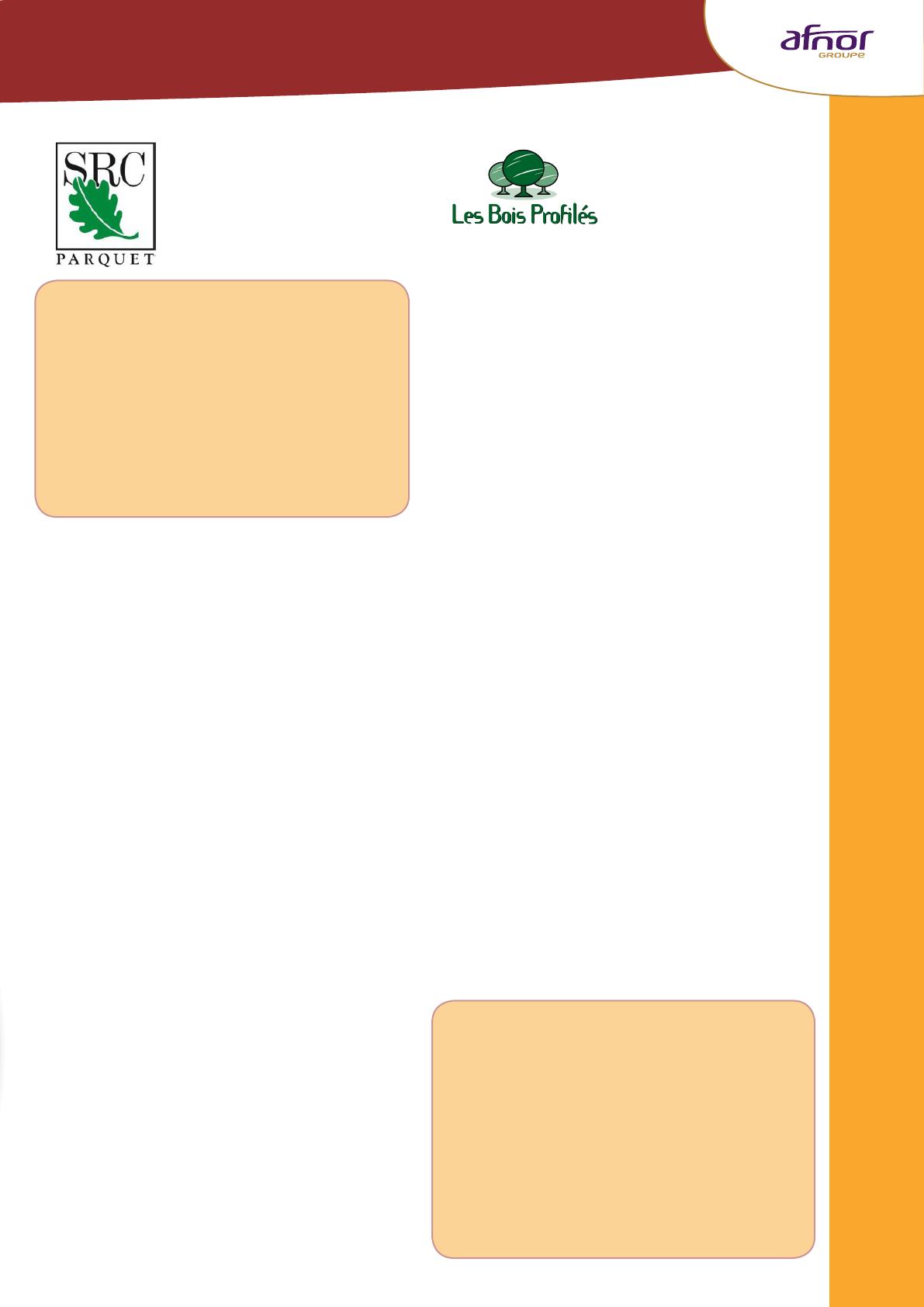
5
Région Bourgogne 2012 - 2014
Laurent Rizet, Directeur
industriel de Les Bois
Profilés, Groupe Ducerf
Changer la façon de
travailler
Nous avons profité de l’opération collective pour
développer la culture lean dans l’entreprise. En
effet, nous savions qu’il fallait progresser dans
l’organisation de la production, mais pas forcément
comment faire.
