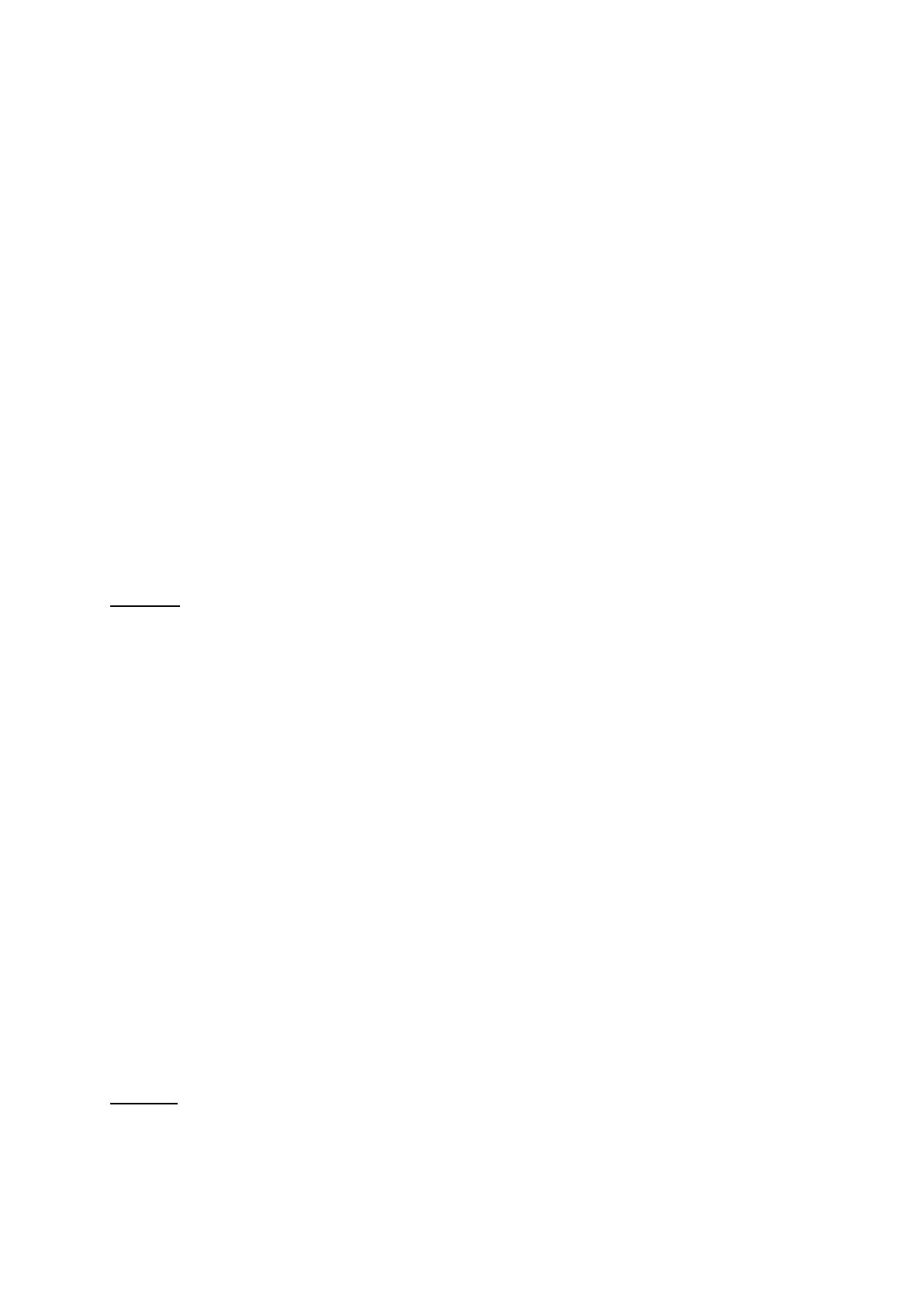
3
Nouvelles stratégies catalytiques pour la gazéification de la biomasse :
Influence de métaux imprégnés sur les mécanismes de pyrolyse
Résumé
Le développement des voies de valorisation de la biomasse par gazéification, très prometteuses pour la
production de biocarburants, est ralenti à cause de la concentration trop élevée de goudrons dans le gaz
produit par ce procédé. Des travaux récents ont montré que les métaux, lorsqu’ils sont imprégnés dans la
biomasse, limitent la génération des goudrons primaires, produits lors de l’étape de pyrolyse qui précède les
réactions d’oxydation. L’objectif principal de ce travail est d’étudier l’influence des métaux imprégnés sur les
mécanismes de pyrolyse et sur les rendements en goudrons de cette étape. La réactivité du char formé, qui est
dopé en métal, par rapport aux réactions d’oxydation a également été évaluée. L’étude de l’influence du fer et
du nickel sur la pyrolyse des principaux polymères qui constituent la biomasse (cellulose, xylane, lignine) et
d’échantillons de biomasses a permis de mettre en évidence que les métaux favorisent principalement les
mécanismes de formation du char, ce qui inhibe les réactions de dépolymérisation et de fragmentation,
responsables de la production des goudrons. Imprégné dans les phases amorphes des polysaccharides, le nickel
catalyse aussi des réactions de dépolymérisation. Ce résultat explique que la réduction des rendements en
goudrons soit plus forte avec le fer qu’avec le nickel. Par contre, le nickel est plus efficace pour limiter la
production des molécules contenant un noyau benzénique et pour catalyser des réactions secondaires des
matières volatiles, comme le reformage à la vapeur. Lors des expériences de gazéification de char dopé en fer,
des problèmes de désactivation du catalyseur métallique, qui conduisent à un ralentissement de la cinétique de
la réaction d’oxydation, sont observés. Au contraire, l’activité catalytique du nickel est stable et rend possible
les réactions d’oxydation du char au CO2 à 600 °C et à la vapeur d’eau à 500 °C. Ces résultats indiquent que
l’approche, qui consiste à imprégner des métaux dans la biomasse, permet d’envisager la mise en œuvre de
procédés de gazéification à basse température ; ce qui limiterait le problème des goudrons et permettrait
d’améliorer l’efficacité énergétique des procédés.
Mots-clés : pyrolyse, biomasse, goudrons, catalyse, nickel, fer, cellulose, lignine, hémicelluloses, gazéification,
