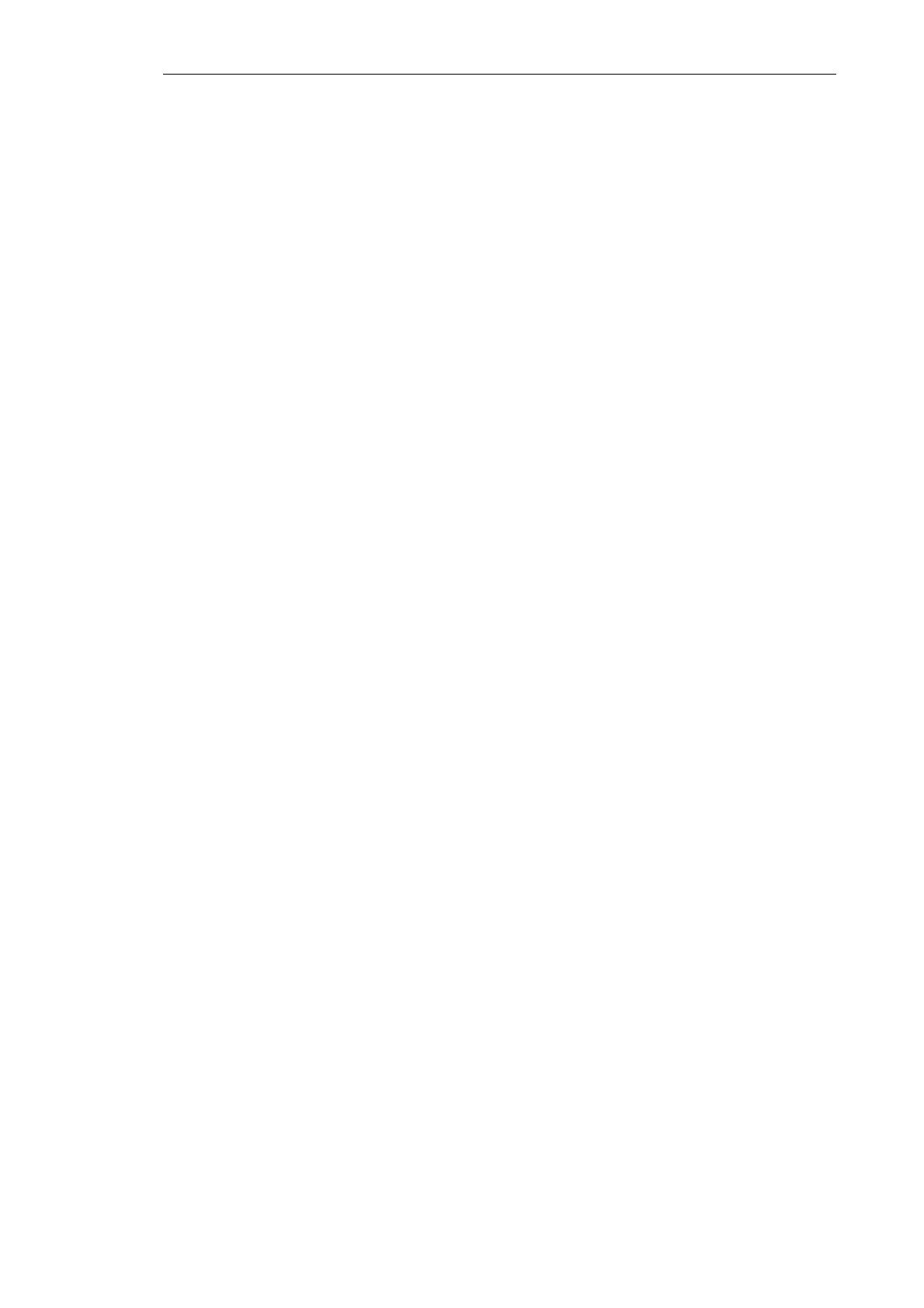
Remerciements
Remerciements
Remerciements Remerciements
Remerciements
Tout d’abord, je tiens
Tout d’abord, je tiensTout d’abord, je tiens
Tout d’abord, je tiens
à remercier
à remercierà remercier
à remercier
mon encadreur Dr. A.MIHI d’avoir accepté
mon encadreur Dr. A.MIHI d’avoir accepté mon encadreur Dr. A.MIHI d’avoir accepté
mon encadreur Dr. A.MIHI d’avoir accepté
de diriger ce travail et d’avoir
de diriger ce travail et d’avoir de diriger ce travail et d’avoir
de diriger ce travail et d’avoir
m
mm
mi
ii
is
s s
s à
àà
à
ma d
ma dma d
ma disposition tous les moyens qui m’ont
isposition tous les moyens qui m’ont isposition tous les moyens qui m’ont
isposition tous les moyens qui m’ont
permis
permispermis
permis
de
de de
de mener
menermener
mener
à t
à tà t
à terme cette étude et aussi pour s
erme cette étude et aussi pour serme cette étude et aussi pour s
erme cette étude et aussi pour ses
es es
es précieux conseils et
précieux conseils et précieux conseils et
précieux conseils et ses
sesses
ses
encouragement
encouragementencouragement
encouragements
ss
s.
