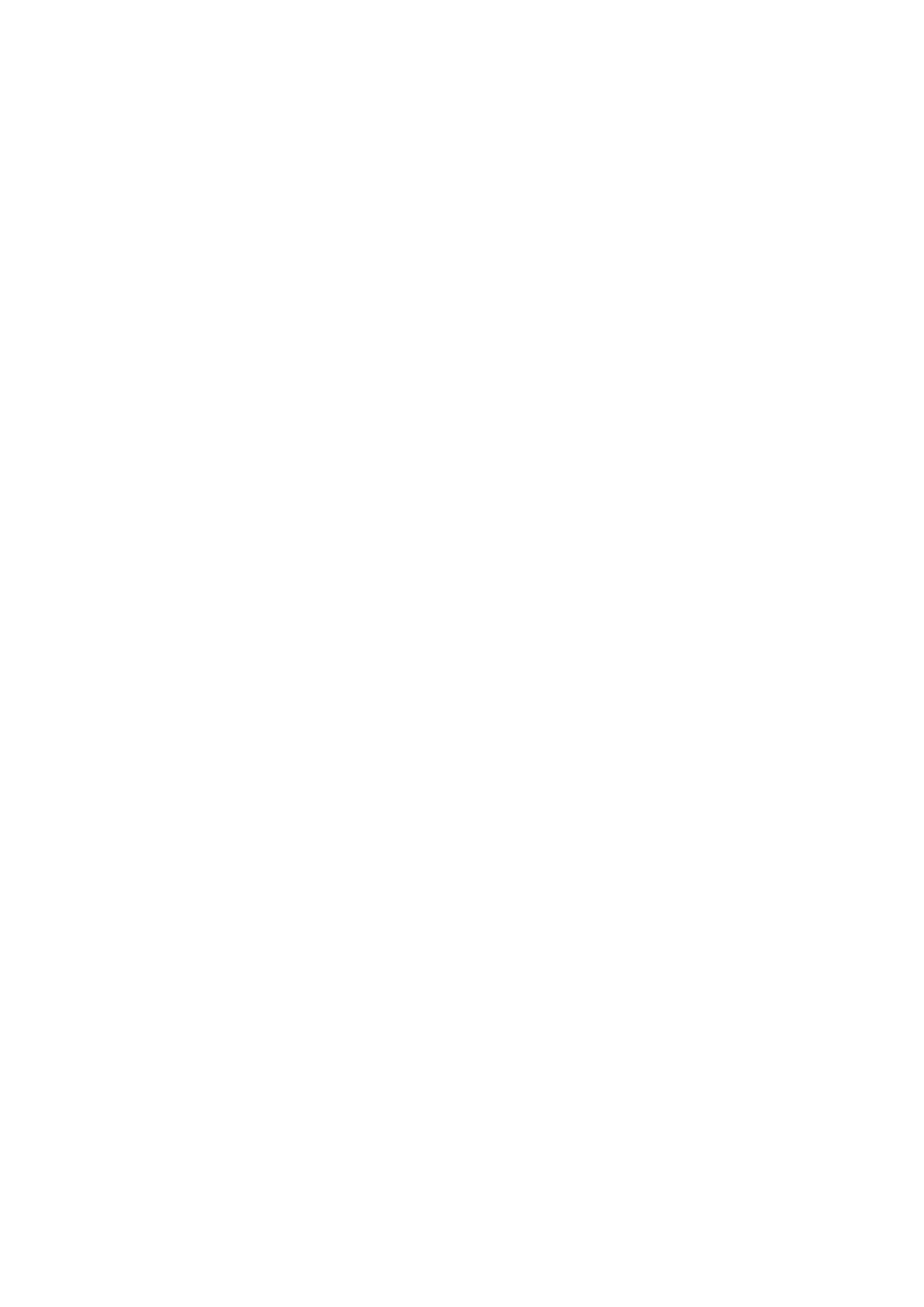
CHAPITRE II
TECHNIQUES EXPERIMENTALES
I. Introduction ............................................................................................................... 43
II. Techniques de caractérisation structurale et texturale des catalyseurs…………….43
II.1. Diffraction des rayons X .................................................................................... 43
II.1.1. Principe de la méthode ................................................................................ 43
II.1.2. La loi de Debye-Scherre .............................................................................. 44
II.1.3. Dispositif expérimental ............................................................................... 44
II.2. Spectroscopie infrarouge (FTIR) ....................................................................... 45
II.1.1. Principe de la technique .............................................................................. 45
II.1.2. Spectre infrarouge ....................................................................................... 46
II.1.3. Type d’appareil ........................................................................................... 46
II.3. Mesure de la surface spécifique par la méthode BRUNAUER-EMMET-
TELLER (BET) ............................................................................................................ 47
II.4. Microscopie électronique à balayage (MEB) ..................................................... 49
III. Description du test catalytique……………………………………………………………50
III.1. Test catalytique……………………………………………………………………….50
III.2. Méthodologie d’analyse chromatographique…………………………………………52
III.2.1. Etalonnage chromatographique…………………………………………………..52
III.2.1.1. Temps de rétention de chaque gaz…………………………………………..52
III.2.1.2. Calcul des facteurs de réponse Kfi de chaque gaz analysé…………………..53
III.3. Mise en œuvre du test catalytique…………………………………………………….54
III.3.1. Activation du catalyseur………………………………………………………….54
III.3.2. Réaction catalytique....................................................................................….......54
III.4. Formules de calcul…...………………………………………………………………54
III.4.1. Composition des mélanges gazeux ( Xi )….……………………………………..54
III.4.2. Le taux de conversion……………………………………………………………55
III.4.3. Sélectivité en (%)………………………………………………………………...55
III.4.4. Estimation de la productivité de CO (n CO)…………………………….........56
III.4.5. Bilan théorique des produits carbonés…………………………………...56
Références bibliographiques…………………………………………………………58
CHAPITRE III
SYNTHESE ET CARACTERISATION
DES CATALYSEURS
I.Intoduction ................................................................................................................. 59
II. Description de la méthode de préparation ................................................................ 59
II.1. L’imprégnation .................................................................................................. 59
II.2. Le séchage ......................................................................................................... 59
II.3. La calcination .................................................................................................... 60
II.4. L’activation ....................................................................................................... 60
III. Synthèse des catalyseurs ......................................................................................... 60