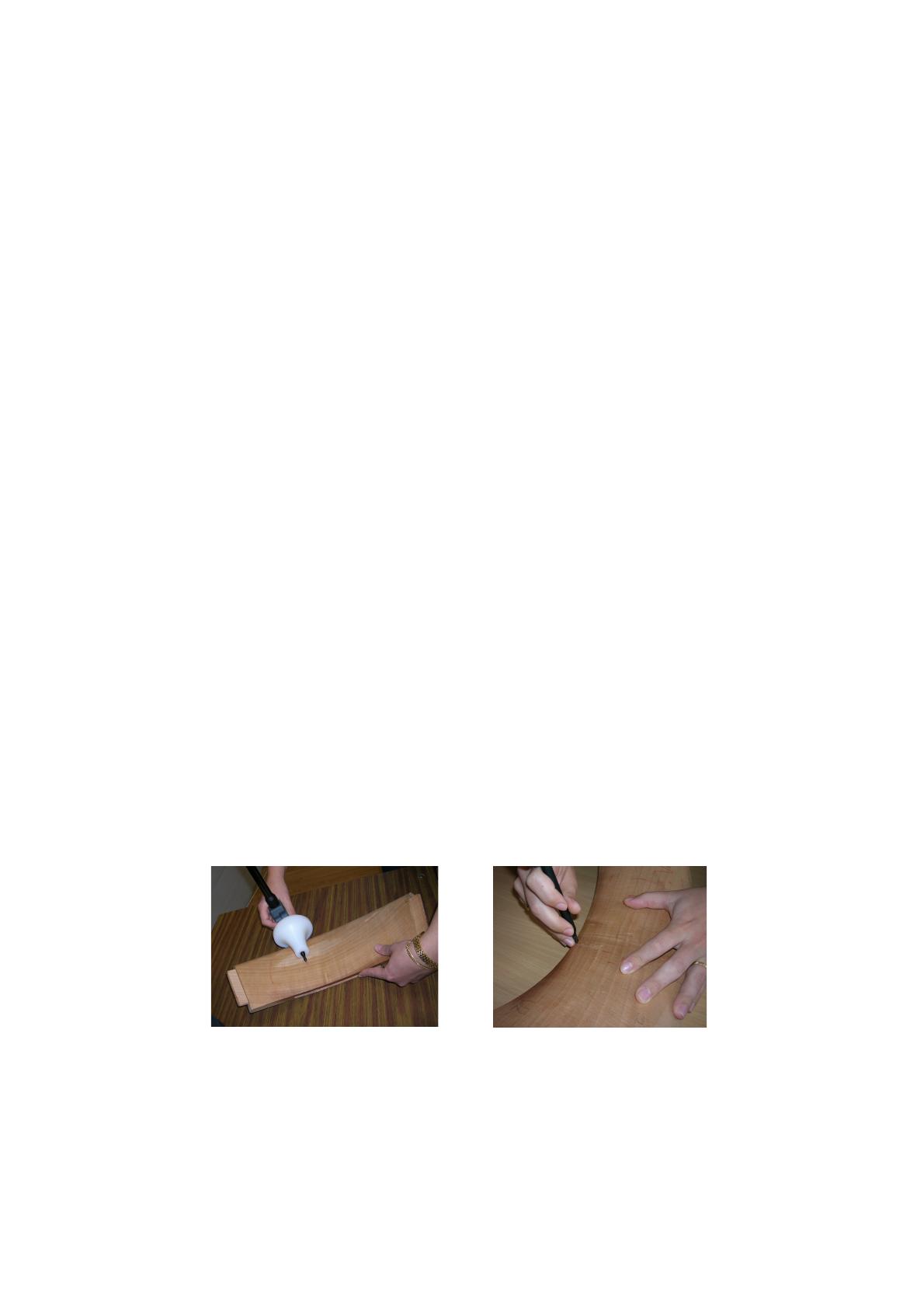
l’outil (Cf. fig. 1). Cette trajectoire nous permet de calculer la surface réellement
obtenue et de détecter des écarts.
Le prototype est défini à partir de formes gauches que l’on peut obtenir soit par de
l’usinage en bout soit par un usinage en roulant. Etant donné les faibles pressions
spécifiques de coupe dans l’usinage de pièces en bois, les usineurs programment en
roulant afin d’enlever un maximum de matière en une seule opération qui a un rôle
d’ébauche et de semi-finition. L’opération de finition est ensuite toujours réalisée par
polissage. Le choix de l’usinage en bout dans certaines pièces est nécessaire à cause de
la visibilité ou des risques d’interférences globales.
Nous nous intéressons ici uniquement à l’usinage en roulant. Nous supposons que
cinématiquement toutes les surfaces sont accessibles et sans risque d’interférences
globales (le porte-outil ne peut pas être en collision avec un élément).
L’usinage en roulant de surfaces gauches a été traité par de nombreux chercheurs
mais spécifiquement sur les surfaces réglées. (Liu 1995) cherche 2 points de l'axe de
l'outil à ¼ et ¾ de la règle. Dans (Redonnet et al., 1998), le positionnement de l'outil est
calculé à partir de 2 points de tangence sur les directrices tout en conservant un point de
contact sur la règle concernée. Dans (Monies et al., 2002), cette méthode est étendue
aux outils coniques. Dans (Bedi et al., 2003), le positionnement de l'outil est calculé
dans les 2 plans osculateurs aux extrémités de la règle. (Menzel et al., 2004) reprennent
cette méthode et minimisent sur quelques points, l'écart entre l'outil et la surface. Ces
différentes approches cherchent à améliorer les trajectoires afin de se rapprocher de la
surface nominale définie par la CAO. Elles portent toujours sur des géométries d’outils
élémentaires (cylindriques et coniques) contrairement à notre étude qui privilégie la
complexité des géométries et l'allure générale de ces pièces en bois sur la précision.
1.1. Définition de l'outil
Dans les pièces à usiner, nous devons limiter le nombre d’opérations et donc choisir
des outils qui permettront d’obtenir rapidement la pièce. Le choix de la géométrie
d’outil se fera à l’aide d’une section caractéristique de la pièce (Cf. fig. 2) et celui des
opérations, en fonction des différents posages de pièce dans l’espace de la machine.
Figure1. Palpage d'un dossier de chaise Figure 2. Récupération du profil de l'outil
2