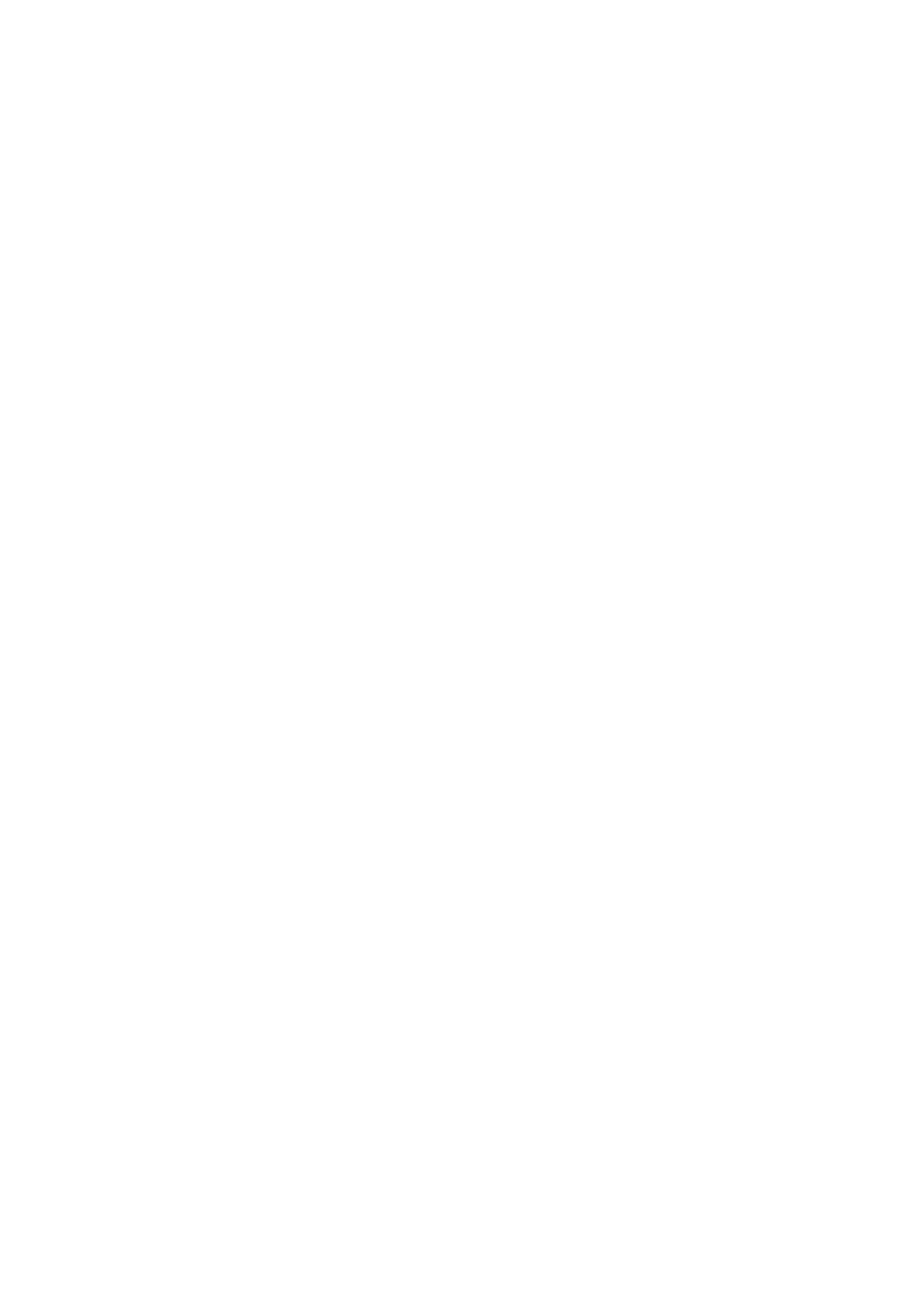
Remerciements
Ce travail a été effectué au sein du l’Institut de Chimie et des Milieux et Matériaux de
l’Université de Poitiers (IC2MP, UMR 7285), sous la direction de Madame Catherine
ESPECEL et Madame Laurence VIVIER. Cette étude n’aurait pu être réalisée sans l’appui
financier de la région Poitou-Charentes.
J’exprime toute ma reconnaissance et ma gratitude à Monsieur Jacques BARBIER Jr.,
Madame Florence EPRON et Madame Laurence PIRAULT-ROY directeurs de l’équipe
Catalyse par les métaux pour m’avoir accueillie dans leur laboratoire et pour leur sympathie
continuelle.
Je remercie Monsieur Jacques BARBIER Jr., Professeur de l’Université de Poitiers, pour
l’honneur qu’il me fait de présider ce jury de thèse.
J’adresse mes sincères remerciements à Monsieur Pascal GRANGER, Professeur de
l’Université de Lille, et à Madame Catherine PINEL, Directrice de recherche CNRS à l’Institut
de Recherches sur la Catalyse et l’Environnement de Lyon, d’avoir bien voulu accepter de
juger ce travail et d’en être les rapporteurs auprès de l’Université de Poitiers.
Ainsi que Madame Laetitia OLIVIERO, Maître de conférences de l’Université de Caen
pour sa participation à ce jury.
J’exprime ma profonde et sincère reconnaissance à Mesdames Catherine ESPECEL et
Laurence VIVIER, Maîtres de conférences à l’Université de Poitiers pour leur encadrement,
pour leur aide précieuse et la rigueur scientifique qu’elles m’ont apportés dans la réalisation de
cette thèse.
Je remercie particulièrement Michel CHAUVEAU et Mehrad TARIGHI, qui m’ont
donné de nombreux conseils et apporté leur aide technique sur les montages, le tout dans une
ambiance toujours des plus agréables.
Je tiens à remercier également tous ceux, permanents comme étudiants, qui ont contribué
à ce que cette thèse se passe dans les meilleures conditions possibles.