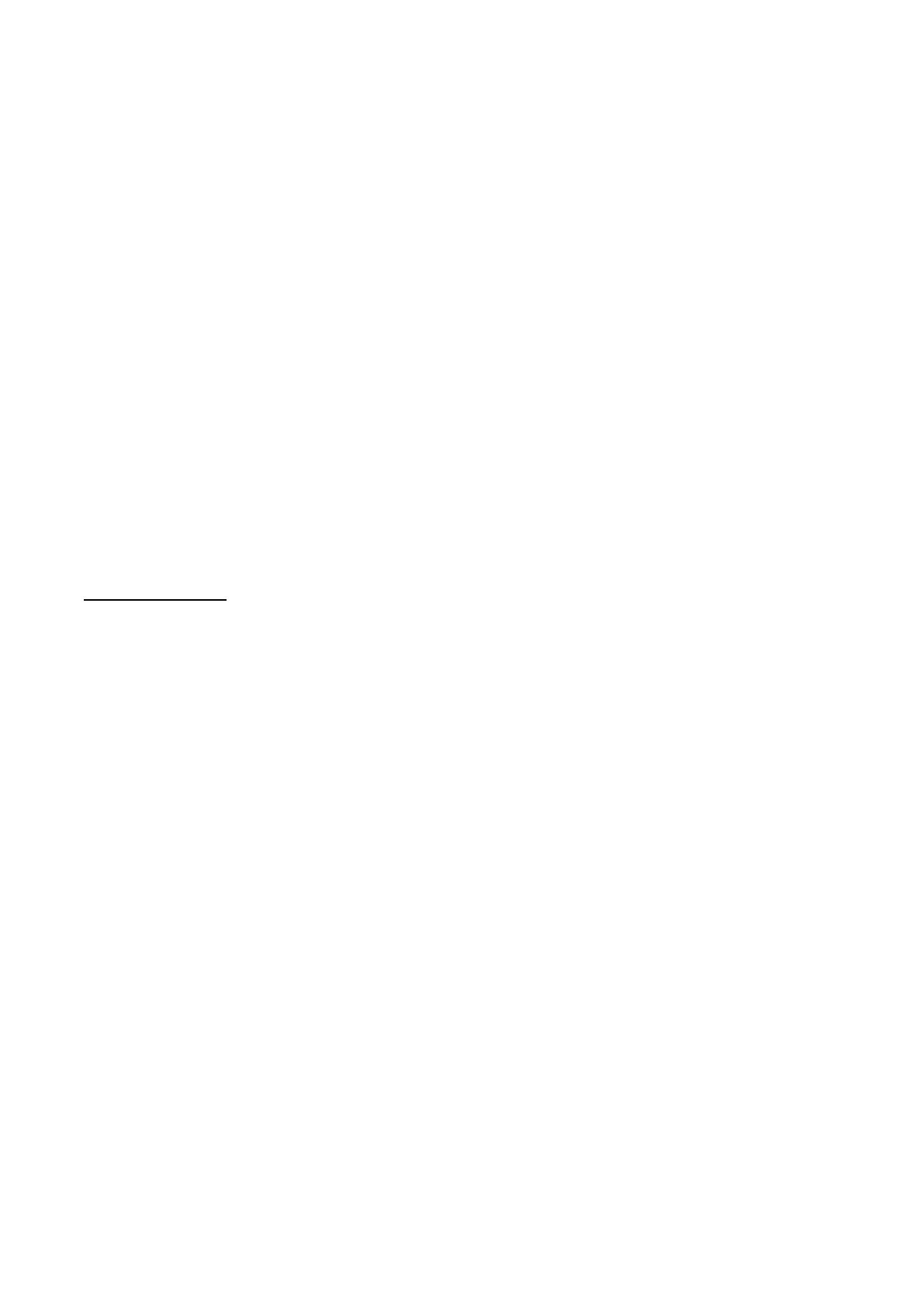
2.4 – Le TQM
TQM = total quality management ou CWQC – company wide quality control.
Introduit dans les années 80.
Vise l’obtention de la qualité par la mobilisation de tous.
La recherche de la qualité y est un processus intégrateur (tous y participent, du management à l’ouvrier) et
transversal (toutes les fonctions sont concernées).
Le « service qualité » ou la préoccupation qualité axée sur la production évolue vers une culture de la
qualité totale.
Dont l’objectif est la création de valeur et la satisfaction du client.
Basée sur des processus d’amélioration de la qualité.
Les méthodes et outils y sont des aides à une stratégie qualité globale s’appuyant sur les ressources
humaines.
Le TQM intègre :
- la mise en cohérence de la politique qualité avec la stratégie générale ;
- la diffusion de cette politique dans toutes les directions ;
- les risques (financiers, sociaux, concurrentiels, …) ;
- la relation client fournisseur interne ;
- la motivation du personnel ;
- l'analyse des besoins clients et le positionnement marketing ;
- la maîtrise des processus internes et leur amélioration (voir § 4.2) ;
- une recherche d’amélioration de la rentabilité.
3 – La maintenance
Maintenance = « ensemble des actions permettant de maintenir ou de rétablir un bien dans un état spécifié
ou en mesure d’assurer un service déterminé, au coût optimal » (AFNOR X-60-010).
Concerne l’outil de production, les systèmes de soutien, les bâtiments, …
Concerne les produits (garantie et service après-vente : réparations, rechanges, …).
La maintenance influe sur la qualité, elle comprend trois volets :
- maintenance curative (intervention pour remédier à une panne) ;
- maintenance préventive (entretien permettant de réduire la probabilité de panne) ;
- maintenance évolutive (mise à niveau des équipements.
La facilité de maintenance des produits est un facteur de qualité du processus de production qui influence
aussi la qualité perçue par le client.
Elle est intégrée dans la conception du produit.
Elle exploite, quand cela est possible, des alertes automatiques.
Elle constitue un argument de vente (possibilités d’évolution, image d’après-vente fiable, …).
La maintenance préventive de l’outil de production permet :
- de réduire les temps morts par la planification des interventions (moins de pannes, maintenance hors temps
de production) ;
- de réduire les coûts (meilleure organisation, négociation des approvisionnements qui sont alors prévisibles,
moins de défauts de production et de rebuts, prolongation de la durée de vie des équipements) ;
- de respecter les normes de production et de sécurité.
L’organisation de la maintenance peut être centralisée, répartie entre différents centres géographiques, sous-
traitée, confiée aux revendeurs agréés, …
La maintenance de premier niveau consiste à détecter l’origine de la panne, à intervenir sur des problèmes
simples ou à transférer vers un centre spécialisé dans les autres cas.
Dans les SI, la télémaintenance se développe avec les réseaux (prise de contrôle d’une machine à distance
pour un diagnostic ou la réparation d’une panne logicielle).