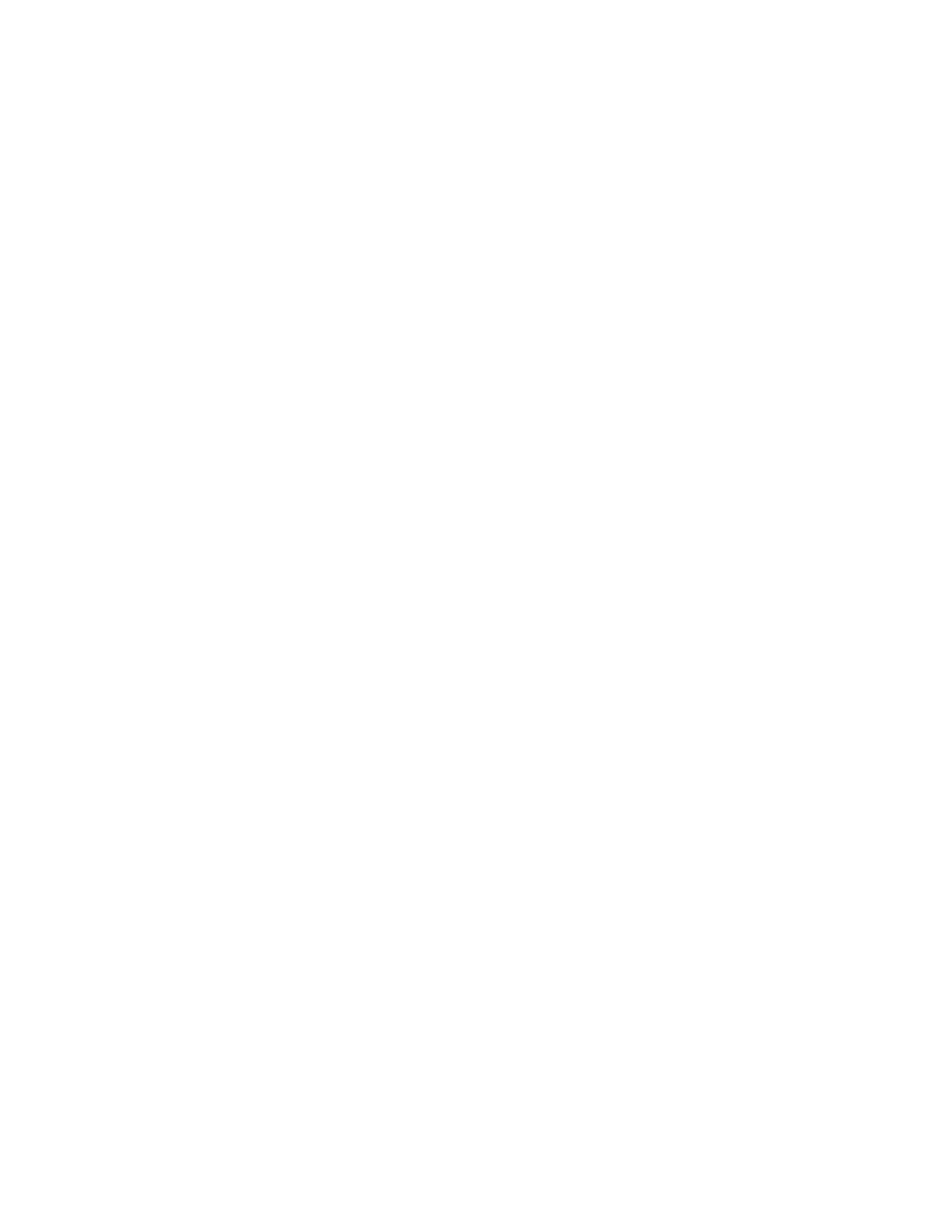
Sommaire
Introduction 1
Chapitre I
1.Structure électronique des matériaux en chimie organique 6
1.1.Théorie des bandes en chimie 6
1.2.Différence avec les semiconducteurs minéraux classiques 7
1.3.Caractéristiques des matériaux organiques 8
1.4.Le dopage des couches 9
1.4.Tableau des matériaux que nous emploierons 10
2.Description des diodes organiques standards 11
2.1.Principe général des OLEDs 11
2.1.1.La balance de charge13
a) L’injection des trous13
b) L’injection des électrons14
c) Conséquences sur l'ingénierie de bande
des structures des OLEDs15
Diode à une seule couche15
Structure bicouche : simple hétéro jonction15
Structure avec double hétérojonction15
2.1.2.Le transport de charge16
2.1.3.L’efficacité des OLEDs17
2.2.Le rapport singulet/triplet 18
2.2.1.Singulets et Triplets18
2.2.3.Le rapport singulet triplet19
2.2.4.Le rendement de luminescence19
2.3.Le couplage optique 20
2.3.1.Réflexion interne totale et photons piégés20
2.3.2.Modélisation du couplage optique et
des effets de microcavités21
2.3.3.Méthodes d’accroissement du couplage optique22