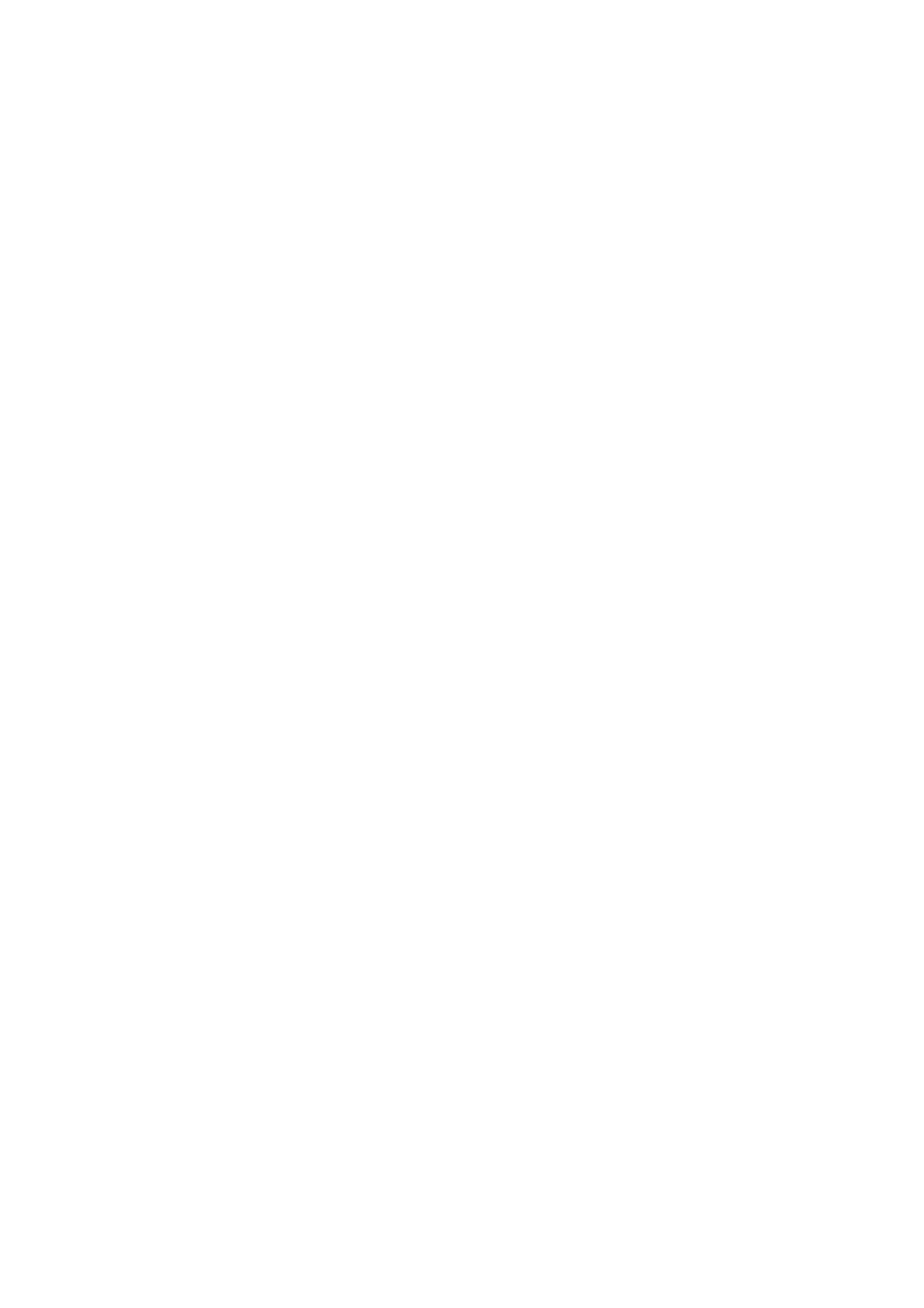
Remerciements
Cette thèse a été réalisée au Laboratoire de Chimie Appliquée et de Génie Chimique,
de l’université de Tizi Ouzou UMMTO, en collaboration avec le laboratoire des Matériaux,
Surfaces et Procédés pour la Catalyse (LMSPC) de l’École Européenne de Chimie,
Polymères et Matériaux (ECPM) de Strasbourg. Elle a été menée grâce à l’aide de très
nombreuses personnes que je tiens à remercier.
Je voudrais tout d’abord remercier Mr TEZKRATT Said, Directeur du Laboratoire de
Chimie Appliquée et Génie Chimique de l’université de Tizi-Ouzou pour la qualité de son
encadrement, pour sa disponibilité, les longues discussions constructives et ses
encouragements durant cette thèse.
Je tiens également à remercier Monsieur le Professeur Alain KIENNEMANN de
m’avoir accueilli dans son laboratoire (LMSPC, Strasbourg), de la qualité de sa
collaboration, son aide, sa confiance et pour ses nombreux conseils.
Je voudrais remercier chaleureusement Madame CERIFI Ouiza, Professeur à
l’Université de Boumerdès (UMBB), pour l’honneur qu’elle m’a fait de juger ce travail.
J’ai été très honoré de la participation de Madame DELLAH Saliha Maîtres de
Conférences à l’Université de Tizi-Ouzou (UMMTO) à mon jury de thèse que je remercie
vivement. Je lui suis également reconnaissante de m’avoir initié pour mes travaux de
recherche.
Je souhaite remercier également Madame HALLICHE Djamila Professeur à
l’Université de Bab-Ezouar (USTHB) pour avoir accepté de juger ce travail.
Je remercie tout le personnel du laboratoire des Matériaux, Surfaces et Procédés pour
la Catalyse (LMSPC) de l’École Européenne de Chimie, Polymères et Matériaux (ECPM) de
Strasbourg pour m’avoir aidé pour effectuer les différentes techniques de caractérisations.
Un grand merci à mes amis (es) et collègues du LCAGC et de LMSPC de Strasbourg
pour leur amitié, leur aide et leur soutien.