char dopé en métal.
New catalytic strategies for biomass gasification:
Influence of impregnated metals on pyrolysis mechanisms
Abstract
The very promising development of the use of biomass for biofuel production by gasification is slowed down
owing to too high tar concentration in the gas produced by this process. Recent works showed that, when
impregnated in biomass, metals display catalytic activity that results in a significant decrease in the production
of the primary tars, during the pyrolysis step, which precedes the oxidation reactions. The main aim of this
work was to assess the effect of impregnated metals on pyrolysis mechanisms and on the tar yield of this step.
The reactivity of the metal-doped char produced, during the oxidation reactions, was also evaluated. The study
of the influence of iron and nickel on the pyrolysis conversion of the main polymers that form biomass (i.e.
cellulose, xylan and lignin) and of biomass samples showed that impregnated metals mainly catalyzed the
mechanisms of char formation. This phenomenon inhibited the depolymerization and fragmentation reactions,
which are responsible for most tar formation. When impregnated in the amorphous phase of the
polysaccharides, nickel also promoted some depolymerization reactions. This result explains the bigger
decrease in tar production obtained with iron than with nickel. However, nickel was more efficient in limiting
the production of molecules containing a benzene ring and to catalyze the secondary reactions of volatile
compounds. During gasification tests, the conversion of the iron-doped char revealed problems of deactivation
of the metal catalyst, which led to a decrease in the reaction rate of the oxidation reaction. On the contrary,
the catalytic activity of nickel was stable and made possible the oxidation reactions of char at 600 °C with CO2
and at 500 °C with steam. These findings show that the approach which consists in impregnating biomass with
metals, allows considering the implementation of gasification processes at low temperature, which could limit
the tar problem and could improve the energy conversion efficiency of these processes.
Keywords: pyrolysis, biomass, tar, catalysis, nickel, iron, cellulose, lignin, hemicelluloses, gasification, metal-
doped char.
Laboratoire Biomasse Energie et Biocarburants (2iE) / Transformations Intégrées de la Matière Renouvelable
(UTC)