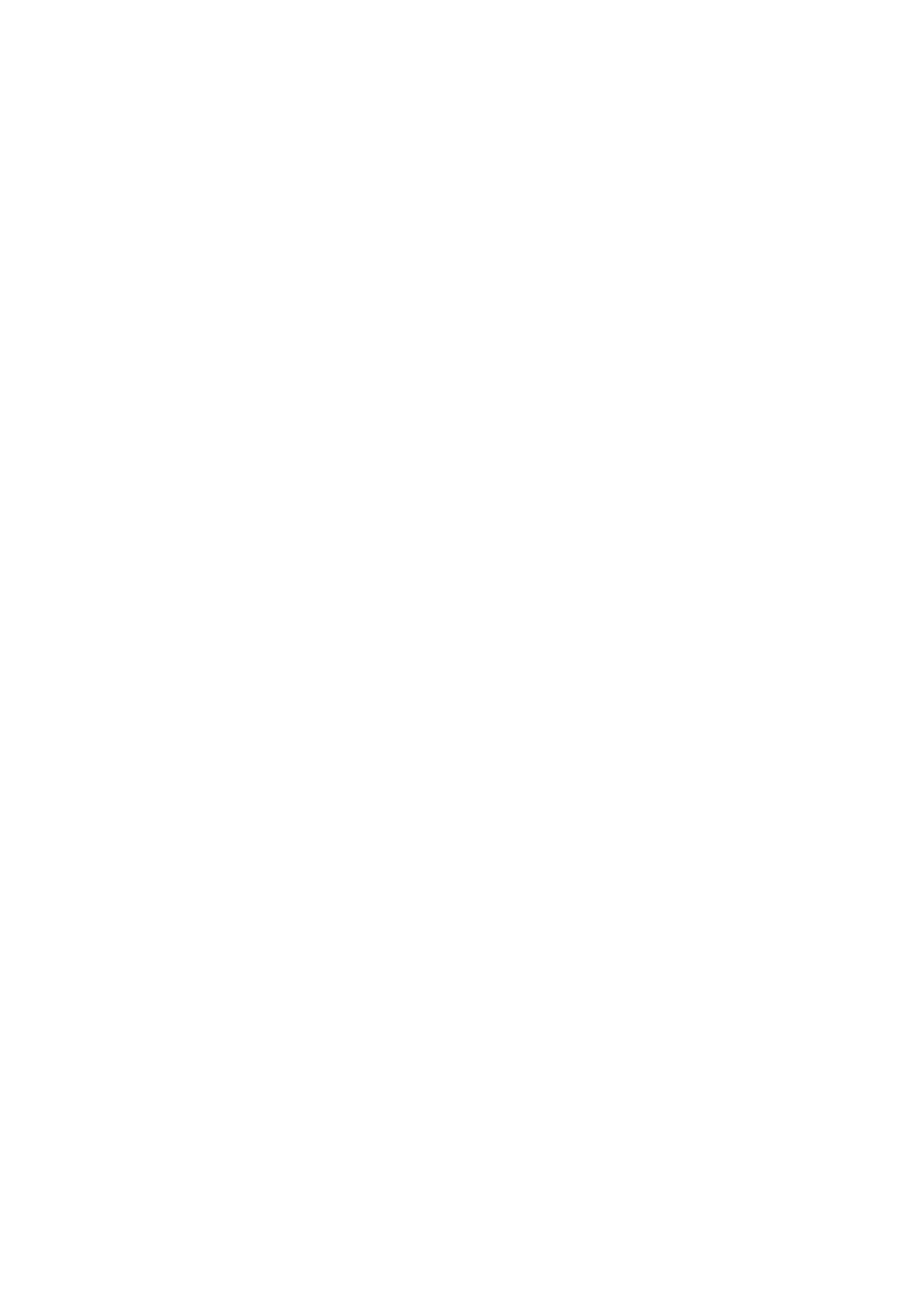
Remerciements
Ces travaux de thèse ont été effectués au sein du groupe Intégration des Systèmes de Gestion de
l’énergie (ISGE) du Laboratoire d’Analyse et d’Architecture des Systèmes (LAAS) du CNRS à
Toulouse.
Avant d’exprimer mes remerciements pour toute personne ayant participé à ce travail de thèse, je
voudrais tout d’abord rendre hommage à mon directeur de thèse ; Monsieur Jean-Louis SANCHEZ
décédé le 15 Mai 2011 suite à une crise cardiaque.
Monsieur SANCHEZ était, au-delà de ses qualités scientifiques, un modèle d’humanité, de gentillesse,
de simplicité et de modestie. C’est grâce à son encouragement et ses conseils que mon travail de thèse
a pu avancer. J’ai eu l’honneur d’être encadré par quelqu’un comme Jean-Louis SANCHEZ. C’est
vraiment très triste son départ définitif.
Je tiens à remercier en premier lieu Messieurs CHATILA, SANCHEZ et ARLAT directeurs successifs
du LAAS, ainsi Madame BAFLEUR, responsable du groupe ISGE, pour m’avoir accueilli et permis
d’entreprendre cette étude.
Je remercie énormément Messieurs SCHAEFFER Christian et KHATIR Zoubir, qui ont accepté de
rapporter sur les travaux de ma thèse. Je remercie également les membres du jury, Messieurs
ROUGER Nicolas et DUPUY Philippe, ainsi que Monsieur BIDAN Pierre qui m’a fait l’honneur de le
présider avec toute sa modestie.
Je remercie en particulier, mon co-directeur de thèse Abdelhakim BOURENNANE pour son aide
scientifique et son suivi permanent de ce travail. Tu as accompli ton travail plus qu’il fallait. Merci
pour ta confiance que tu m’as fait durant toutes ces années et merci beaucoup pour l’énorme temps que
tu as consacré pour réussir ce travail (jusqu’à 5h00 du matin en plusieurs fois). C’était très agréable de
mener ce travail de thèse avec toi. Tes prochains thésards vont le confirmer sans doute. Si ce travail de
thèse est qualifié pour un prix de thèse de l’école doctorale GEET, c’est bien grâce à toi.
Je remercie énormément madame Marie BREIL-DUPUY pour son aide pertinent dans ce travail et
pour ses corrections de ce manuscrit.
Un grand merci aux personnels de la centrale technologique du LAAS pour leur patience et
compréhension, en particulier Eric IMBERNON, Djaffar BELHARET, Laurent BOUSCAYROL,
Laurent MAZENQ…
Je voudrais également remercier mes collègues du bureau Emanuel, Gaëtan et Hussein pour avoir
rendu cette période, si agréable par la bonne ambiance, par l’échange d’informations et par l’entraide
sur tous les plans.