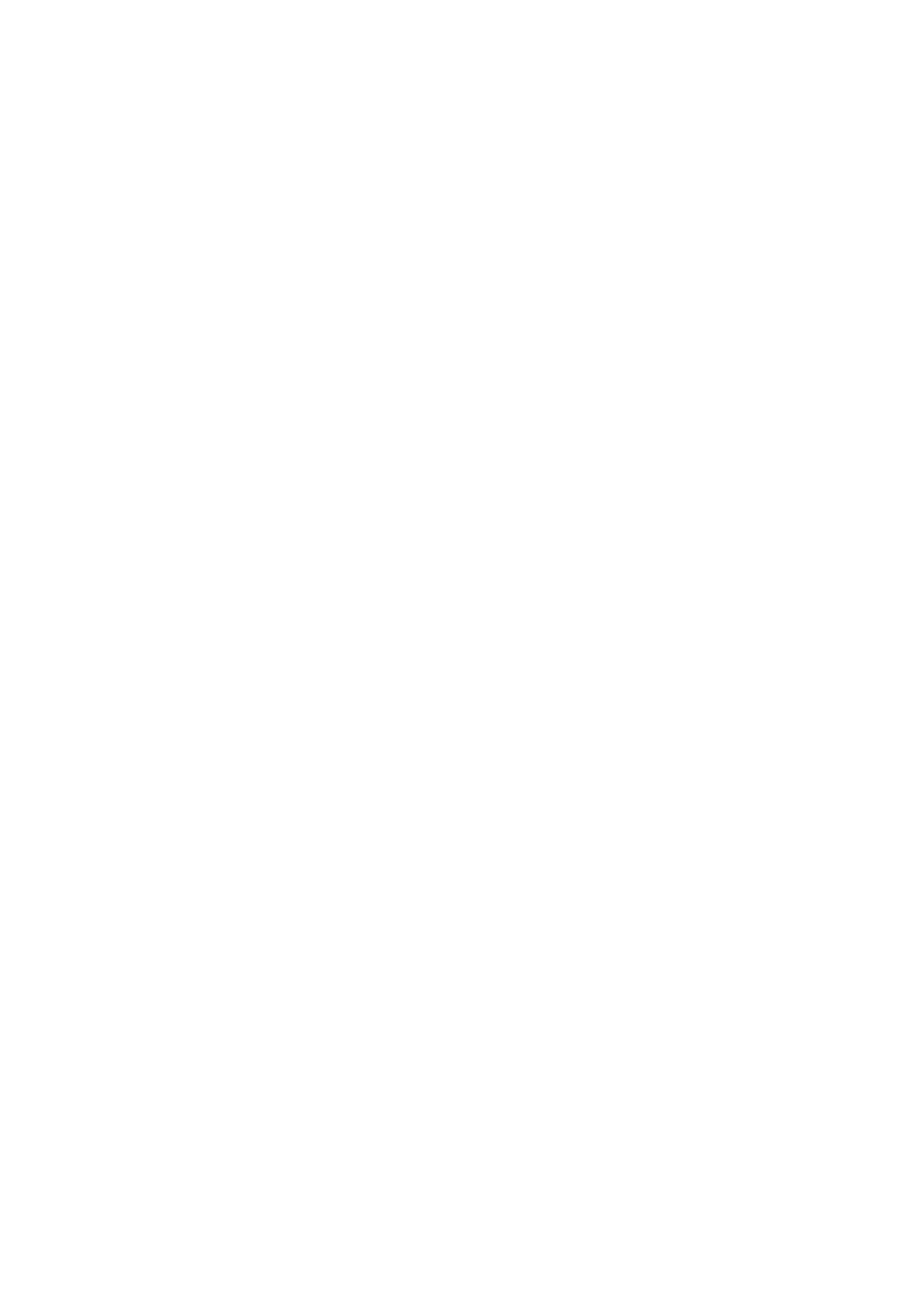
Merci à l’ensemble des personnes qui ont contribué à l’avancement de mes travaux au sein
du laboratoire IREENA, et plus particulièrement le Professeur Joseph SAILLARD, directeur
de l’IREENA pour ses conseils, ainsi que pour m’avoir fait partager sa bibliothèque
personnelle riche de précieux ouvrages. A Marc BRUNET, ingénieur à l’IREENA et Sandrine
CHARLIER, secrétaire de l’IREENA, qui m’ont apporté une aide précieuse pour les besoins
matériels et administratifs.
Je tiens à remercier l’ensemble des membres de l’IMN pour leurs contributions et leur
soutien, et en particulier M. Christophe CARDINEAU, maître de conférence/HDR à
l’université de Nantes et Mme Michèle CARETTE, maître de conférences à l’école
polytechnique de l’université de Nantes pour l’intérêt qu’ils ont porté à mon travail.
M. Yann MAHE, Maître de conférences à l’école polytechnique, M. Hartmut GUNDEL,
Professeur à l’université de Nantes, et M. Reynald SEVENO, Maître de conférences à
l’université de Nantes, pour les conseils qu’ils ont pu m’apporter durant ces travaux.
Je souhaite également remercier les membres de l’entreprise MHS Electronics qui m’ont
accueilli pour effectuer ce doctorat. En particulier, M. Alain CHARPENTIER, expert
technique, dont la contribution aura été majeure dans les orientations de ce travail. Son
expérience, sa rigueur et ses grandes compétences techniques m’auront beaucoup apporté
durant ces années de thèse. M. Gérard GADOT, directeur du département R&D de MHS
Electronics pour m’avoir accueilli dans son équipe. Tous les membres de l’entreprise pour
leur accueil, leur disponibilité, leur support technique, en particulier M. Thierry THEBAULT,
M. Fréderic LAINAT, M. Sun ONG MOK, Mme Sophie D’ALBERTO, M. Pascal
KROPFELD et tous les autres…
Merci à Mme Maryline GUILLOUX-VIRY, Professeur à l’université de Rennes et Mme
Stéphanie DEPUTIER, Maître de conférences à l’université de Rennes pour leurs
contributions et leur soutien durant ces travaux.
Je remercie tous mes collègues et amis du laboratoire, en particulier mon grand ami
Hongyang HE, qui m’a toujours été d’extrêmement bon conseils. Biyun, Julien, Atef, Ahmad,
Haitao, Janic, Gildas, Nicolas, Yuehua… Entre humour, conseils et soutien, les moments
passés à vos côtés me manqueront...
A ma famille, mes parents, ma sœur sans qui je n’aurais jamais pu réussir. Je les remercie
pour tous les sacrifices qu’ils ont fait, et pour le soutien sans bornes qu’ils m’ont apporté
durant mes études et pas seulement. Que vous soyez fiers de moi à toujours été un moteur
dans ma vie, merci à vous trois.
Je remercie également ma belle famille et en particulier Julie, qui dés qu’elle le peut,
n’hésite pas à faire mon éloge et ma promotion autour d’elle : si j’ai un jour besoin d’un
agent, je t’engage !
Enfin, j’adresse ma profonde gratitude à mon Angélique, pour ses conseils, ses
contributions, son soutien dans tous mes projets, et cela, avec tous les sacrifices qu’ils
impliquent. Grace à toi, ces années auront vraiment été belles et heureuses.