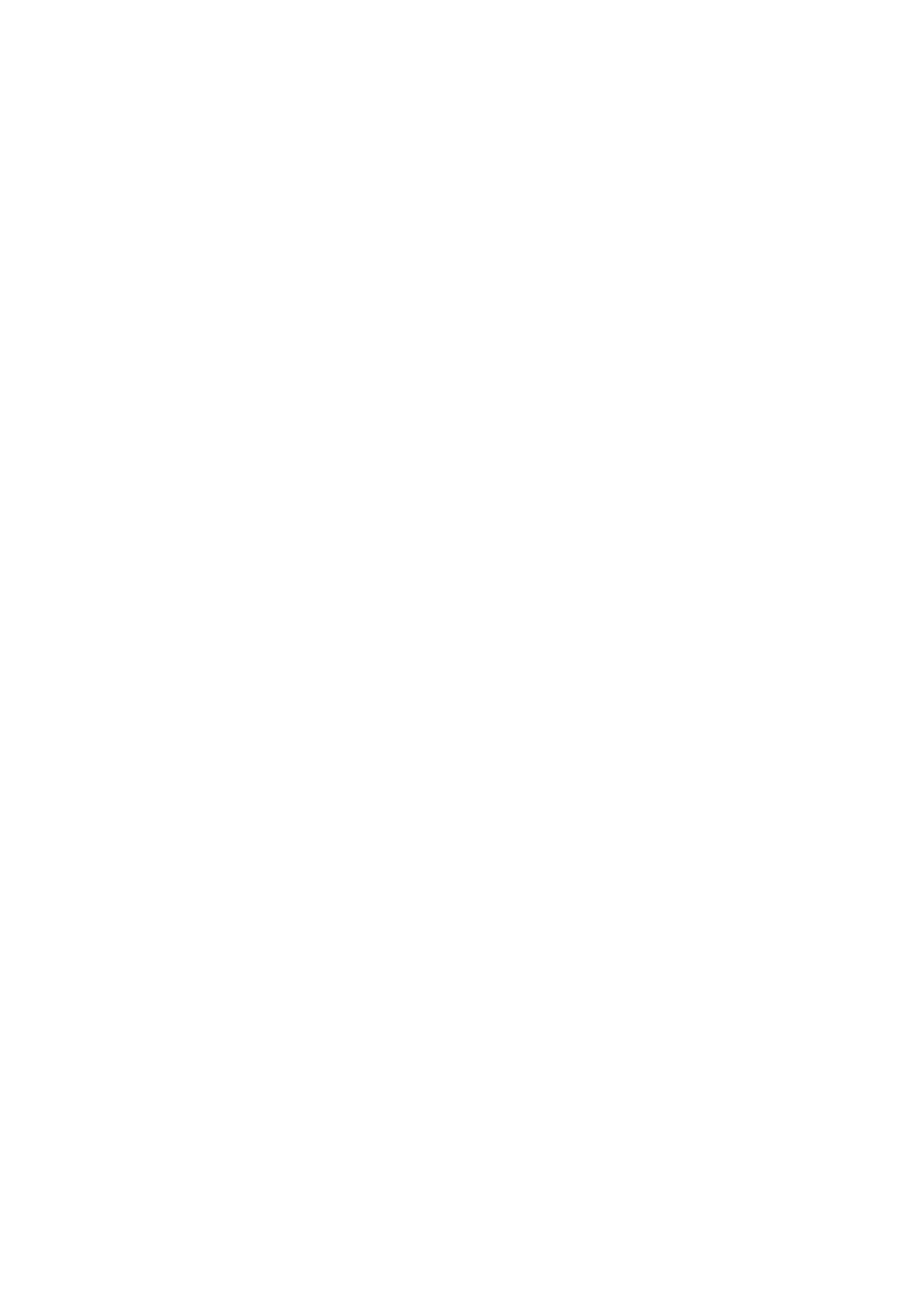
Avant-Propos
Le travail présenté dans les pages suivantes a été réalisé à l'Université Henri Poincaré, Nancy
1 au sein de l’équipe 206 de l’institut Jean Lamour.
Ces trois années de recherches ont été effectuées sous la direction de Monsieur le Professeur
Michel VILASI. Je lui exprime ma gratitude et ma reconnaissance pour ses précieux conseils
et ses encouragements qui m’ont permis de progresser continuellement durant cette thèse.
Ce travail n'aurait pas pu être mené à bien sans l'encadrement de Monsieur Stéphane
MATHIEU, Maître de Conférences à l'UHP. Sa disponibilité, sa compétence et son exigence
ont grandement contribué à la réussite de ce travail.
Je remercie Clotilde BOULANGER, Professeur de l’université de Lorraine, pour avoir
accepté la présidence du Jury de cette thèse.
Je suis très reconnaissant envers Monsieur Yves WOUTERS, Professeur à l’université de
Grenoble et Monsieur Jean-Pierre LARPIN, Professeur à l’Université de Bourgogne à Dijon,
de l'attention portée à ce travail en participant à ce Jury en tant que rapporteurs.
Je suis également très honoré de compter parmi les membres du Jury Monsieur Jean-Bernard
VOGT, Professeur à l’université de Lille 1.
Je tiens en outre à remercier vivement pour l'intérêt porté à ce travail en participant à ce Jury
en tant que membre invité, Pascal DEL-GALLO et Marc WAGNER de la société Air Liquide
et Thierry MAZET de Fives Cryogénie.
Mes remerciements vont également à toutes les personnes qui ont participé de près ou de loin
à la réalisation de ce travail :
- toute l’équipe 206 et plus particulièrement mes camarades docteurs ou étudiants qui
ont contribué à rendre agréable ces trois années : Stéphane KNITTEL, Grégory
MICHEL, Pauline GATEAU, Joffrey TARDELLI, Nabil CHAIA, Rafael BOGADO,
Léo PORTEBOIS, Tuti K. ABDULLAH, Ibra DIOP ;
- Le personnel technique de l’équipe dont le savoir-faire et la disponibilité a permis la
bonne réalisation des expérimentations : Pierre-Jean PANTEIX, Guillaume AUBERT,
Lionel ARANDA, Thierry SCHWEITZER, Jean-Jacques KUNTZ ;
- Les membres du service commun de micro-analyse.
Je ne saurais terminer sans avoir une pensée pour ma famille et mes amis dont le soutien fut
sans faille tout au long de ces trois années et demie.