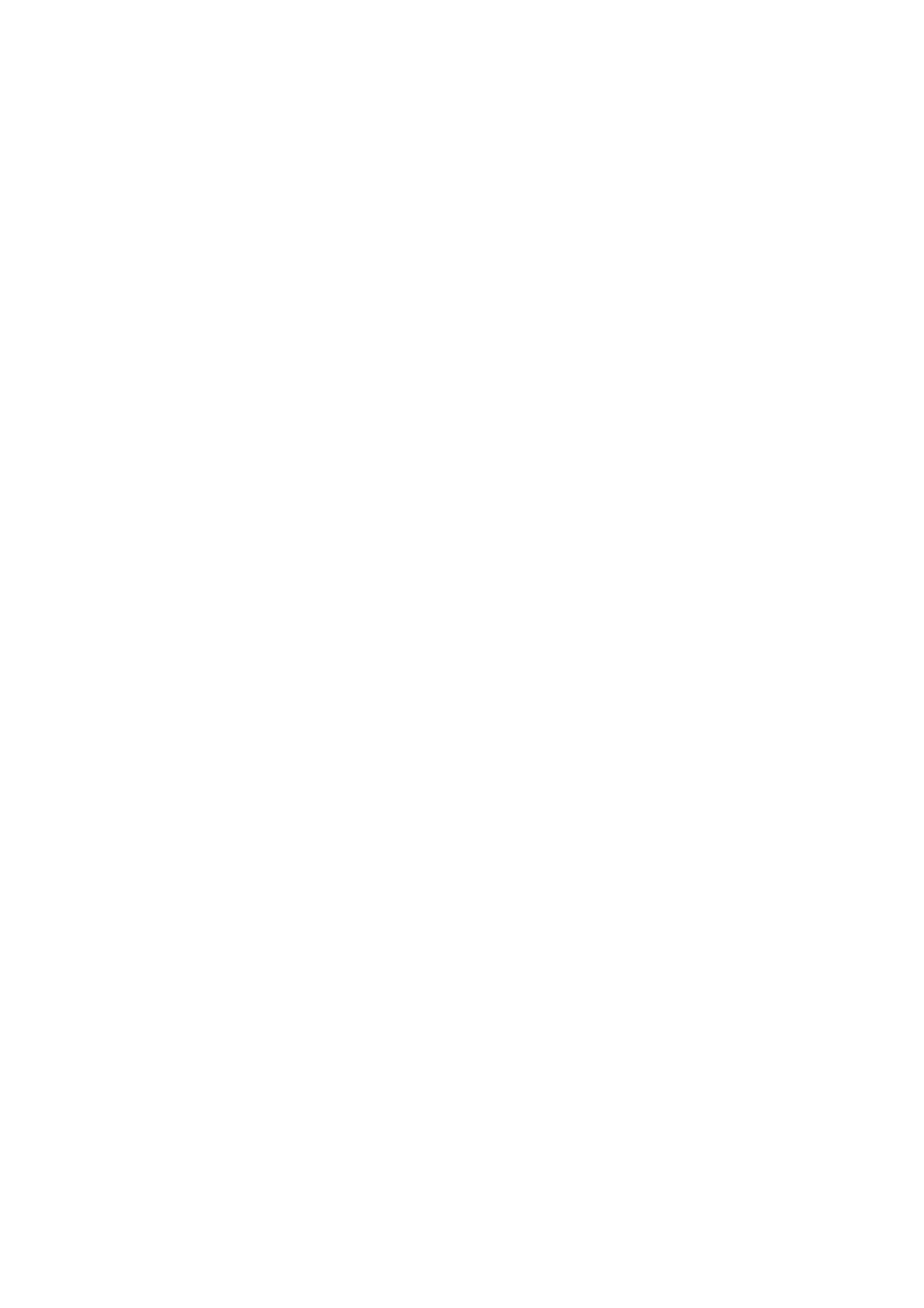
5
Avant Propos
Cette étude a été effectuée au Laboratoire de Mécanique des Solides de l’Université de
Poitiers (UMR 6610) dont je remercie son directeur, Monsieur le Professeur O. Bonneau,
pour m’avoir accepté pour ces travaux de doctorat.
Je tiens bien évidemment à remercier particulièrement mon directeur de thèse Monsieur le
Professeur Arghir M. pour sa confiance et ses conseils qui m’ont permis de réaliser ce travail
de thèse.
Je remercie sincèrement Monsieur Thouverez F., Professeur de l’Ecole Centrale de Lyon et
Monsieur Nelias D., Professeur à l’INSA de Lyon pour avoir accepté d’être les rapporteurs de
mes travaux auprès de l’université de Poitiers.
Je suis aussi très reconnaissant envers Monsieur Bonnet P., Directeur de recherche au
Laboratoire d’Etude Aérodynamique, pour sa disponibilité lui permettant d’apporter son
expertise dans le domaine de la Mécanique des Fluides.
Ce projet de recherche s’appuie sur un partenariat industriel établi lors du précédent contrat de
thèse et qui a été reconduit dans le but d’élargir la validité du modèle numérique. Un suivi
régulier de l’avancement des travaux, rythmé par des réunions semestrielles, a été mis en
place. Je tiens ainsi à remercier nos partenaires industriels représentés principalement par les
ingénieures Magret C., Quenardel A. et Gastineau O. pour leur accueil toujours très cordial et
avec qui les échanges durant nos réunions semestrielles ont souvent été très constructifs.
Avant de terminer, je souhaiterais remercier amicalement l’ensemble des membres du
laboratoire : les chercheurs, les secrétaires, les techniciens, mais plus particulièrement les
doctorants de la salle informatique (Fabien, Touf, Mihai Bogdan Dobrica, Hung, Dédé, Seb)
avec qui l’entraide a été souvent très utile. Je remercie très sincèrement les informaticiens,
Franck et Mathieu, dont les conseils m’ont été très souvent bénéfiques.
Pour terminer d’une manière plus personnelle, je voudrais remercier très chaleureusement ma
famille et plus particulièrement mon épouse qui m’a soutenu tout au long de mon travail.