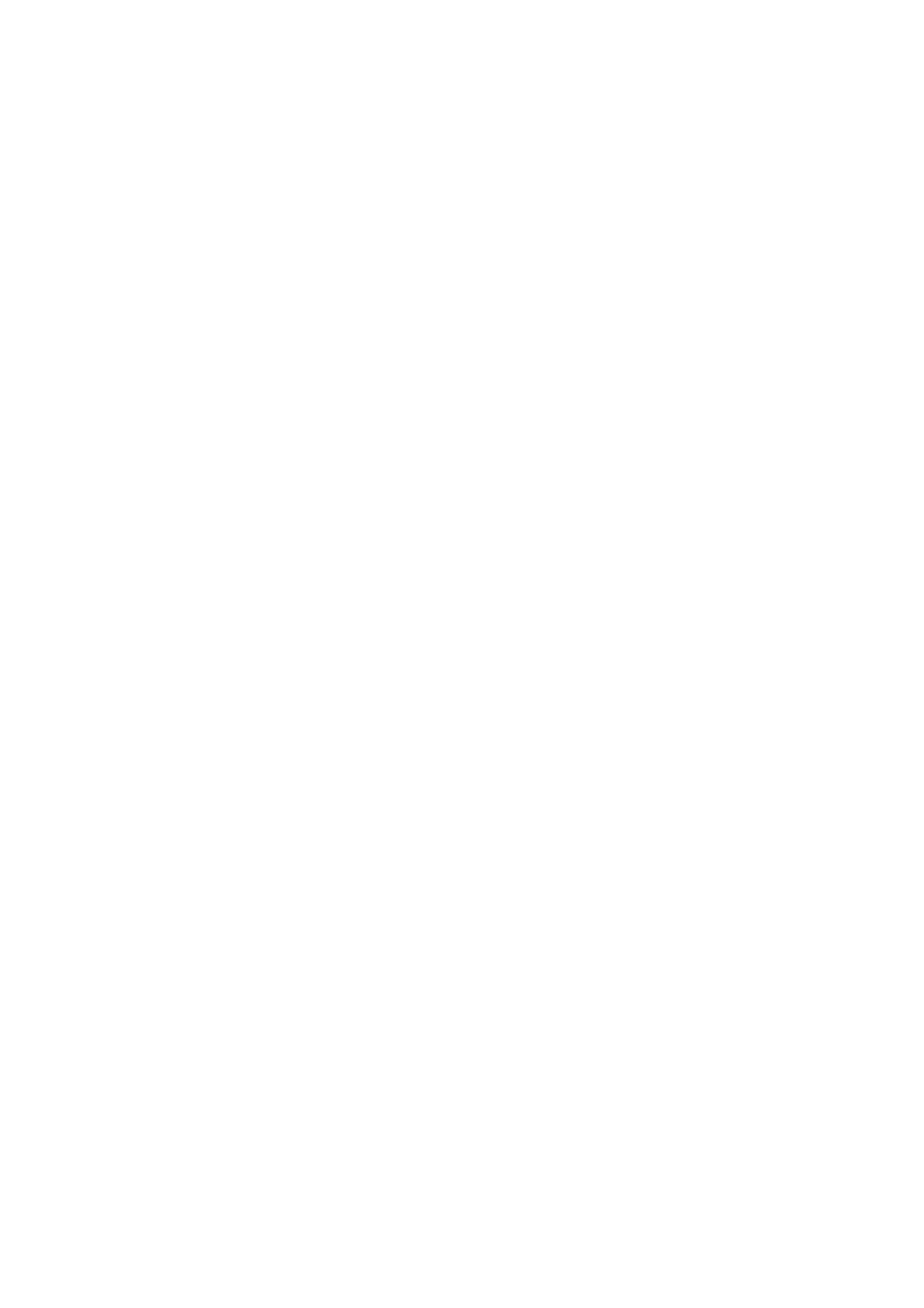
/v
Remerciement
Le travail présenté dans ce mémoire a été effectué au sein du Laboratoire de
Recherche en Électrotechnique de l’École Nationale Polytechnique d’Alger, sous la
direction de Monsieur Rachid Ibtiouen, Professeur à l'ENP. Je tiens à le remercier pour
la confiance qu’il m’a témoignée en acceptant de diriger ce travail. Sa disponibilité et
ses encouragements durant de longues années m’ont été d’un grand apport pour
l’aboutissement de ce travail.
J'exprime aussi, mes remerciements à Monsieur Omar Touhami, Professeur à
l'École Nationale Polytechnique, d'avoir codirigé cette thèse. Sa disponibilité, son esprit
critique, ses remarques pertinentes et ses conseils ont été utiles pour mener à terme ce
travail.
Je remercie profondément Monsieur Ahmed Chériti, Professeur à l’Université
à Trois Rivières à Montréal pour sa gentillesse, son aide durant le travail et pour sa
contribution scientifique qui a été très fructueuse dans l’avancement de ce travail.
Je tiens à exprimer mes vifs remerciements à Monsieur Ahmed Boubakeur,
Professeur à l’École Nationale Polytechnique, pour l’honneur qu’il me fait de présider
le jury de soutenance.
Que Messieurs Saïd Mekhtoub, Maître de Conférences à l’École Nationale
Polytechnique, Larbi Hadjout et Youcef Ouazir, Maîtres de Conférences à
l’USTHB trouvent, ici l’expression de ma profonde gratitude, pour avoir accepté
d’examiner et critiquer cette thèse.
Mes remerciements s’adressent aussi à Monsieur Karim Atif, Maître de
Conférences à l’USTHB, pour ces encouragements qui me poussaient toujours vers
l’avant.