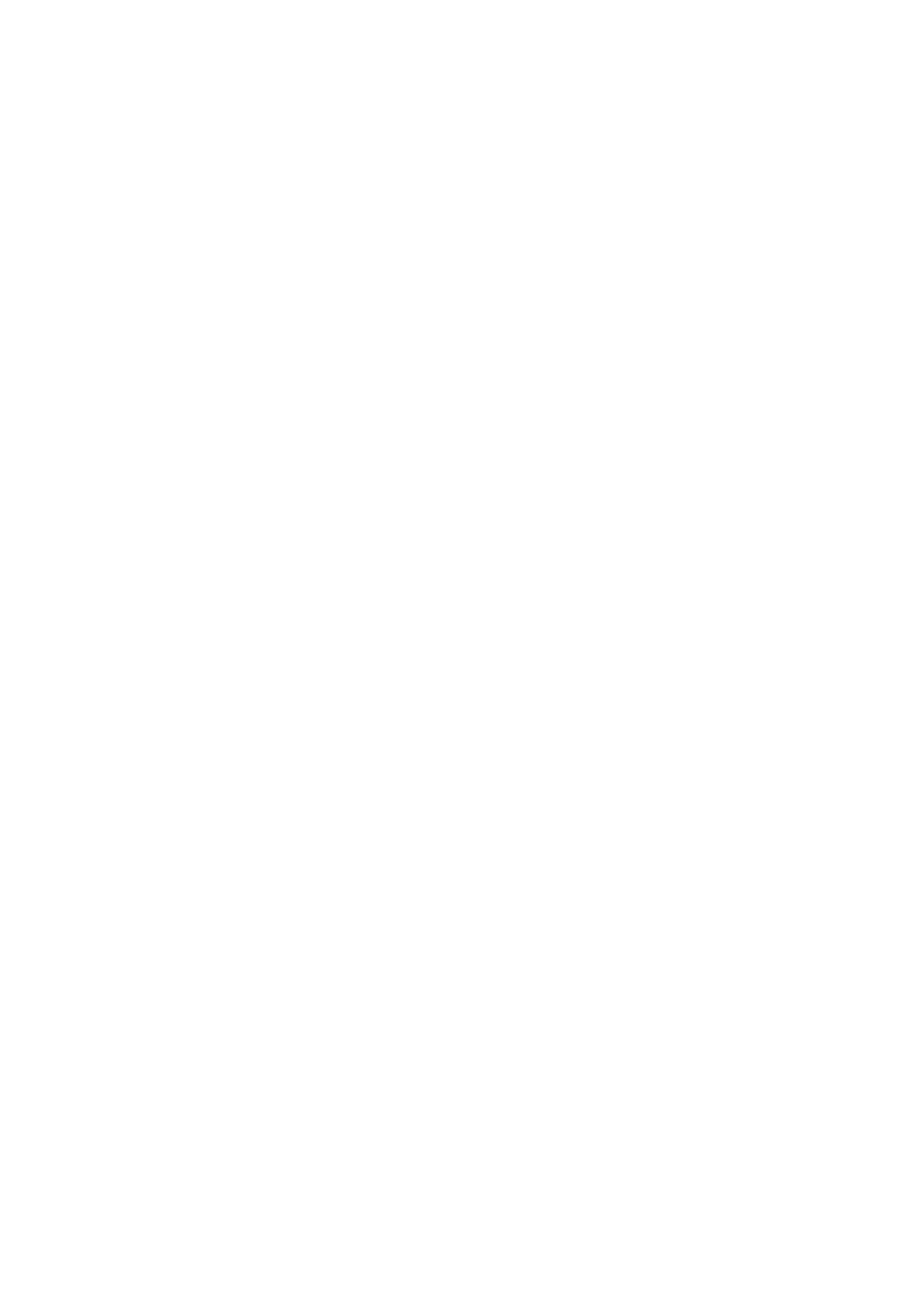
Remerciements
Je souhaite, en premier lieu, remercier James ROUDET directeur du laboratoire G2Elab pou m’avoir
accueilli dans ses locaux ainsi que l’entreprise VALEO pour m’avoir donné sa confiance afin de
réaliser cette thèse. Je souhaiterais également remercier l’Agence Nationale Recherche Technologie
pour l’appui financier qu’elle a accordé à ce projet.
