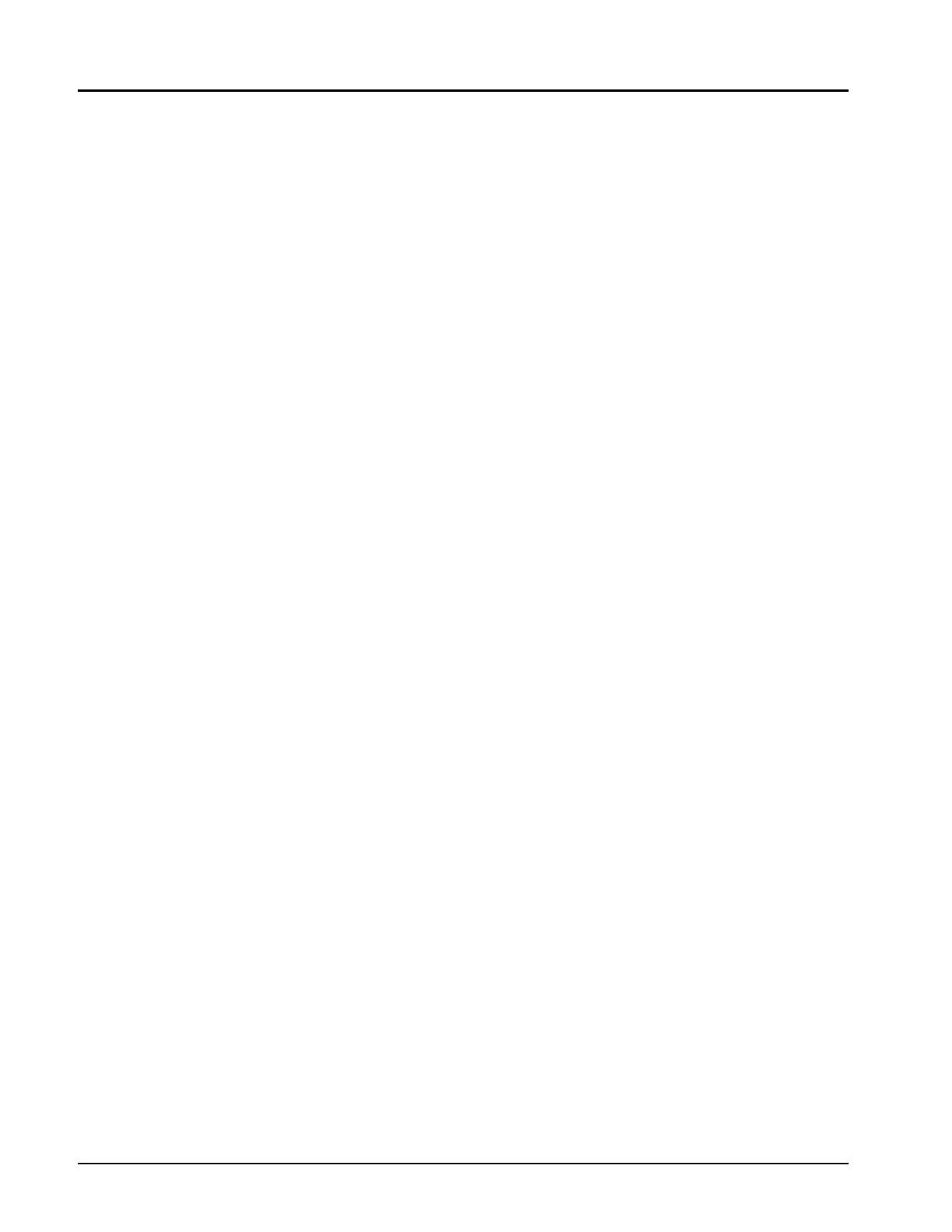
Causes et analyse des défaillances de stators et de rotors
des moteurs à induction à courant alternatif Fiche technique no 31
TN31-4
d’effet couronne en deçà de certaines limites afin d’assurer
au moteur une longévité appropriée. Par contre, l’utilisateur
peut également apporter sa contribution en maintenant le
moteur propre et frais autant que possible. L’utilisateur
devrait aussi apprendre à identifier ce type de défaillance.
D. Tensions transitoires
Au cours des dernières années, une preuve substantielle
a été cumulée que de nombreux moteurs se trouvent
exposés à des tensions transitoires ou à une alimentation
de tension à surface d’onde prononcée, ce qui entraîne une
longévité de bobinage réduite ou des bris prématurés (soit
de spire à spire, soit de spire à mise à la terre). Ces
tensions transitoires peuvent provenir de n’importe quelle
des sources suivantes :
1. Défauts de phase à phase, phase à mise à la
terre, phases multiples à la terre ou de terne qui
provoquent des tensions excessives pouvant
atteindre 3-1/2 fois leurs valeurs-seuils normales
dans des temps d’échauffement extrêmement
courts.
