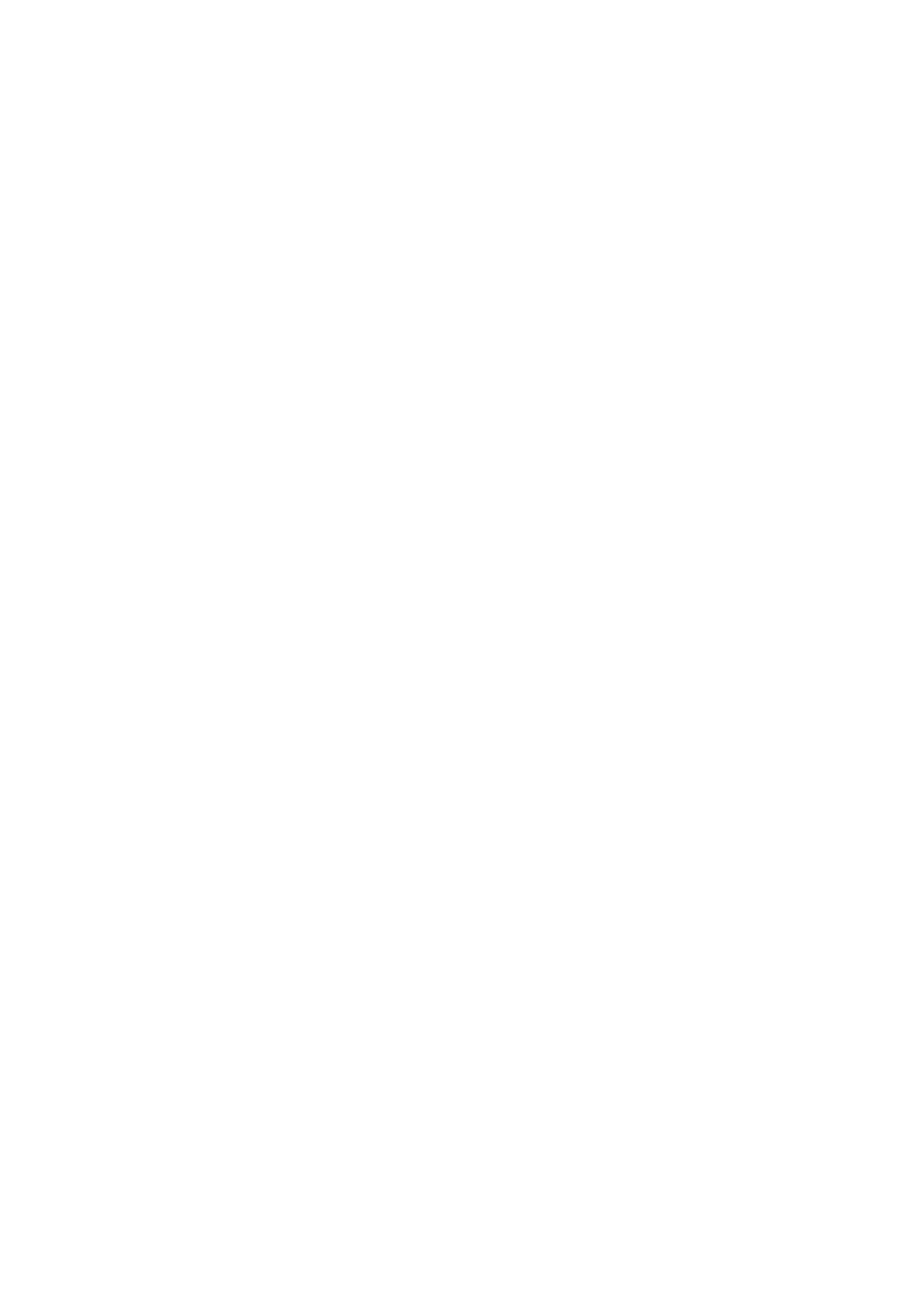
Page 5/10
Décliner ce document de façon visuelle, en
utilisant des photos, et des représentations
graphiques, fait partie de la volonté de
mettre en place un management visuel de
l’information.