Je voudrais ensuite remercier tous les membres du jury pour l’intérêt qu’ils ont montré à cette thèse. Je
tiens à remercier Souad HARMAND pour avoir accepté de présider ce jury. Merci également à
Georges BARAKAT et Frédéric GILLON, rapporteurs de cette thèse, pour leur examen profond et
pertinent de mon travail. Leurs rapports m’ont grandement inspiré et m’ont permis d’aller plus loin
dans la réflexion autour de ce travail.
J’exprime toute ma gratitude envers mon encadrement chez VALEO. Merci à Sophie PERSONNAZ,
Philippe FARAH, Jean-Claude MIPO et Olivier SAVINOIS pour leur soutien et les conseils qu’ils
m’ont donnés lors de nos réunions fréquentes et lors de mes visites à Créteil pour les séminaires et les
diverses formations que j’ai pu suivre. Je souhaite également remercier les ingénieurs et le personnel
de VALEO que j’ai rencontré pour leur aide technique mais aussi pour leur bienveillance quand ils
m’ont accueilli : Clément SAINT-PIERRE pour la conception des plans mécaniques sous CATIA,.
Michel FAKES pour son aide sur FLUENT sans oublier Meriem AHMED, Bassel ASLAN, Rija
ANDRIAMALALA, Jean-Marc DUBUS, Radu FRATILA, Radhouane KHLISSA, Jérôme
LEGRANGER, Antoine TAN-KIM. Je suis très content de continuer avec Valeo pour la suite et je
remercie Mouheb DHIFLI pour l’intérêt porté à mes travaux et à ma candidature. Je souhaite
également bonne chance et bon courage aux doctorants de la Chaire DEMETER Adolfo, Amit,
Pranshu et Ziwei.
Mes remerciements les plus sincères vont à mon encadrement de thèse au Laboratoire. Un énorme
merci à Afef LEBOUC pour son soutien de tous les instants, sa bienveillance et ses conseils
techniques et scientifiques, en particulier sur les matériaux magnétiques pour les machines. J’ai la plus
grande estime pour toi, pour ton professionnalisme, ta force de volonté et ton humanité. Toute ma
gratitude va aussi à Lauric GARBUIO. J’ai beaucoup appris auprès de Lauric tant scientifiquement
que humainement. Merci à toi pour ton ouverture d’esprit, ta grande culture technique et scientifique.
Tu m’as ouvert les yeux sur de nombreux points sur lesquels je pensais avoir des certitudes. Enfin, je
remercie infiniment Laurent GERBAUD pour son soutien et ses encouragements pour me lancer dans
la thèse depuis l’école d’ingénieur. J’ai beaucoup apprécié nos conversations à la fois scientifiques et
« personnelles ». Sans toi Laurent je ne serai pas arrivé là aujourd’hui.
Je souhaiterais également remercier Daniel GOMEZ et Yoann QUEREL, les deux stagiaires de PFE
qui m’ont accompagné sur les projets autour de la machine à commutation de flux et le
refroidissement diphasique. Bon courage Yoann pour ta poursuite en thèse avec Valeo ! Merci
également à François BLACHE, Claude BRUN et Sébastien FLURY pour leur aide précieuse sur la
partie technique et expérimentations.
Je remercie également les chercheurs et enseignants-chercheurs du Laboratoire et en particulier Gérard
MEUNIER, Brahim RAMDANE, Gilles CAUFFET, Christian CHILLET, Leticia GIMENO MONGE,
Benoit DELINCHANT pour leurs conseils et le grand recul qu’ils ont sur l’expérience qu’est le
doctorat. Je remercie également les personnes de l’administration, du service technique et Sylvie
GARCIA pour le temps qu’ils m’ont accordé.