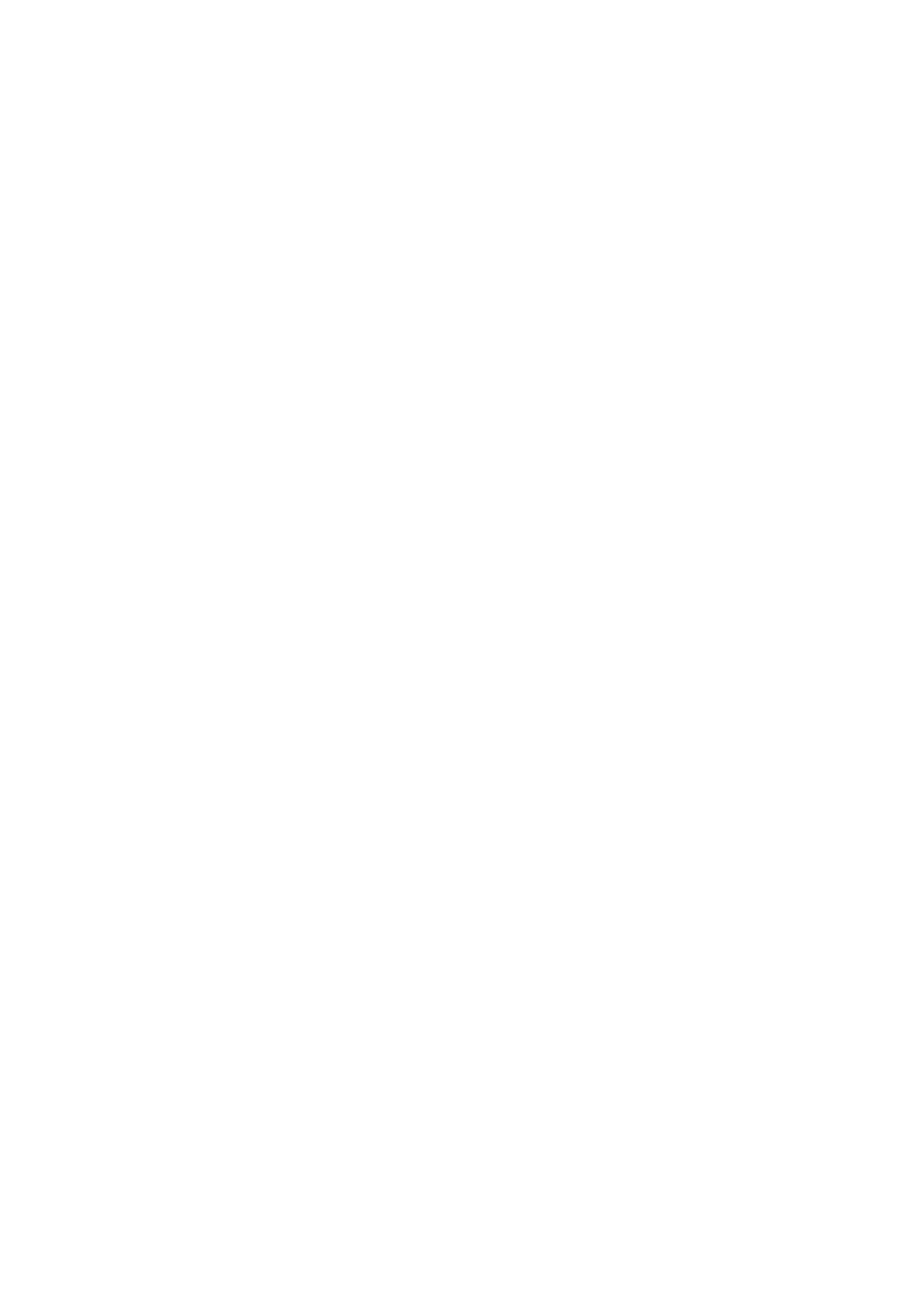
Table des matières
Résumé v
1 Introduction 1
1.1 Communications par fibres optiques ...................... 1
1.2 Lasers accordables à bas coût pour les communications optiques ...... 4
1.3 Filtres accordables à bas coût pour les communications optiques ...... 5
1.4 Objectifs et déroulement de la thèse ...................... 7
2 Matériaux et techniques 11
2.1 Cristaux liquides ................................ 11
2.2 Alignement des cristaux liquides ........................ 15
2.2.1 Alignement par brossage ........................ 15
2.2.2 Photoalignement ............................ 16
2.3 Cristaux liquides polymérisables ........................ 23
2.4 Fluide pour déposer des espaceurs ....................... 26
2.5 Adhésifs optiques ................................ 30
2.6 Photolithographie ................................ 31
2.7 Résines positives diazonaphtoquinone-novolac ................ 33
2.8 Discussion .................................... 35
3 Microtechnologie pour fabriquer des puces laser accordables incluant
une couche de PDLC intra-cavité 37
3.1 Matériaux PDLC pour les cavités optiques .................. 37
3.1.1 Présentation des matériaux PDLC .................. 37
3.1.2 Mesure des pertes du matériau .................... 38
3.1.3 Mesure de la variation d’indice .................... 41
3.2 Structure laser ................................. 45
3.3 Dépôt du PDLC ................................ 48
3.4 Matériaux antiadhésifs ............................. 50
3.5 Problèmes rencontrés .............................. 54
3.5.1 Dégorgement du PDLC ......................... 54
3.5.2 Dépôt du miroir de Bragg ....................... 54
3.5.3 Capot de protection .......................... 56
3.6 Transfert du miroir de Bragg par collage ................... 57
3.7 Discussion .................................... 65
iii