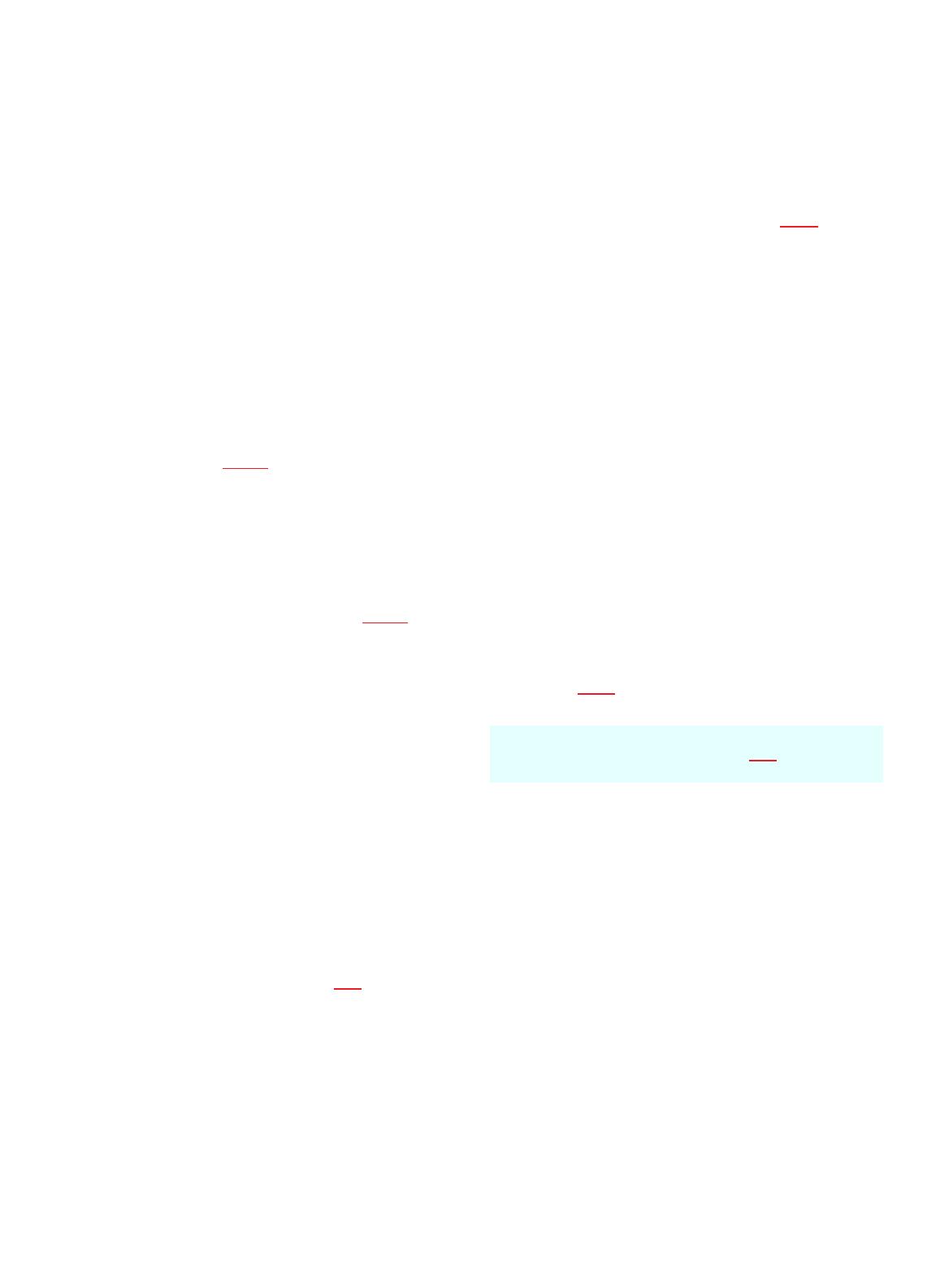
________________________________________________________________________________________________________________________ TUYAUTERIES
Toute reproduction sans autorisation du Centre français d’exploitation du droit de copie est strictement interdite.
© Techniques de l’Ingénieur, traité Génie mécanique
A 830
−
3
1.1.1.4 Corrosion sélective
C’est un type de corrosion très dangereux parce
qu’insoupçonnable : la pièce corrodée ne semble pratiquement pas
concernée, alors que sa résistance diminue considérablement. Elle
consiste en la dissolution sélective d’un élément d’un alliage, les
autres éléments restant non attaqués. Le métal devient poreux et
perd sa résistance.
Industriellement, ce phénomène concerne surtout les
alliages
contenant du zinc
, tels que le bronze ou le laiton, où le zinc subit
cette attaque sélective en milieu acide. L’adjonction de petites
quantités d’étain (environ 1 %) et d’arsenic a permis de mettre au
point des laitons insensibles à ce type de corrosion.
1.1.2 Caractérisation suivant le mode d’action
du milieu
1.1.2.1 Corrosion entre deux métaux différents
Ce type de corrosion implique l’existence de deux métaux
différents reliés entre eux électriquement et baignant dans un liquide
conducteur. L’un des deux métaux, celui qui forme l’
anode
de la pile
ainsi constituée, est attaqué (§ 1.2.1).
