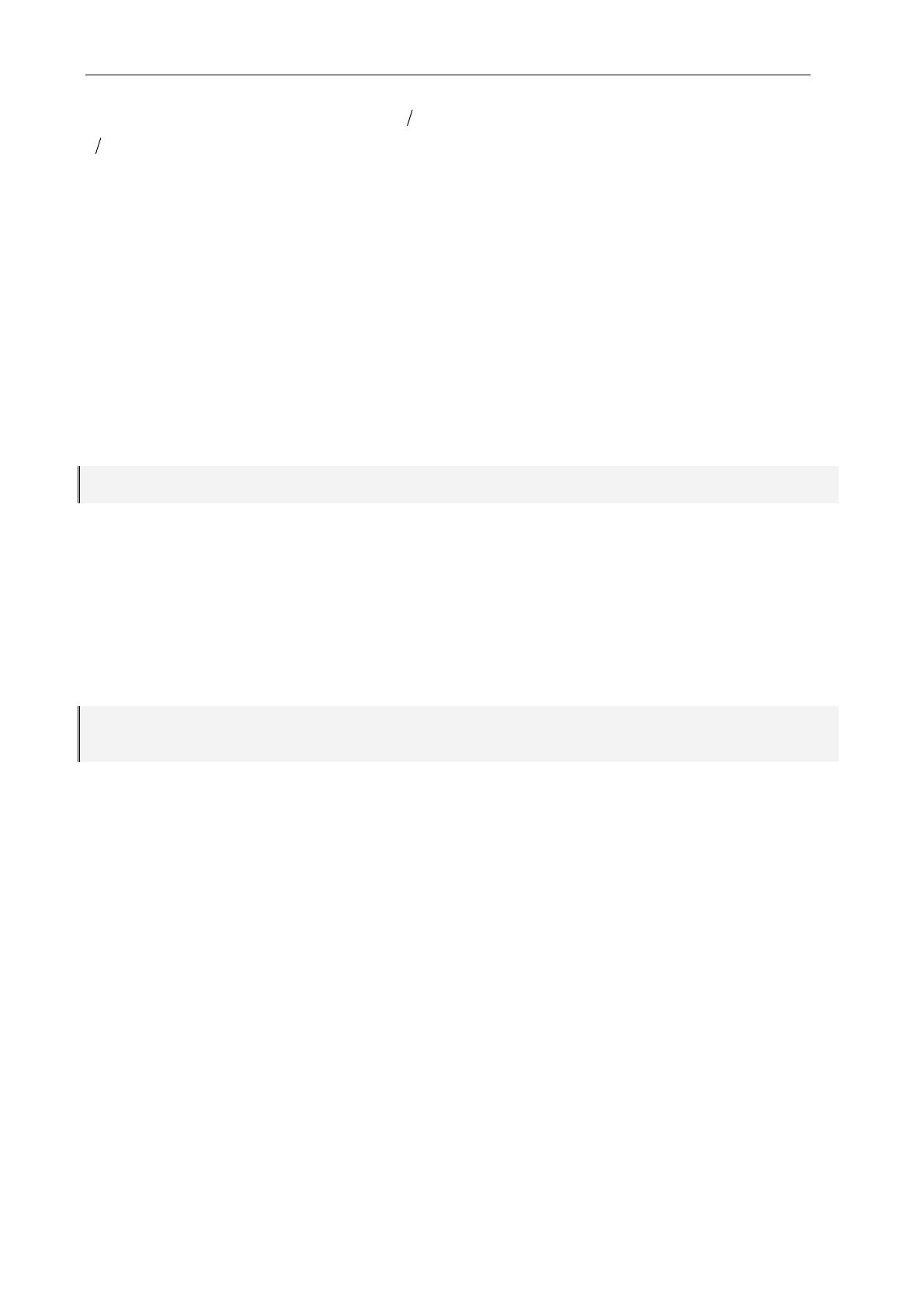
Gestion de la Maintenance 2
V1 de Werner von Braun. Un mathématicien de son équipe bouleversa son raisonnement en annonçant que
« si la probabilité de survie d’un élément est x1 , alors la probabilité de survie de n éléments identiques est
n
x1 ». C’était la fin de la théorie du maillon le plus faible. A partir de cette date, on commence alors à tenir
compte de tous les risques, et la loi anecdotique de Murphy (1949) « si un ennui a la moindre chance de
se produire, il se produira » ne fit que confirmer cette théorie :
• années 1950 : apparition du taux de défaillance, diagnostic de pannes,
• années 1960 : apparition de l’A.M.D.E.C. et de l’arbre des causes,
• années 1970 : normalisation des termes (fiabilité, maintenabilité, disponibilité), des calculs
(MTBF, MTTF, etc.), prévision des risques,
• années 1980 : approche globale de la sûreté de fonctionnement
Plus que jamais, la notion de sûreté de fonctionnement ou F.M.D.S. s’impose aujourd’hui.
