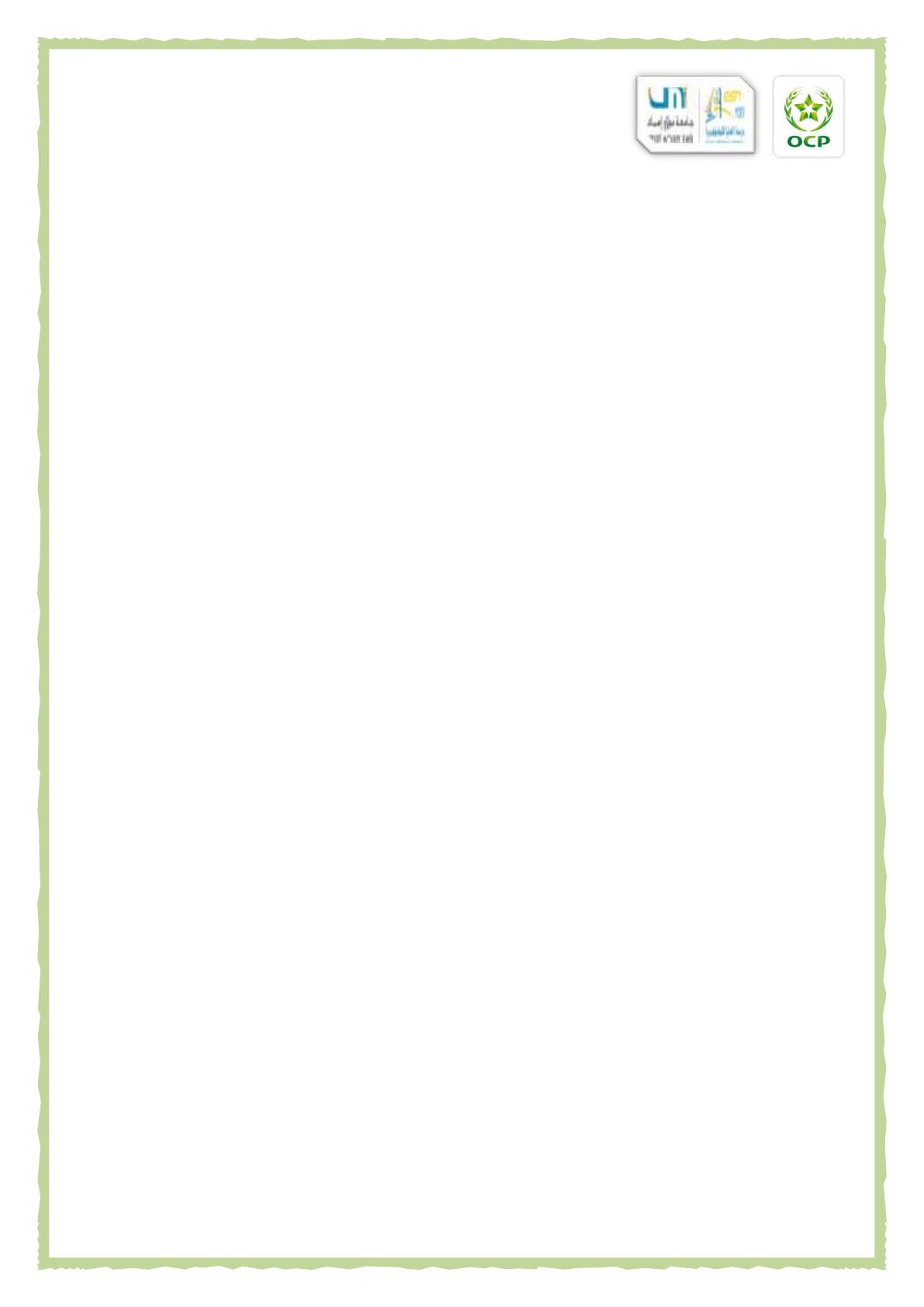
Rapport de stage Page 4
REMERCIEMENT :
Mes remerciements s'adressent à toutes les personnes
du service instrumentation de l’atelier CENTRALE
THERMIQUE à Maroc Phosphore 1, qui par leurs
dévouements, leurs savoir-faire et leurs extrêmes
gentillesses, ont su donner à mon stage un supplément
pratique qui a renforcé incontestablement ma formation
théorique.
De plus, l'accueil chaleureux qu'ils m'ont réservé,
l'amitié dont ils ont fait preuve à mon égard ; mais encore
leur disponibilité à tout besoin d'informations ont fait que
je garde un très beau souvenir de ce stage à la fois
agréable, enrichissant et instructif.
J’exprime toute ma reconnaissance au Responsable du
stage, Mr. KOLLACH pour l’opportunité que vous nous avez
donné pour effectuer ce stage, aussi à Mr. ALAMOUCH, et
Mr.MAHAMMID, pour l’aide et les précieux
renseignements qu’ils m’ont communiqués
Ma gratitude s'adresse enfin à ceux qui ont participé
de près ou de loin à la réalisation de ce présent travail.