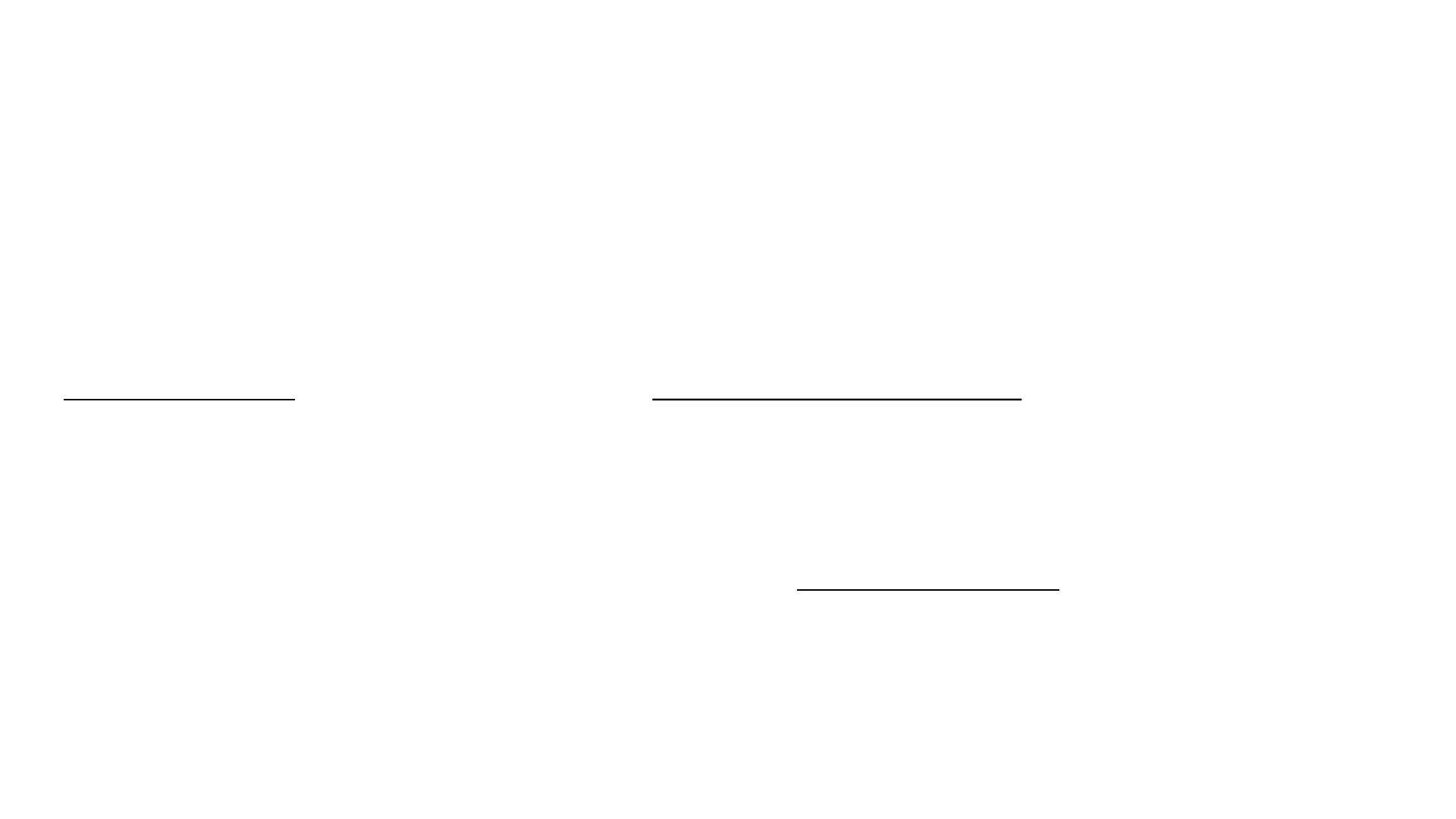
Polymérisation par complexes de métaux de transition
Introduction
*Au cours des réactions de polymérisation, l'enchaînement des motifs monomères s'effectue généralement
d'une manière assez désordonnée suivant plusieurs conformations possibles.
*Avec les monomères vinyliques, les substituants latéraux sur la chaîne macromoléculaire peuvent se
disposer au hasard de part et d'autre de celle-ci: DISPOSITION ATACTIQUE.
*Avec les composés diéniques tels que le butadiène CH2=CH—CH=CH2 ou l'isoprène CH2=C(CH3)-CH=CH2,
la polymérisation laisse dans la chaîne une double liaison par motif monomère donnant des possibilités
locales de conformation "Z" (Cis) ou "E" (Trans) également distribuées au hasard.
*Les amorceurs cationiques et anioniques ne polymérisent pas en général les monomères α-oléfines
CH2=CH(R), ou ne donnent que des oligomères avec des rendements faibles et des structures angulaires
(Transposition du C+ dans le cas de la polymérisation cationique).