POURQUOI APPLIQUER LE
LEAN MANUFACTURING EN
FORGE ?
La forge est en amont dans le processus
d’obtention des pièces. Que ce métier soit
le seul de l’entreprise (fournisseurs de
bruts) ou intégré dans un processus plus
global (pièces ou produits finis livrés), il
n’en est pas moins soumis aux lois du
marché mondial actuel qui impose de plus
en plus de flexibilité, une qualité irrépro-
chable, des coûts maîtrisés (pour assurer
la pérennité de l’entreprise confrontée à
des prix de marchés toujours plus bas),
dans une vision de développement durable
(efficacité énergétique, économies de ma-
tières, recyclabilité, etc…).
Le Lean Manufacturing est une solution qui
répond à l’ensemble de la problématique
d’amélioration du fonctionnement d’une
organisation industrielle et aux nouvelles
exigences environnementales, forge y
compris.
Sans oublier les obligations intrinsèques
aux Supply Chains, dont les têtes de filiè-
res (grands donneurs d’ordres aéronauti-
ques, ferroviaires, automobiles et autres)
imposent que les entreprises composantes
de la chaîne d’approvisionnement soient
de plus en plus réactives et respectent le
Takt time (indexé sur leur propre cycle de
production en flux tiré)
EXISTE-T-IL DES SPECIFICITES
LIMITATIVES A LA MISE EN
OEUVRE DU LEAN EN FORGE ?
Deux aspects doivent être analysés :
•Est-ce que le Lean Manufacturing
porte en son sein des limites
d’applications intrinsèques à la
méthode et aux principes de base
(issues du Toyota Production Sys-
tem) ?
•Est-ce que le métier de la Forge a
des spécificités qui empêchent de
mettre en œuvre efficacement le
Lean Manufacturing ?
Le Lean Manufacturing a-t-il des limites
d’applications ?
La description résumée de la méthodolo-
gie/philosophie Lean proposée en premier
chapitre ne fait aucune distinction de pro-
cédés ou de typologies de production pour
sa mise en œuvre.
Le Lean fait ouvrir les yeux et découvrir le
réel, quel que soit l’entreprise.
La réalisation de la cartographie des flux
de valeur s’applique à n’importe quelle
entreprise manufacturière et même de
services (Lean Office).
Le Lean est un guide et chaque application
est différente. Il n’y a pas deux entreprises
identiques, que ce soit par l’outil de pro-
duction ou par les relations interpersonnel-
les et le profil de compétences des hom-
mes et des femmes qui les constituent.
Dès lors, la comparaison entre deux entre-
prises, centrées sur la forge par exemple,
n’a aucun sens.
L’intérêt du Lean est de s’améliorer, ou
plutôt d’apprendre à s’améliorer.
Certains auront des résultats énormes,
empêtrés qu’ils étaient dans leurs habitu-
des de travail d’un monde dépassé.
D’autres auront des résultats plus limités.
Qu’importe ! Des gains seront apparus et
la dynamique du progrès sera amorcée,
pour la plus grande satisfaction du client
qui les fait vivre.
La forge a-t-elle des spécificités
contraignantes pour la mise en œuvre
du Lean Manufacturing ?
Le monde de la forge est complexe. Il est
constitué d’un ensemble de procédés diffé-
rents (forge à chaud, frappe à froid, forge
libre, estampage des aciers, matriçage des
non-ferreux, etc….) transformant géomé-
triquement et métallurgiquement des ma-
tières diverses (aciers et alliages légers)
pour obtenir des produits dont la masse
peut varier de quelques centaines gram-
mes à plusieurs tonnes.
On peut s’attendre à des contraintes limita-
tives assez fortes de l’amélioration des
processus d’obtention de produits.
Quelques exemples possibles :
•Le travail à chaud (manipulation de
pièces à haute température, pro-
cédés dangereux ou, pour le
moins, imposant des conditions de
travail humain difficiles,