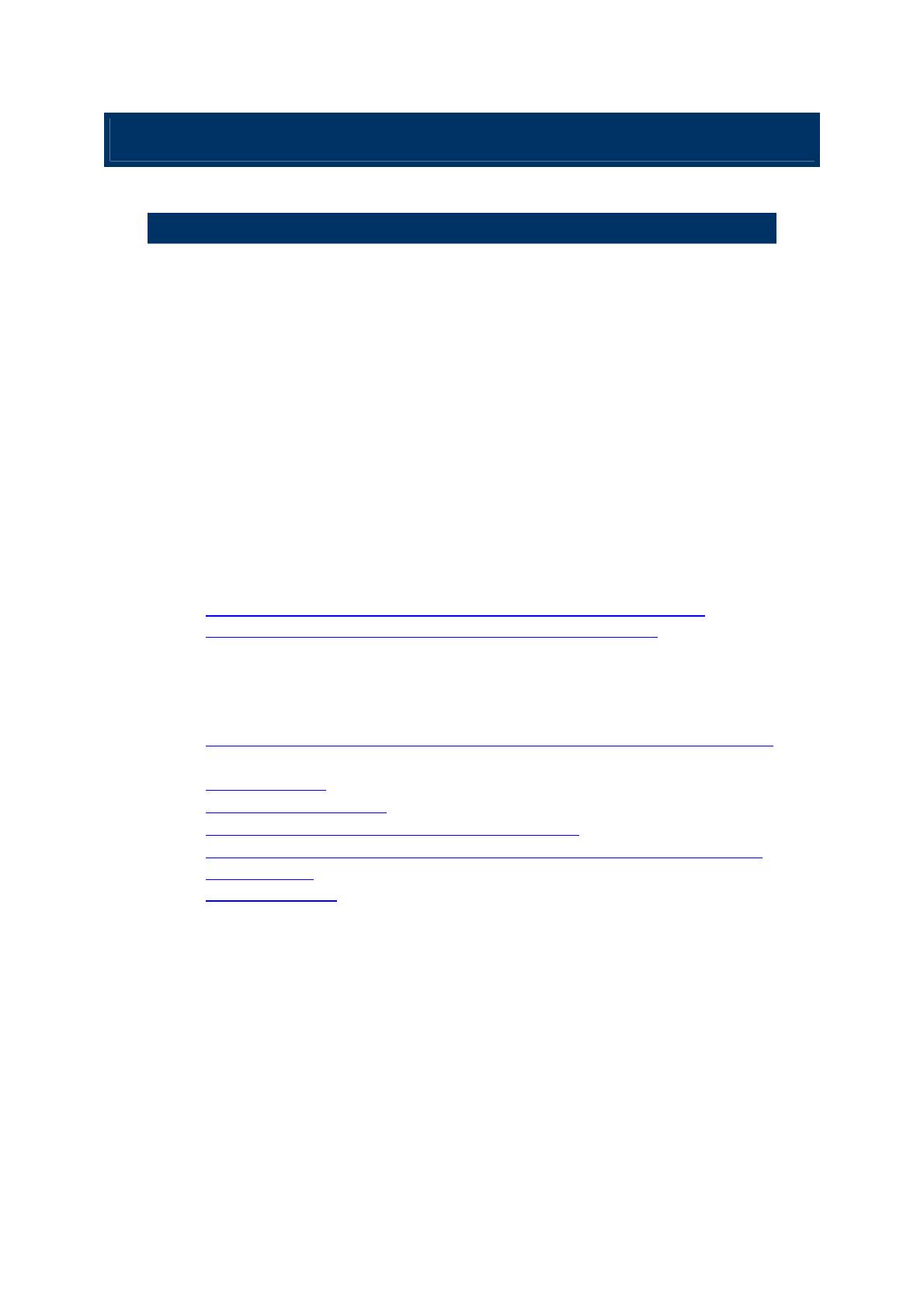
Comment accroître et renouveler les réserves de pétrole et de gaz ? - Avancées de la
technologie et stratégie de recherche de l'IFP
Conférence de presse
Date : 31/05/2005
Lieu : Paris
Les progrès de la technologie pour accéder à de nouvelles ressources (pétroles
lourds, gisements enfouis, offshore ultra-profond), mieux exploiter les réserves
disponibles (augmentation du taux de récupération) et réduire les coûts vont
permettre de repousser les limites des réserves d'hydrocarbures et de prolonger
durablement l'approvisionnement mondial.
Dans un contexte où les incertitudes géopolitiques, les cours très élevés du brut et
les déclarations alarmistes d'experts dits "pessimistes" font resurgir les inquiétudes
relatives aux réserves de pétrole, l'IFP fait un point sur le rôle essentiel que peut
jouer la technologie.
• Comment accroître et renouveler les réserves de pétrole et de gaz ?
Avancées de la technologie et stratégie de recherche de l'IFP (PDF - 4.3
Mo)
par Olivier Appert, Président
J. Lecourtier, Directeur scientifique
G. Friès, Directeur du Centre de Résultats Exploration-Production
• Comment augmenter le taux de récupération du pétrole dans les gisements ?
(PDF - 60 Ko)
• Les bruts lourds (PDF - 60 Ko)
• L'offshore ultra-profond (PDF - 60 Ko)
• Les gisements très enfouis au delà de 5000 mètres (PDF - 50 Ko)
• Réserves de pétrole : des données évolutives en fonction de la technique et
de l'économie.
Le point par l'IFP (PDF - 60 Ko)