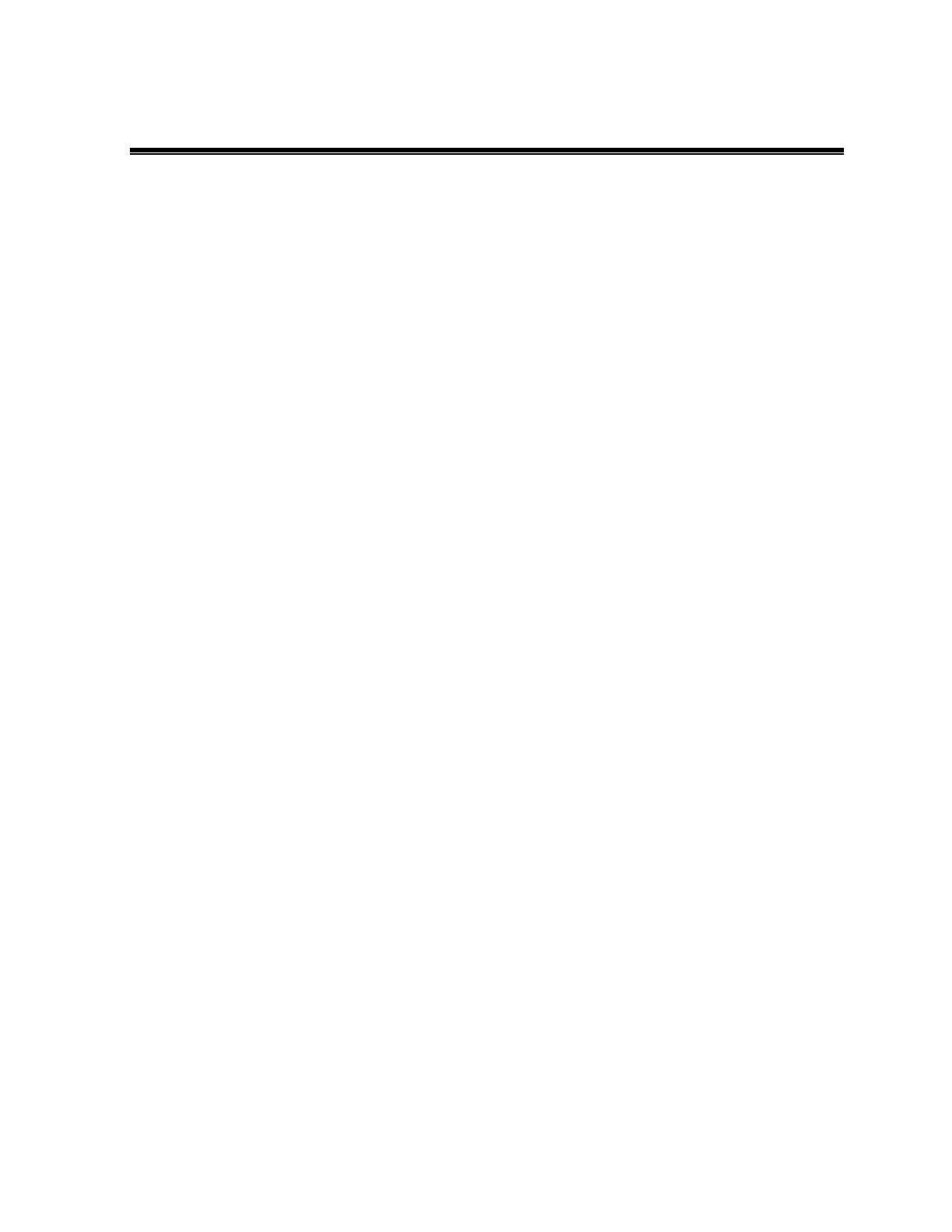
i
RÉSUMÉ
L’industrie des biocarburants de deuxième génération utilise, entre autre, la biomasse
lignocellulosique issue de résidus forestiers et agricoles et celle issue de cultures énergétiques.
Le sorgho sucré [Sorghum bicolor (L.) Moench] fait partie de ces cultures énergétiques.
L’intérêt croissant de l’industrie agroalimentaire et des biocarburants pour cette plante est dû à
sa haute teneur en sucres (jusqu’à 60% en masse sèche). En plus de se développer rapidement
(en 5-6 mois), le sorgho sucré a l’avantage de pouvoir croître sur des sols pauvres en nutriments
et dans des conditions de faibles apports en eau, ce qui en fait une matière première intéressante
pour l’industrie, notamment pour la production de bioéthanol.
Le concept de bioraffinerie alliant la production de biocarburants à celle de bioénergies ou de
bioproduits est de plus en plus étudié afin de valoriser la production des biocarburants. Dans le
contexte d’une bioraffinerie exploitant la biomasse lignocellulosique, il est nécessaire de
s’intéresser aux différents métabolites extractibles en plus des macromolécules permettant la
fabrication de biocarburants et de biocommodités. Ceux-ci pouvant avoir une haute valeur
ajoutée et intéresser l’industrie pharmaceutique ou cosmétique par exemple. Les techniques
classiques pour extraire ces métabolites sont notamment l’extraction au Soxhlet et par
macération ou percolation, qui sont longues et coûteuses en énergie. Ce projet s’intéresse donc
à une méthode d’extraction des métabolites primaires et secondaires du sorgho sucré, moins
coûteuse et plus courte, permettant de valoriser économiquement l’exploitation industrielle du
de cette culture énergétique. Ce travail au sein de la CRIEC-B a porté spécifiquement sur
l’utilisation d’une émulsion ultrasonique eau/carbonate de diméthyle permettant de diminuer les
temps d’opération (passant à moins d’une heure au lieu de plusieurs heures) et les quantités de
solvants mis en jeu dans le procédé d’extraction. Cette émulsion extractive permet ainsi de
solubiliser à la fois les métabolites hydrophiles et ceux hydrophobes. De plus, l’impact
environnemental est limité par l’utilisation de solvants respectueux de l’environnement (80 %
d’eau et 20 % de carbonate de diméthyle). L’utilisation de deux systèmes d’extraction a été
étudiée. L’un consiste en la recirculation de l’émulsion, en continu, au travers du lit de biomasse;
le deuxième permet la mise en contact de la biomasse et des solvants avec la sonde à ultrasons,
créant l’émulsion et favorisant la sonolyse de la biomasse.
Ainsi, en réacteur « batch » avec recirculation de l’émulsion eau/DMC, à 370 mL.min-1, au sein
du lit de biomasse, l’extraction est de 37,91 % en 5 minutes, ce qui est supérieur à la méthode
ASTM D1105-96 (34,01 % en 11h). De plus, en réacteur « batch – piston », où la biomasse est
en contact direct avec les ultrasons et l’émulsion eau/DMC, les meilleurs rendements sont de
35,39 % en 17,5 minutes, avec 15 psig de pression et 70 % d’amplitude des ultrasons.
Des tests effectués sur des particules de sorgho grossières ont donné des résultats similaires avec
30,23 % d’extraits en réacteur « batch » avec recirculation de l’émulsion (5 min, 370 mL.min-
1) et 34,66 % avec le réacteur « batch-piston » (30 psig, 30 minutes, 95 % d’amplitude).
Mots-clés : Carbonate de diméthyle, Émulsion, Éthanol cellulosique, Extraction, Sorgho
sucré, Ultrasons.