..
.
Je t
Je tJe t
Je tie
ieie
iens aussi à remercier Dr.
ns aussi à remercier Dr. ns aussi à remercier Dr.
ns aussi à remercier Dr.
A. ABBASSI pour l’intérêt qu’il a bien voulu
A. ABBASSI pour l’intérêt qu’il a bien voulu A. ABBASSI pour l’intérêt qu’il a bien voulu
A. ABBASSI pour l’intérêt qu’il a bien voulu
porter
porter porter
porter à
à à
à ce travail ainsi que
ce travail ainsi que ce travail ainsi que
ce travail ainsi que pour
pour pour
pour l’honneur qu’il m
l’honneur qu’il ml’honneur qu’il m
l’honneur qu’il m’
’’
’a fait en présidant le jury.
a fait en présidant le jury.a fait en présidant le jury.
a fait en présidant le jury.
Mes remerciements vont également au
Mes remerciements vont également auMes remerciements vont également au
Mes remerciements vont également aux
x x
x
Drs. H. DJEBAILI,
Drs. H. DJEBAILI, Drs. H. DJEBAILI,
Drs. H. DJEBAILI, et
et et
et
R. BENBOUTA pour s’être
R. BENBOUTA pour s’être R. BENBOUTA pour s’être
R. BENBOUTA pour s’être intéressé
intéresséintéressé
intéressé
à
àà
à
ce travail et
ce travail et ce travail et
ce travail et d’
d’d’
d’avoir bien voulu
avoir bien voulu avoir bien voulu
avoir bien voulu
m’
m’m’
m’honor
honorhonor
honorer de leur présence
er de leur présenceer de leur présence
er de leur présence
dans ce jury.
dans ce jury.dans ce jury.
dans ce jury.
Mes remerciement s’adresse
Mes remerciement s’adresseMes remerciement s’adresse
Mes remerciement s’adressent
ntnt
nt
également
également également
également à tous ce qui
à tous ce quià tous ce qui
à tous ce qui
m’
m’m’
m’ont aidé
ont aidéont aidé
ont aidé
et m’
et m’et m’
et m’ont
ont ont
ont
permis
permispermis
permis
de faire aboutir ce travail
de faire aboutir ce travailde faire aboutir ce travail
de faire aboutir ce travail,
,,
,
en particulier
en particulieren particulier
en particulier
: Mme BOUZEGHAYA
: Mme BOUZEGHAYA : Mme BOUZEGHAYA
: Mme BOUZEGHAYA
NORA pour sa contri
NORA pour sa contriNORA pour sa contri
NORA pour sa contribution et son soutien
bution et son soutienbution et son soutien
bution et son soutien
durant la réalisation des dépôts, des
durant la réalisation des dépôts, des durant la réalisation des dépôts, des
durant la réalisation des dépôts, des
essais, et de la préparation d
essais, et de la préparation dessais, et de la préparation d
essais, et de la préparation du
u u
u manuscrit
manuscritmanuscrit
manuscrit,
,,
,
sans oublier le concour
sans oublier le concoursans oublier le concour
sans oublier le concours
ss
s
de
de de
de
Mr M. BENAOUF
Mr M. BENAOUFMr M. BENAOUF
Mr M. BENAOUF,
,,
,
des technicien
des techniciendes technicien
des techniciens
ss
s
du hal
du haldu hal
du hall
ll
l
de
de de
de technologie
technologie technologie
technologie et du technicien
et du technicien et du technicien
et du technicien
ch
chch
chargé du
argé duargé du
argé du
laboratoir
laboratoirlaboratoir
laboratoire des
e dese des
e des
rayon
rayonrayon
rayons
ss
s
X de l’université de Biskra.
X de l’université de Biskra.X de l’université de Biskra.
X de l’université de Biskra.
Enfin,
Enfin, Enfin,
Enfin, mes
mes mes
mes remerciements
remerciementsremerciements
remerciements
vont tout particulièrement à mon épou
vont tout particulièrement à mon épouvont tout particulièrement à mon épou
vont tout particulièrement à mon époux
xx
x
BELLOUFI Abderrahim
BELLOUFI Abderrahim BELLOUFI Abderrahim
BELLOUFI Abderrahim pour son
pour sonpour son
pour son
apport inconditionnel et sans lequel ce
apport inconditionnel et sans lequel ce apport inconditionnel et sans lequel ce
apport inconditionnel et sans lequel ce
mémoire n’
mémoire n’mémoire n’
mémoire n’aurait jamais pu
aurait jamais puaurait jamais pu
aurait jamais pu
être
être être
être mené
menémené
mené
à bien.
à bien.à bien.
à bien.