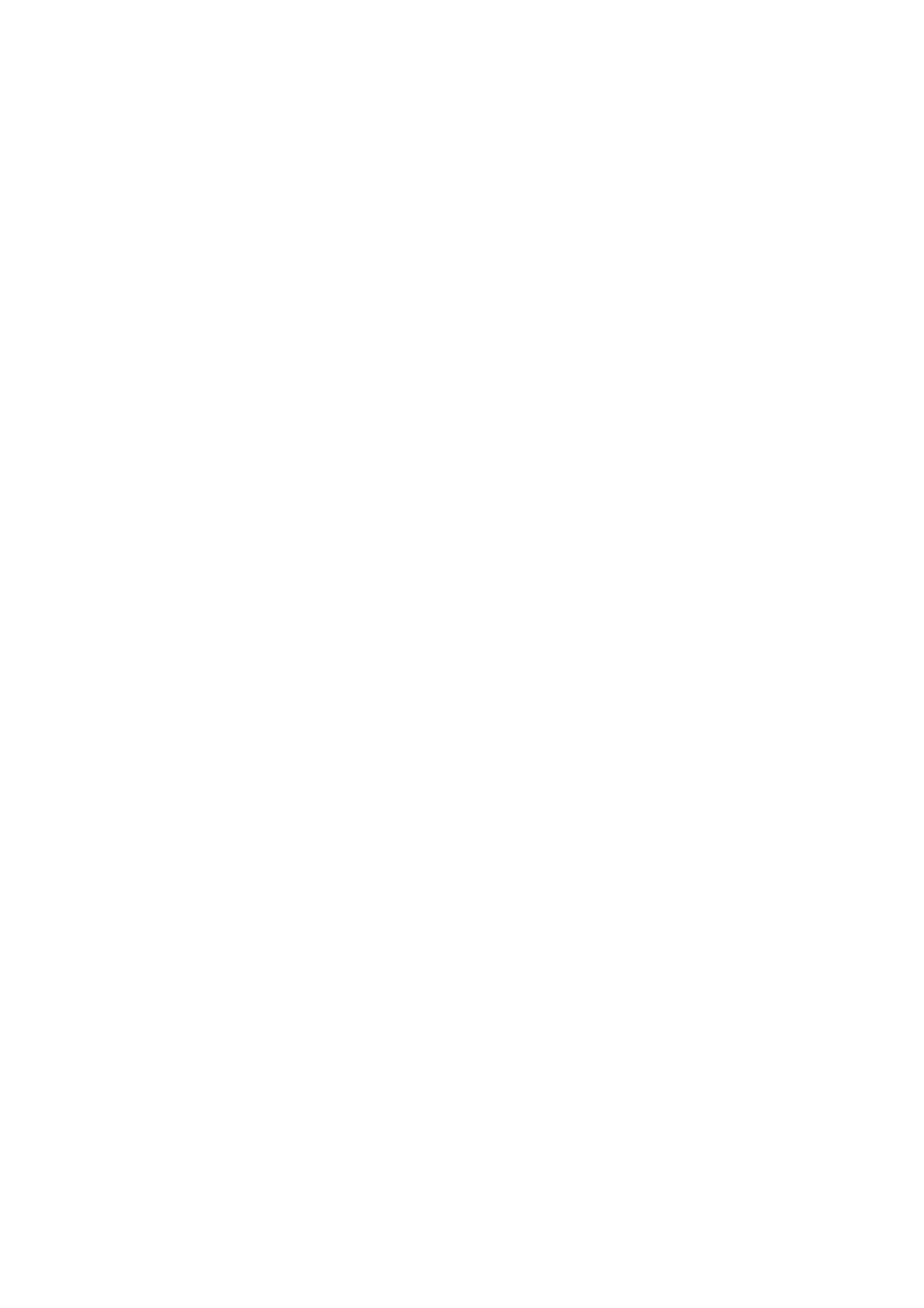
3
L’oxyde d’iridium ........................................................................................................................... 51
b. Les matériaux bimétalliques : effet de la teneur en iridium ....................................54
Composition catalytique Ru0,7Ir0,3O2 ...................................................................................... 54
Composition catalytique Ru0,8Ir0,2O2 ...................................................................................... 56
Composition catalytique Ru0,9Ir0,1O2 ...................................................................................... 57
c. L’effet de l’ajout d’un troisième métal : co-calcination des trois métaux. ................58
Etude des matériaux trimétalliques Ru0,85Ir0,10Sn0,05O2 et Ru0,85Ir0,05Ti0,10O2 ........ 58
d. Ajout du troisième métal utilisé comme support ....................................................60
Les matériaux trimétalliques Ru0,85Ir0,05Ta0,10O2 et Ru0,85Ir0,05Nb0,10O2 ................... 60
4. Caractérisation par diffraction des rayons X ..................................................................63
a. Etude de la taille des cristallites ............................................................................67
b. Etude du paramètre de maille ...............................................................................68
Les catalyseurs monométalliques ............................................................................................ 68
L’étude du paramètre de maille des matériaux bimétalliques ..................................... 69
5. Mesure de la surface spécifique par la méthode Brunauer-Emmett-Teller .....................70
La méthode de synthèse polyol ............................................................................................71
Caractérisation par microscopie électronique en transmission .............................................71
a. Les catalyseurs monométalliques et bimétalliques : l’oxyde de ruthénium et le
matériau bimétallique Ru0,90Ir0,10O2 ................................................................................71
Caractérisation par diffraction des rayons X .........................................................................73
Effet de la méthode de synthèse ..........................................................................................74