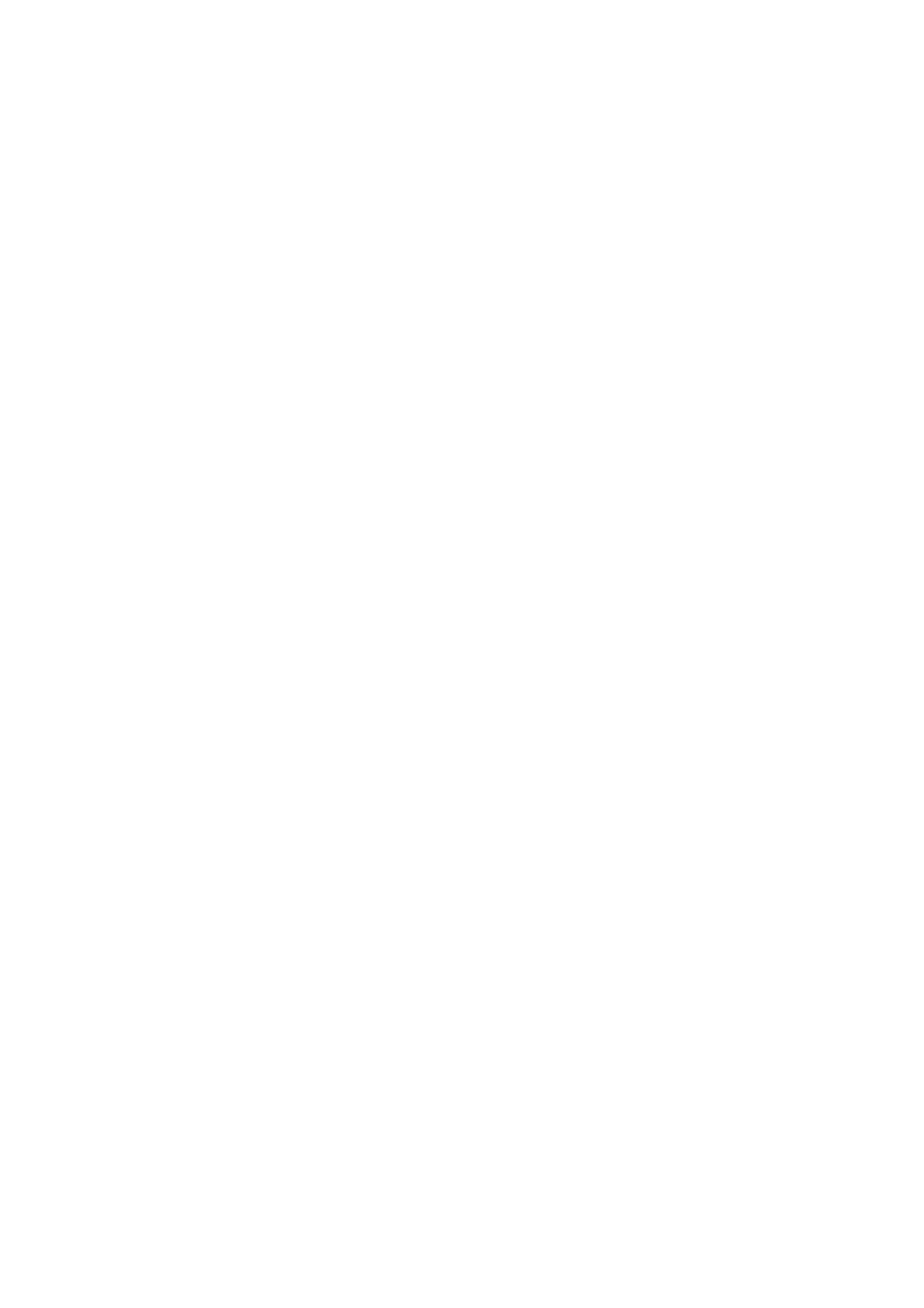
Remerciements
Le travail pr´esent´e dans ce m´emoire a ´et´e r´ealis´e au sein du laboratoire de recherche
l’UMR TREFLE de l’Universit´e de Bordeaux 1 (Unit´e Mixe de Recherche sur les Transferts,
Ecoulements, Fluides et Energ´etique) et ArcelorMittal Research. Ce travail a ´et´e men´e au la-
boratoire TREFLE sur le site de l’ENSCBP (Ecole Nationale Sup´erieure de Chimie Biologie
et Physique) dont je remercie les directeurs respectifs, Eric Arquis et Jean-Marc Heintz et a
´et´e suivi par le chef de projet et l’ing´enieur de recherche d’ArcelorMittal, Maxime laugier et
Pascal Gardin, que je remercie.
Je tiens `a remercier particuli`erement mon directeur de th`ese, Jean-Paul Caltagirone, Profes-
seur de l’Universit´e Bordeaux 1, pour la confiance et l’autonomie qu’il m’a accord´e tout au
long de mes trois ann´ees de th`ese.
Cette th`ese a ´et´e co-encadr´ee par Stephane Vincent du laboratoire TRFLE. Toujours dis-
ponnible, il a su, par ses comp´etences, me donner de bonnes pistes plus ou moins ardues
`a suivre ce qui m’a permis de gagner un temps pr´ecieux. Son enthousiasme et sa ”positive
attitude” concernant mes travaux de recherche m’ont motiv´e et stimul´e pendant ces trois
ans. Pour cela, et pour le reste, je lui exprime ma profonde reconnaissance et toute mon
amiti´e.
Je remercie sinc`erement les membres du jury : M. Patrick Hoffmann, Professeur de l’Ecole
Polytechnique de Lausanne, qui m’a fait l’honneur de pr´esider ma soutenance. MM. Pierre
Montmitonnet, directeur de recherche au CNRS CEMEF (Centre de Mise en Forme des
mat´eriaux), Alain Berlemont, directeur de recherche au CNRS CORIA (COmplexe de Re-
cherche Interprofessionnel en A´erothermochimie) et Aziz Omari, Professeur de l’Institut Po-
lytechnique de Bordeaux qui ont accept´e de prendre du temps et mobiliser leurs comp´etences
pour ˆetre rapporteurs de mon manuscrit et de ma soutenance.
Je tiens `a remercier plus particuli`erement Nicolas Legrand, Maurice Tornicelli, ing´enieurs Ar-
celorMittal, pour toute l’aide pr´ecieuse qu’ils m’ont apport´e au cours de l’ensemble du projet.