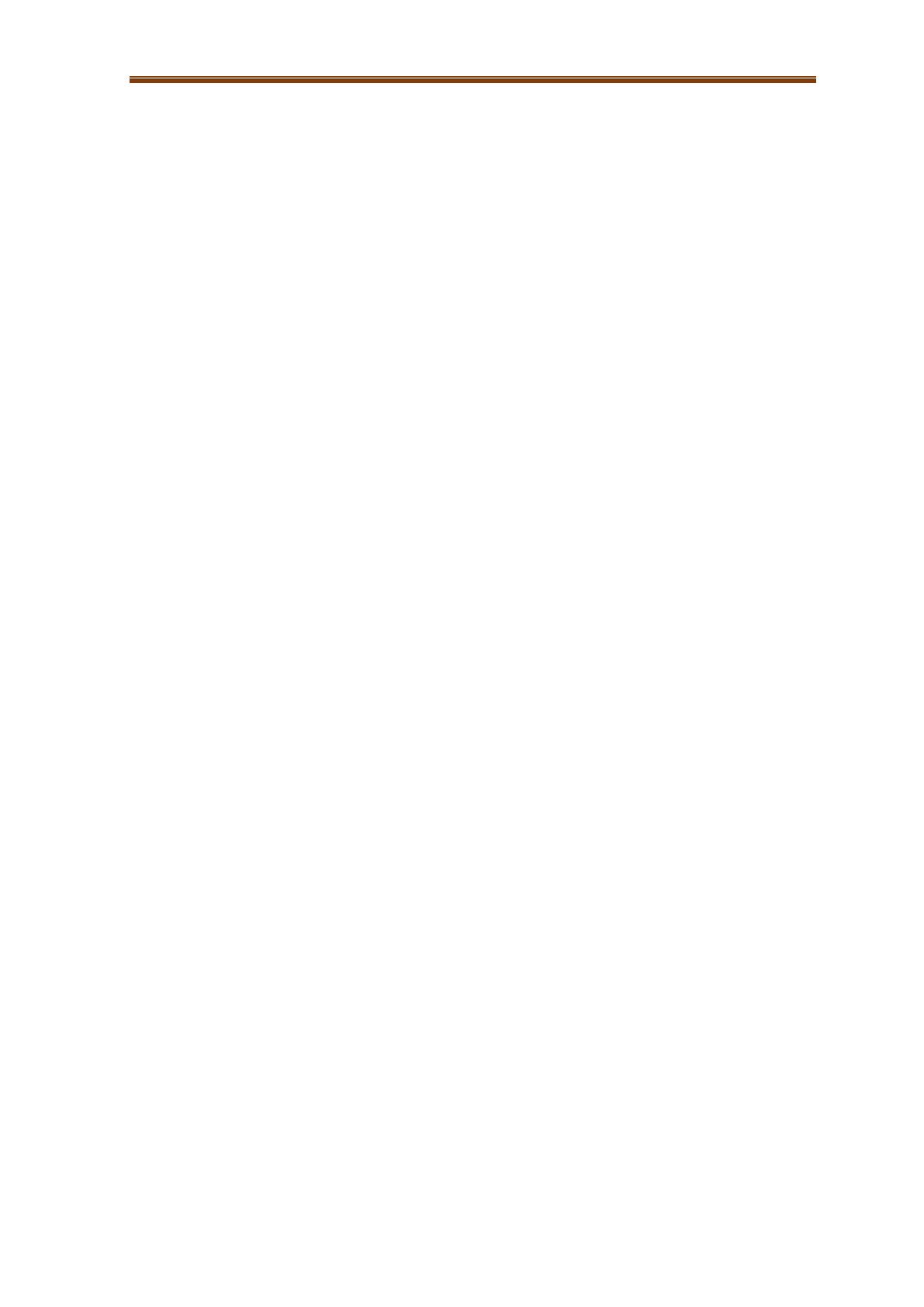
Sommaire
CHAPITRE II : REVEVETENT CHIMIQUE DU NICKEL
.
II.1- Introduction ...........................................................................................
II.2- Historique ..............................................................................................
II.3- Formulation de la réaction des dépôts ................................................
II.4-Principe
II.4.1- les procédés par déplacement ....................................................................
II.4.2- Les procédés par contact ...........................................................................
II.4.3- Les procédés par réduction chimique .......................................................
II.4.3.4- Nickelage chimique en milieu hypophosphite .......................................
II.5- Influence des paramètres expérimentaux sur le bain chimique. ......
II.5.1- Effet de pH ..................................................................................................
II.5.2- Influence de la température ......................................................................
II.5.3- Effet de la concentration en phosphore du bain ......................................
II.5.4- Influence des complexant ...........................................................................
II.5.5- Effet des stabilisateurs ..............................................................................
II.6-Caractéristiques des dépôts ..................................................................
II.6.1- Caractéristiques mécaniques ............................................................
II- Epaisseur ...........................................................................................................
II- Dureté .....................................................................................................
II- Adhérence .............................................................................................
II- Ductilité ..................................................................................................
II.6.1.5- résistance aux frottements ............................................................
II.6.2- Caractéristiquesphysiques ........................................................
II.6.2.1- Aspect ..............................................................................................
II.6- Susceptibilité magnétique ..............................................................
II.6.2.3- Résistance à la corrosion ................................................................