2. Rétablissements à répétition par lesquels le
système se trouve coupé de la mise à la terre, ce
qui crée une mise à la terre intermittente du
circuit, source d’oscillations de haute tension et de
multiplication.
3. Coupe-circuit limiteur de courant par lequel il y a
interruption de courant quand l’énergie
emmagasinée d’un champ magnétique dans
l’inductance du circuit n’est pas égale, ce qui
entraîne des oscillations de tension et une
certaine résonance.
4. Transferts rapides de barre omnibus. À la suite
d’un transfert, le bobinage d’un moteur peut subir
la différence de vecteur entre la tension de
réserve de la barre et la tension décroissante
produite.
La tension nette sera fonction de l’angle de phase entre
la tension de la barre omnibus et celle du moteur au
moment de la nouvelle coupure. La tension efficace
maximale obtenue peut être de 200 %. L’angle de phase
entre le rotor et la barre omnibus de réserve se voit modifié
continuellement à mesure que la fréquence entre le moteur
désalimenté chute lors du ralentissement.
5. Ouverture et fermeture de disjoncteurs. Cette
surtension de démarrage demeure présente en
permanence. Il peut y avoir production d’une onde
de choc qui circulera dans le circuit à un rythme
donné lorsque, à la fermeture d’un contact de
disjoncteur, il se forme un arc en raison d’une
différence de potentiel aux contacts du
disjoncteur. Cet arc influera sur l’onde de tension
qui pénétrera dans le circuit du moteur. Des
surtensions peuvent aussi survenir quand les
disrupteurs ne s’engagent pas simultanément et
qu’il y a rebondissements ou vibrations, pour créer
une onde de tension irrégulière de type surtension
(similaire aux rétablissements à répétition).
L’utilisation de dispositifs de commande de
moteurs à haute vitesse, comme des contacteurs
à vide, provoque des surtensions prononcées
lorsqu’il y a « hachure de courant » due à
l’ouverture des contacts dans un vide, sans arc
pour maintenir le courant.
6. Commutation de condensateur. En présence de
condensateurs utilisés en vue d’améliorer la
puissance, il peut y avoir création de surtensions
quand ces derniers sont constamment mis hors
circuit et en circuit. Les surtensions surviennent à
mi-cycle après l’interruption, au moment où les
contacts d’ouverture de l’interrupteur présentent
deux fois la tension de phase de pointe normale.
Puisque la tension du condensateur tient bon durant le
premier instant, la tension du système passera outre celle
du condensateur et une oscillation haute fréquence
débutera.
Des extracourants à tension extrêmement élevée
peuvent se manifester lorsque, par exemple, un moteur et
un condensateur sont mis simultanément hors circuit et se
trouvent coupés de la source d’alimentation. L’ampleur de la
surtension est fonction de la valeur de la capacité. Des
condensateurs activés avec un moteur sont source
d’excitation aux bornes du moteur et il y a induction de
tensions élevées. Ce problème se fait généralement
important dans les circuits à haute inertie où la réduction de
vitesse constitue un facteur d’excitation continue.
7. Défaillance d’isolement. Lorsqu’un bris ou une
perforation de l’isolement d’un système électrique
survient à des endroits autres qu’au moteur, des
surtensions de choc peuvent se créer. Un bris de
cette nature dans les modèles à haute tension
peut provoquer des surtensions de plus de trois
fois la tension phase-terre normale dans un
système qui ne se trouve pas solidement mis à la
terre.
8. Surtension atmosphérique. La foudre peut
provoquer une surtension par un contact direct ou
par induction d’un coup de foudre à proximité. Ces
ondes de tension se propagent le long du circuit
avec les magnitudes de pointe du courant de la
foudre et les temps d’échauffement qui dépendent
de l’impédance de surtension du système.
9. Circuits à fréquence variable. Selon la particularité
du concept, il est possible de produire des pointes
de tension durant les démarrages/arrêts ou même
pendant la commutation de chaque demi-cycle.
L’annexe II indique la forme d’onde recommandée
pour de telles utilisations.
On estime que l’ampleur de ces diverses surtensions
varie normalement de deux à cinq fois la tension de pointe
phase à phase normale avec des temps d’échauffement de
0,1 à 1 microseconde. Les défaillances de bobinage
causées par ces transitoires se manifestent normalement
sous forme de défauts spire à spire ou spire à mise à la
terre. On confond souvent cette cause de bris avec un autre
mode de défaillance.
Le fabricant ne dispose généralement pas de
renseignements suffisants sur l’utilisation future du moteur
pour déterminer l’ajout d’une protection contre la surtension
et la foudre. Par contre, il est en mesure d’évaluer les
limites de surtension que le moteur peut supporter pour
offrir une longévité satisfaisante.