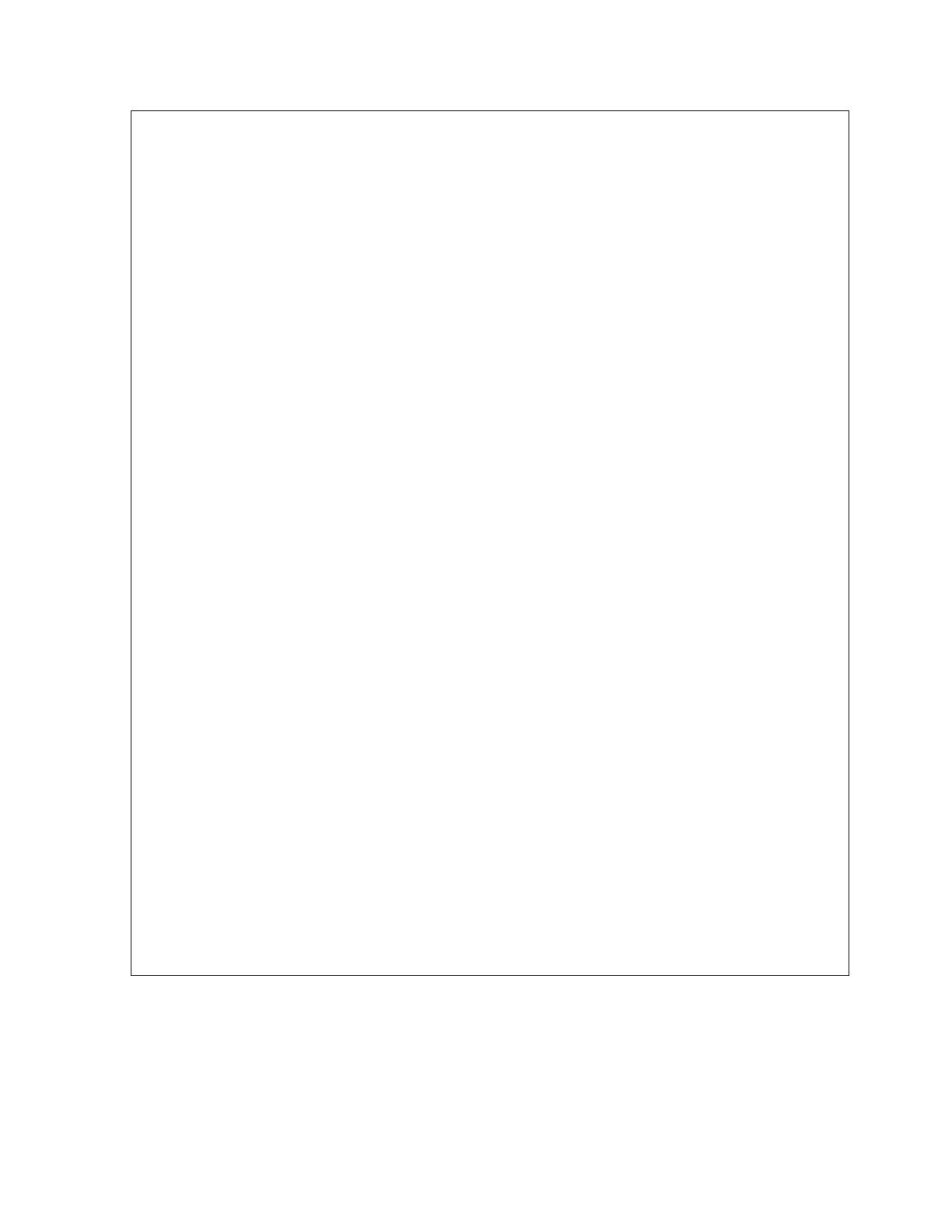
Le gaz naturel constitue une source d’énergie polyvalente qui peut être employée dans des
domaines très varies bien que la production de l’ammoniac et le méthanol via le gaz de
synthèse.
Le reformage du méthane regroupe les réactions ayant lieu entre le méthane et un oxydant
(O2, CO2 ou H2O ) pour former du gaz de synthèse, qui est un mélange de CO et H2.
dans notre présent travail nous avons étudié la réaction de reformage du méthane par dioxyde
de carbone qui présente de nombreux avantages par rapport au reformage à la vapeur,
notamment ceux d’utiliser deux gaz à l’effet de serre et d’aboutir à un gaz de synthèse
présentant un rapport H2/CO faible proche a l’unité.
La première partie da la présente étude sur des catalyseurs de type HYDROTALCITE. Ces
solides catalytiques à base de Nickel et d`aluminium, préparés par la méthode de
Coprécipitation à différentes rapports (R=2, 3, 5, 8 et 10), et différents pH (pH=5, 8, 10 et12)
La formule chimique généralement de nos solides ont été déterminée par l’Analyse chimique.
Leur propriétés texturales ont été caractérisées par la méthode de mesure des surface
spécifique (BET). Les propriétés structurales ont été caractérisées par diffraction des Rayons
X, et spectroscopie IR (FTIR).
Les propriétés catalytiques ont été déterminées a l’aide d’un test catalytique muni d’un
réacteur en quartz.
Plusieurs paramètres ont été examinés sur les solides élaborés.
L’étude de la réaction de reformage du méthane par dioxyde de carbone en présence de ces
catalyseurs a montré que les performances catalytiques en fonction de température de la
réaction sont améliorés quand la température de réaction augmente, cette augmentation
dépendent aussi de la température calcination, de rapport molaire Ni/Al et de pH de
préparation de nos solides. Globalement, nos solides peuvent être classés selon l’ordre
croissant de leurs performances catalytique comme l’indique la séquence suivante :
Pour l’effet de température de calcination (NiAl-T): NiAl-800 < NiAl-700 < NiAl-600<
NiAl-500.
Pour l’effet de rapport molaire (NiAl-R) : NiAl-10 < NiAl-8 < NiAl-5 < NiAl-3 <
NiAl-2.
Pour l’effet de pH (NiAl-pH) : NiAl-12 < NiAl-10 < NiAl-8 < NiAl-5.
Par ailleurs l’étude de la réaction en fonction du temps de la réaction a montré que nos solide
sont actifs des les premières minute, et sont stable durant 6h du travail.
Mémoire de magister : TOUAHRA Fouzia
1 ** Directeur de thèse : D, Halliche, Maître de Conférences, USTHB.