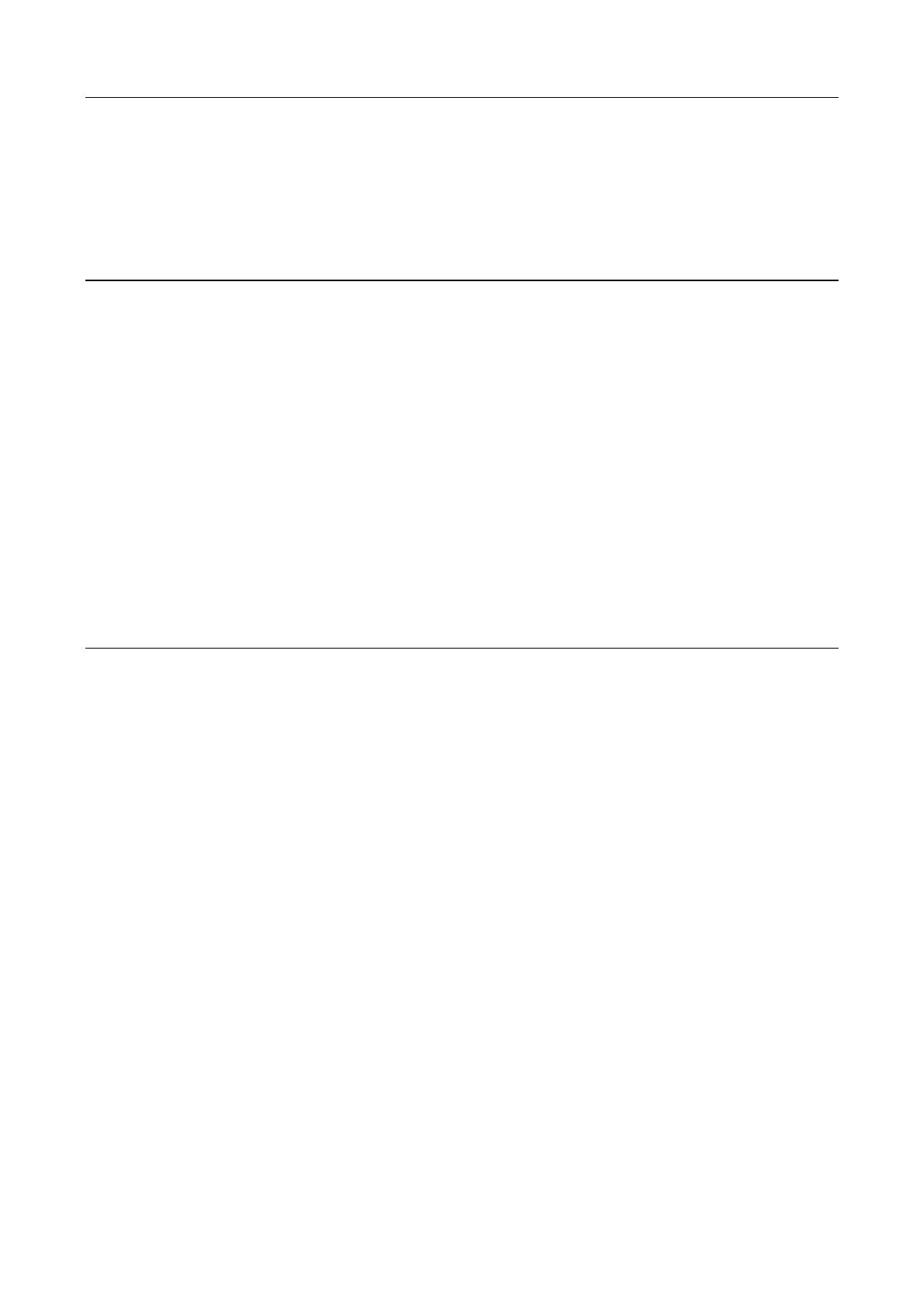
MATERIAUX 2006 13-17 Novembre 2006 – Dijon, France
Etude des performances des structures composites réparées
Julien Rodes, Romain Brossier, Xiao-Jing Gong, Jérôme Rousseau
Laboratoire de Recherche en Mécanique et Acoustique, ISAT Nevers, xiao-jing.gong@u-bourgogne.fr
RESUME :
L’étude s’inscrit dans le contexte de l’optimisation de la réparation des structures composites
carbone/époxyde. Une stratification quasi isotrope comportant 8 plis, vierge et endommagée par impact, est
caractérisée expérimentalement en traction statique et en fatigue. Les éprouvettes endommagées ont été
réparées selon différents protocoles utilisant le collage de patchs, afin de rétablir leurs performances à la fois
en statique et en fatigue, en tenant compte des aspects pratiques et économiques. On étudie l’influence de
différents paramètres, tels que la nature des patchs, leur séquence d’empilement et leur géométrie, sur les
performances des structures réparées. Les mécanismes de rupture des éprouvettes réparées sont étudiés à
l’aide de méthodes de contrôle non destructif telles que le contrôle par ultrasons (C-Scan) et la
thermographie infrarouge. Une modélisation numérique par éléments finis a permis de dégager certains
paramètres importants en vue d’optimiser la réparation. Les solutions retenues sont testées et comparées
afin de discuter la validité et les limites de ces méthodes de réparation.
MOTS-CLES
: composites stratifiés – réparation – fatigue – modélisation numérique
Introduction
Le développement de l’utilisation des matériaux composites pour la réalisation de structures pose le
problème de leur cycle de vie et notamment des endommagements accidentels auxquels ils peuvent être
soumis. Dans le cas des endommagements d’impacts basse vitesse, du type chute d’outil, on peut observer
une réduction des performances mécaniques des structures, notamment de leur résistance en fatigue.
Plutôt que de remplacer des structures qui peuvent être de grandes dimensions, il est plus
économique d’envisager de réparer ces dommages d’impact afin de redonner aux pièces composites leurs
propriétés originelles. Cependant, les techniques de réparation couramment utilisées, notamment dans le
domaine aéronautique, réclament un savoir faire important et sont souvent d’une mise en œuvre complexe.
Cette complexité représente un obstacle pour le développement de structures composites en grandes
séries.
Nous présentons ici un travail préliminaire visant à déterminer l’efficacité de protocoles de réparation
simplifiés, et notamment l’influence de la géométrie et de la stratification des patchs de réparation. Dans un
premier temps, l’étude de la rupture en traction statique et en fatigue des éprouvettes vierges est présentée.
L’endommagement est simulé ensuite par un perçage permettant de retirer totalement la zone impactée.
Ces éprouvettes trouées sont également caractérisées, puis on étudie expérimentalement les performances
de divers protocoles de réparation. Parallèlement, une étude numérique permet de dégager certains
paramètres géométriques et matériels influents, ainsi que de proposer et valider des solutions originales.