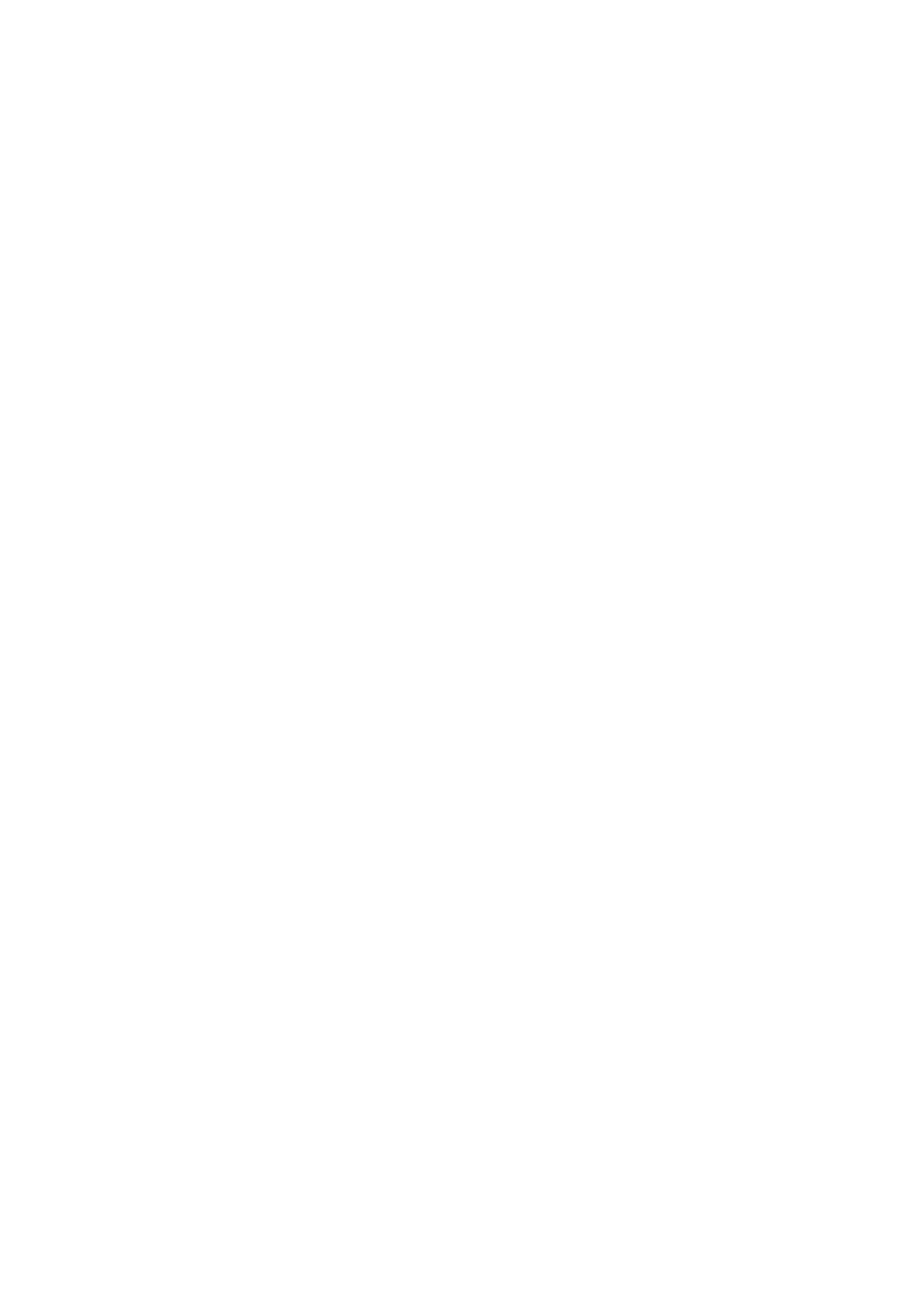
Liste des figures :
Figure -1- : Marché mondial des catalyseurs
Figure -2- : Description de l’acte catalytique en catalyse hétérogène.
Figure -3- : Etapes de formation des gels
Figure -4- : Evolution de la viscosité d’un gel au cours de la transition sol-gel
Figure -5- : Interface liquide – vapeur pour un pore cylindrique.
Figure - 6-: Formation d’un xérogel
Figure -7- : Formation d’un aérogel.
Figure -8 -: Structure interne d’un aérogel
Figure -9- : Structure cristallographique de WO3
Figure -10-: Structure cristallographique de MoO3
Figure -11-: Structure cristallographique MoO2
Figure -12- : Structure cristallographique WO2
Figure-13- : Isomérisation du 2-méthylpentane en 3-méthylpentane par déplacement
de liaison
Figure-14- :Isomérisation du 2-méthylpentane en 3-méthylpentane selon un
mécanisme cyclique
Figure -15- : Mécanisme d’isomérisation bifonctionnelle
Figure -16- : Etapes de préparation des xérogels
Figure -17- : Etapes de préparation des aérogels
Figure -18- : Diffractogrammes des catalyseurs
Figure -19- : Spectres infrarouge des catalyseurs
Figure -20- : Adsorption-désorption de
Figure -21- : Comparaison des surfaces spécifiques des 3 séries de catalyseurs
Figure -22- : Comparaison des volumes poreux des 3 séries de catalyseurs
Figure -23- : Comparaison des acidités des 3 séries de catalyseurs
Figure -24- : Photons MEB des catalyseurs
Figure -25- : Schéma expérimental de l’installation