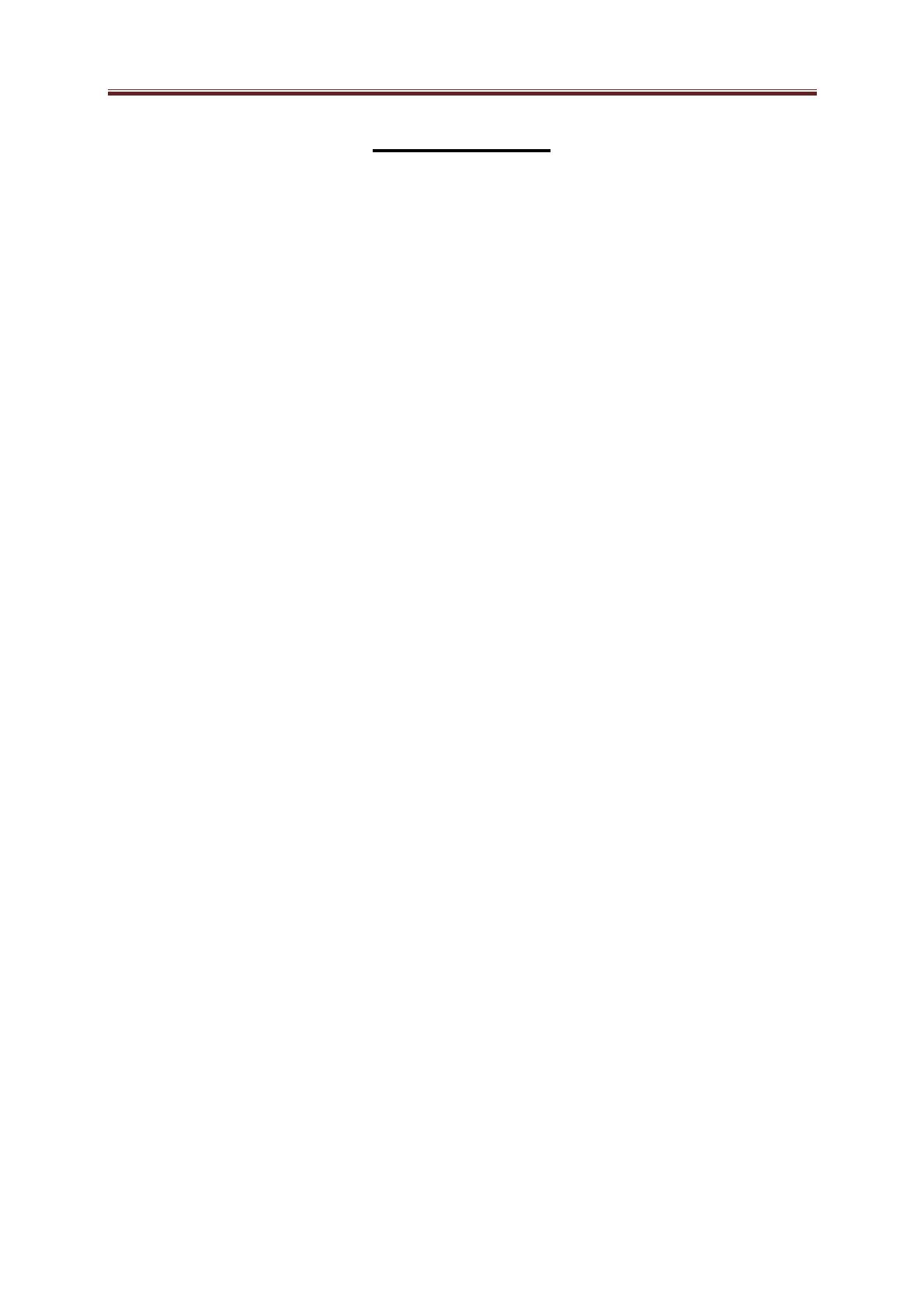
Avant propos
Avant propos
Les travaux présentés dans ce mémoire ont été réalisés au Laboratoire de Spectroscopie,
Modélisation Moléculaire, Matériaux et Environnement LS3ME, Equipe Physico-chimie des
Matériaux et Environnement EPCME, Université Mohammed V, Faculté des Sciences de
Rabat sous la direction du Professeur Souad EL HAJJAJI en codirection avec le Professeur
Mr. Bennaceur OUAKI responsable du Laboratoire de Génie des matériaux de l’Ecole
Nationale Supérieure des Mines de Rabat.
Je tiens à remercier sincèrement Madame Souad EL HAJJAJI, Professeur à la faculté des
Sciences de Rabat et Directrice de mes travaux de recherches pour toutes les connaissances
qu’elle m’a transmises dans le domaine des matériaux. Elle a été mon professeur et sans elle
ce travail n’aurait certainement pas eu lieu. Je la remercie aussi pour l’autonomie qu’elle m’a
accordée, tout en restant disponible, et pour ses qualités humaines et scientifiques qui ont
permis la réalisation de ce travail dans les meilleures conditions possibles.
J’exprime ma profonde gratitude au Professeur Mr. Bennaceur OUAKI, responsable du
Laboratoire de génie des matériaux de l’Ecole Nationale Supérieure des Mines de Rabat, et
codirecteur de mes travaux de recherches pour son aide précieuse au quotidien et sa forte
implication dans ce travail. Son aide s’est révélée précieuse et sans qui certains thèmes de la
thèse n’auraient pas pu être abordés aussi sereinement. Je lui exprime aussi toute ma gratitude
d’avoir accepté de présider le jury de ma thèse.
J’adresse un remerciement particulier à Mme Fouzia GUEDIRA, Professeur à la Faculté des
Sciences de Rabat, d’avoir accepté de faire partie du Jury et à qui j’adresse mes plus vifs
remerciements.
Je remercie vivement à Mr Mohammed BENMESSAOUD, Professeur Habilité de l’Ecole
supérieur de Technologie de Salé, pour tout l’intérêt qu’il a porté à mon travail en acceptant
de le juger.
Mes remerciements s’adressent également à Mr Moulay Abdrrahim EL MHAMMEDI,
Professeur Habilité à la Faculté Poly-disciplinaire de Khouribga. Je lui exprime aussi toute ma
gratitude d’avoir accepté d’examiner ce travail.
Leurs commentaires et suggestions ainsi que les différents échanges que nous avons eu m’ont
été d’une grande aide dans la finalisation de ce travail.
Enfin, je souhaite exprimer ma reconnaissance et mes remerciements aux personnes qui m’ont
soutenue et aidé durant les années consacrées à la réalisation de ce travail.