1.2 – Définitions générales
Nous pouvons donner tout de suite les définitions normalisées des quatre critères F.M.D.S. (norme
NF EN 13306).
1. Fiabilité : c’est l’aptitude d'un bien à accomplir une fonction requise ou à satisfaire les besoins des
utilisateurs, dans des conditions données et durant un intervalle de temps donné.
On suppose bien sûr que le bien est en état d’accomplir la fonction requise au début de l’intervalle de temps
donné. La fiabilité se traduit donc par l’aptitude d’un bien à avoir une faible fréquence de défaillance.
Note : le terme « fiabilité » est également utilisé pour désigner la valeur de la fiabilité et peut être défini
comme une probabilité.
2. Maintenabilité : c’est l’aptitude d'un bien à être maintenu ou rétabli dans un état dans lequel il peut
accomplir une fonction requise lorsque la maintenance est accomplie dans des conditions données avec des
procédures et des moyens prescrits.
Note : le terme « maintenabilité » est également utilisé pour désigner la valeur de la maintenabilité.
3. Disponibilité : c’est l’aptitude d'un bien à être en état d'accomplir une fonction requise dans des
conditions données et à un instant donné ou durant un intervalle de temps donné, en supposant que la
fourniture des moyens extérieurs nécessaires soit assurée.
Cette aptitude est fonction d’une combinaison de la fiabilité, de la maintenabilité associée à la logistique de
maintenance du bien. Elle exprime la probabilité pour que le système accomplisse sa fonction, donc qu'il soit
exempté de fautes, à l'instant t, sachant qu'il a pu en receler auparavant.
Note : Par moyens extérieurs, on entend moyens de maintenance. Les moyens extérieurs nécessaires,
autres que la logistique de maintenance, n'affectent pas la disponibilité du bien
4. Sécurité : elle a pour but d’obtenir un système sûr de fonctionnement, c’est à dire ne risquant pas
d’occasionner la perte ou des blessures de personnes, des dommages ou des pertes d’équipement, que le
système soit en état de fonctionnement normal, dégradé ou en état de non fonctionnement.
Le concept de sécurité est en conflit avec celui de disponibilité. En effet, si on veut de la sécurité, on
aura tendance à s’entourer de protection, et à se replier dans une situation de sécurité chaque fois que l’on
aura un doute sur le bon fonctionnement, au détriment de la disponibilité. Il existe des solutions de
redondance qui assurent la sécurité, d’autres qui assurent de la disponibilité. Les solutions qui assurent les
deux sont, bien sûr, plus onéreuses.
1.3 – Soutien logistique maintenance
Par définition, la logistique est le processus stratégique par lequel l’entreprise organise et soutient
son activité. Appliquée à la maintenance, cette définition peut être exprimée de la manière suivante : « c’est
l’ensemble des moyens permettant aux techniciens de maintenance d’être efficace dans leurs actions ». La
logistique de maintenance peut se décliner en quatre volets essentiels :
• matières et produits consommables,
• pièces et modules de rechange,
• outillage spécifique,
• moyens spéciaux.
1 – Matières et produits consommables