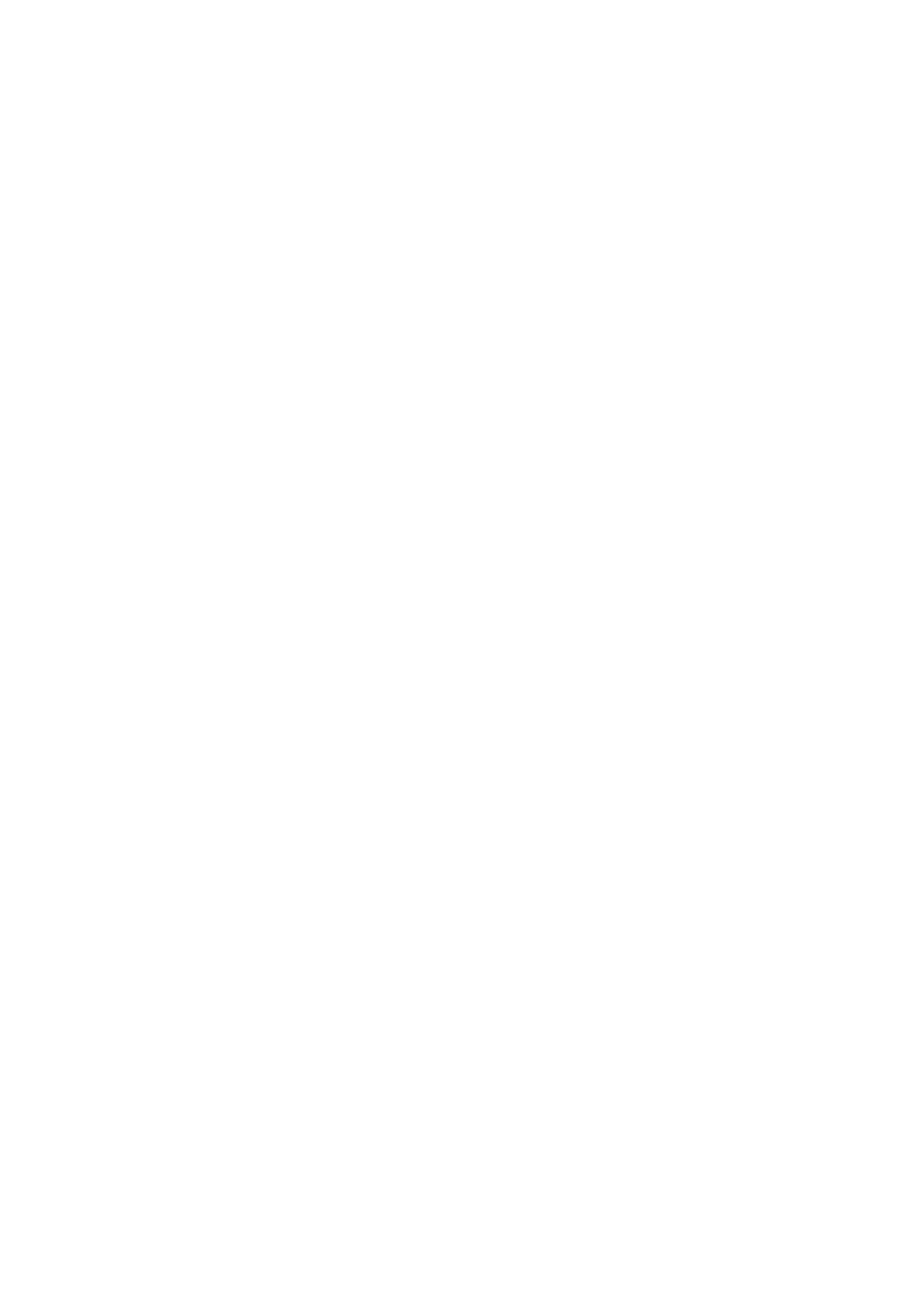
Remerciements
Je remercie en tout premier lieu mes quatre encadrants de thèse qui se sont énormément
investis dans ce projet. Leurs idées, leurs conseils, leur présence et leur écoute ont été précieux tout au
long de ces trois années. Merci spécialement à Amandine Cabiac (IFPEN) pour son optimisme
inconditionnel, à Sylvie Lacombe (IFPEN) pour sa patience, à Catherine Especel (IC2MP) pour ses
relectures attentives, et à Daniel Duprez (IC2MP) pour m'avoir fait partager un peu de son expérience
et de sa bibliographie encyclopédique.
Merci bien sûr à IFPEN, particulièrement à Denis Guillaume et Tivadar Cseri, de m'avoir
accueillie et supportée financièrement pendant cette thèse.
Merci également à Michèle Besson et Franck Dumeignil pour avoir accepté d'être les
rapporteurs de cette thèse (je sais maintenant que quelqu'un l'a lue), et à Yannick Pouilloux pour avoir
accepté de juger ce travail.
Je voudrais aussi remercier toutes les personnes qui m'ont accueillie, aidée et soutenue
pendant ces 3 ans :
- mes collègues du département Catalyse par les Métaux et les Solides Acido-Basiques, en
particulier Karine (SuperCop), Eugénie (SuperMommy), Pascal (SuperKénavo), Denis (SuperSuida),
Charles (SuperBombero), qui m'ont tout appris sur le laboratoire, le Snoop, les clés à molette et les
potins de l'IFP.
- les thésards et les stagiaires que j'ai côtoyés durant ces 3 années, avec une pensée particulière
pour Emanuelle, Filipe et Lilia avec qui j'ai partagé beaucoup de bons moments. Merci aussi à
Bertrand, Thibaut, Fabien, Marius, Tiago, Julie, Vincent, Rachel, Édouard, Pedro et les autres.
- un grand merci à Régis Koerin qui a préparé les oxydes tunsgtés du chapitre 5 pendant son
stage de master 2, et qui croit toujours que je suis géniale même si je n'ai jamais réussi une manip
devant lui.
- merci aux analystes d'IFPEN avec qui j'ai collaboré, qui ont fait beaucoup pour ce travail et
qui m'ont toujours bien traitée : Agnès, Romain, Charlotte, Isabelle, Frédéric, Estelle, Yannick, Anne-
Lise, Hedwige, Florent, Alban, Cédric, Pierre, Nadège, Floriane, Frédéric, Yannis, Nathalie, Nicolas,
Denis, Michaël, Jean, Nathalie, Olivier... et un merci tout particulier à Nadège qui s'est énormément
investie dans ce projet.
- merci à l'équipe Catalyse par les Métaux de l'IC2MP qui m'a accueillie pour la préparation
des bimétalliques et notamment Séverine et Benoît, qui m'ont tout appris sur le sujet.
- merci au chocolat Côte d'Or avec des petites noisettes dedans pour son soutien.
- merci aussi à tous ceux que j'ai oubliés, qu'ils ne m'en tiennent pas rigueur (c'est dur une
thèse !).
Merci à Louis qui sait me faire oublier ma thèse.