C’est surtout au niveau de la conception des ouvrages que l’on
devra éviter de mettre en présence des métaux différents.
1.1.2.2 Corrosion par concentration différentielle
Une hétérogénéité de concentration soit au niveau du métal, soit,
plus souvent, au niveau du milieu agressif, peut donner naissance
à une pile génératrice de corrosion. Le cas le plus fréquent est dû
à l’apparition d’une différence de concentration en oxygène dans la
solution corrosive (
effet Evans
) : la partie métallique en contact avec
la solution pauvre en oxygène devient alors anode (§ 1.2.1) et est
attaquée.
Ces conditions peuvent se présenter dans des zones mortes sans
circulation, telles que des crevasses, l’intervalle entre deux tôles d’un
joint par recouvrement, sous un dépôt d’oxydes ou de produits de
corrosion.
1.1.2.3 Corrosion par frottement
Lorsque deux surfaces métalliques sont en contact et qu’elles se
déplacent l’une par rapport à l’autre, leurs surfaces peuvent se dété-
riorer rapidement et devenir impropres aux mouvements ultérieurs.
Pour que la corrosion par frottement puisse apparaître, il faut
simultanément :
— l’existence d’une pression de contact entre les deux métaux ;
— la présence de vibrations ;
— l’existence d’un glissement entre les deux surfaces ;
— la présence d’oxygène.
Il semble que le phénomène soit dû à l’arrachement et à l’oxyda-
tion des particules métalliques sous l’effet du frottement et de l’éléva-
tion de température qui en résulte. Les conséquences sont :
l’augmentation des jeux, le grippage, l’apparition de défauts pouvant
provoquer des ruptures de fatigue.
La présence d’une huile qui réduira la présence d’air peut être une
solution pour prévenir ce type de corrosion. Une préparation de la
surface métallique (en général phosphatation, § 2.2.4) améliorera la
tenue de l’huile.
1.1.2.4 Corrosion sous tension
Il s’agit d’un type de corrosion accélérée par l’existence de
contraintes dans le métal attaqué. Suivant le type de contraintes,
statiques ou dynamiques, on distingue parfois la
corrosion sous
tension
de la
corrosion sous fatigue.
Ce sont en général les tensions résiduelles (soudage ou écrouis-
sage) qui sont la cause de corrosion sous tension, et très souvent
un traitement de
relaxation
(article
Soudage
[B 621] dans le présent
traité) suffira pour prévenir ce genre de corrosion.
L’acier non allié, en présence de
solutions de soude
, est
particulièrement sensible à la corrosion sous tension et toutes les
soudures, même celles des attaches de supports, doivent être déten-
sionnées si elles intéressent la paroi du réservoir ou de la tuyauterie.
Un type de corrosion sous tension des aciers inoxydables en
présence d’
ions chlore
est étudié au paragraphe 3.3.1.1.
1.1.3 Caractérisation suivant les phénomènes
physiques concernés
On distingue :
— la corrosion électrochimique ;
— la corrosion chimique ;
— la corrosion sèche.
En réalité, la différence essentielle est la présence ou non d’un
milieu conducteur. Dans le premier cas, on se trouvera en présence
d’une
corrosion électrochimique
. Dans le second cas, si le milieu
agressif est liquide, on parlera de
corrosion chimique
alors que s’il
s’agit d’un gaz, on classera ce phénomène sous le nom de
corrosion
sèche.
Il faut cependant noter que les principes physiques de base sont
identiques (transport d’ions, échange d’électrons).
1.2 Corrosion électrochimique
La corrosion électrochimique implique la réunion des conditions
suivantes.
■
Existence d’une dissymétrie physique ou chimique
dans le sys-
tème métal/solution ; cette dissymétrie, parfois difficile à mettre en
évidence, et qui se traduit par une différence de potentiel, peut avoir
des origines très variées :
— hétérogénéité dans la surface d’un métal (traces d’oxydes,
par exemple) ;
— teneur en oxygène différente entre deux points du milieu
(effet Evans, § 1.1.2.2) ;
— concentration variable des solutions.
■
Présence d’un milieu conducteur
(en général liquide) au contact
des parties métalliques
■
Circulation d’un courant électrique
entre deux parties du métal,
l’une étant l’
anode
, l’autre la
cathode
.
En l’absence d’une de ces conditions, il n’y aura pas de corrosion
électrochimique.
1.2.1 Potentiel d’électrode
Le phénomène de base des réactions électrochimiques est un
échange d’électrons entre ions. La notion d’
oxydation
a été géné-
ralisée et interprétée aujourd’hui comme une perte d’électrons et,
la
réduction
, comme un gain d’électrons :
avec
Ox
forme oxydée,
Red
forme réduite.
Ainsi, lorsqu’un métal (par exemple Fe) est mis en contact avec
une solution liquide conductrice, c’est-à-dire susceptible de se
Remarque
: si une différence de potentiel est créée par une
source extérieure (courants vagabonds § 3.1.1), la dissymétrie
telle que définie ici n’est plus nécessaire.
Ox ne–$Red+