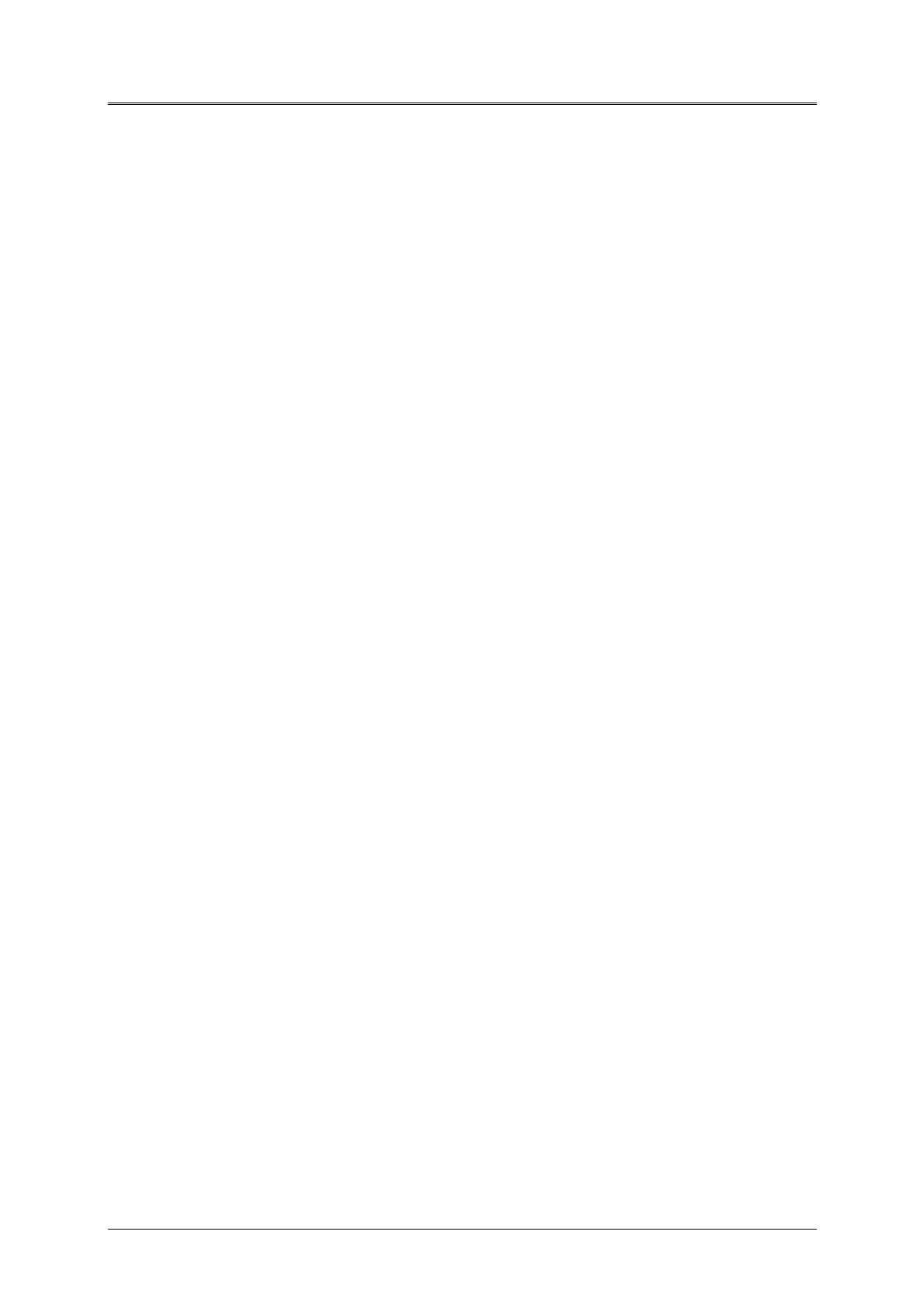
Remerciements
Les travaux présentés dans ce mémoire ont été réalisés au Laboratoire d’Etudes et de
Recherche sur les Matériaux, les Procédés et les Surfaces (LERMPS) de l’Université de
Technologie de Belfort-Montbéliard. Mes remerciements s’adressent à Monsieur le
Professeur C. Coddet, Directeur du LERMPS, d’avoir accepté de présidé Le jury de thèse
ainsi que de m’avoir accueillie au sein de son équipe et de m’avoir accordé sa confiance pour
mener à bien mes travaux de recherches.
Je remercie vivement Monsieur le Professeur D. Klein d’avoir assuré l’encadrement des
travaux et je lui suis très reconnaissante pour le soutien qu’il m’a apporté et les précieux
conseils qu’il m’a prodigués tout au long de cette thèse. Aussi, j’adresse mes sincères
remerciements à Monsieur le Professeur B. Benyoucef, Directeur de l’Unité de Recherche
Matériaux et Energies Renouvelables (URMER) de l’Université Abou-bakr Belkaïd de
Tlemcen, de m’avoir intégrée au sein de son équipe et d’avoir assuré la codirection de ces
travaux de thèse.
Mes remerciements vont aussi à la Communauté d’Agglomération du Pays de
Montbéliard ( CAPM ) pour avoir financé mes travaux.
Je remercie Messieurs les professeurs J- P. Charles, de l’ Université Paul Verlaine de
Metz et B. Khelifa, de la Faculté Jean Perrin de l’Université d'Artois, pour avoir accepté
d’être rapporteurs de cette thèse, et pour l’intérêt qu’ils ont manifesté à l’égard de ce travail.
Je suis reconnaissante à Messieurs les professeurs N-E. Chabane-Sari et S. Ghalem de
l’Université Abou-bakr Belkaïd de Tlemcen ainsi qu’à Monsieur F. Lapostolle, Maître de
conférences à l’Université de Technologie de Belfort-Montbéliard, d’avoir accepté
d’examiner ce travail.
Je remercie aussi Madame S. Lamy ainsi que Monsieur O. Rapaud pour leurs
dévouement et aide précieuse pour la caractérisation des dépôts.
Que messieurs P. Vernoux, de l’Université de Lyon 1 et N. Martin de L’ENSMM de
Besançon, trouvent ici mes sincères remerciements pour les mesures de surfaces spécifiques et
de résistivité à haute température, respectivement.