Nous avons préféré commencer par un atelier dans
lequel travaillent six salariés, pour apprécier leur
ressenti, avant de généraliser la méthode à l’entreprise.
Un atelier test en quelque sorte.
La démarche a débouché sur des améliorations très
concrètes dont beaucoup relèvent du bon sens.
L’organisation de l’atelier a été profondément modifiée,
si bien que la façon de travailler a complètement
changé. D’abord, les plannings de production sont
systématiquement transmis aux opérateurs, ce qui
n’était pas le cas auparavant. Ensuite, nous avons
fait évoluer la gestion des petites commandes qui
prenaient beaucoup de temps. Les moins rentables ont
été externalisées. Et nous groupons les commandes
en production, plutôt que de les traiter une par une
auparavant. Enfin, nous avons créé un poste de cariste
pour alimenter une machine, ce qui réduit les pertes
de temps au moment des changements de séries.
Toute cette réorganisation de l’atelier a eu un impact
positif sur la propreté et sur la circulation qui est
devenue beaucoup plus fluide.
Tout fonctionnait bien. Mais pour réaliser de nouveaux
progrès, il fallait investir, ce que nous ne pouvons pas
faire pour l’instant. Nous avons donc suspendu le lean.
En effet, si l’on ne peut pas résoudre un problème,
mieux vaut ne pas insister, sous peine de décourager
ceux qui s’investissent dans la démarche.
Nous la relancerons dès que nous aurons les moyens
d’investir. L’opération collective nous a permis de
donner une culture du lean à quatre salariés, qui
pourront la transmettre dans le reste de l’entreprise,
en animant des groupes dans d’autres ateliers.
Actions
- Améliorer l’organisation
- Gagner en visibilité sur la production
- Identifier des gains de productivité par une analyse
des coûts
Résultats
- Création d’un poste de cariste
- Rationalisation de la production sur les opérations
à plus haute valeur ajoutée
- Amélioration des conditions de travail (propreté,
rangement et circulation)
Emmanuel Laurent,
Responsable logistique
fabrication chez SRC
Un regard différent sur
l’atelier
Actions
- Identifier les blocages et goulots d’étranglement
- Mettre en place des outils de suivis et des
indicateurs
- Fiabiliser la production
Résultats
- Réduire le taux de panne
- Meilleure prise de décision
- Optimiser l’implantation
- Repenser l’ensemble des flux matière
J’avais participé à une démarche de certification ISO 9001
dans une autre entreprise. Peu de temps après mon arri-
vée chez SRC, le directeur de l’aciérie m’a proposé de
participer à cette opération collective sur le lean.
J’ai apprécié la façon parfois ludique dont la méthode
nous a été présentée. Par exemple, l’atelier des petits ba-
teaux : une quinzaine de personnes simulent une chaîne
de production pour aboutir à un petit bateau en papier.
Cela permet de voir la démarche de chacun pour arriver
au même résultat, avec plus ou moins de flux.
De même, le support du consultant a été très utile, car
il m’a aidé à me recentrer sur les questions essentielles
qui se posaient dans l’atelier.
Le lean m’a appris à porter un regard différent sur
la production, à me poser les bonnes questions. En
observant avec ce nouvel œil, il devient plus facile
de comprendre les blocages, de pointer les goulots
d’étranglement dans la production, d’autant plus que
cette observation s’appuie sur des outils de suivi. C’est
toute cette mécanique qui m’intéresse.
Par exemple, en mettant en place des fiches de suivi,
nous avons constaté qu’une machine tombait très
régulièrement en panne en cours de journée. Nous
savions qu’elle posait problème, mais nous n’en avions
jamais pris l’exacte mesure. Là, nous disposions d’un
indicateur clair qui nous a conduits à réaliser une in-
tervention importante sur cette machine pendant les
congés.
Pour l’instant, nous n’avons pas travaillé sur nos flux,
car nous attendons la livraison de nouveaux équipe-
ments d’ici quelques mois. Le lean va bien sûr nous
servir pour déterminer au mieux leur implantation et
repenser l’ensemble de nos flux matière.
Opération collective - Lean management • Bourgogne