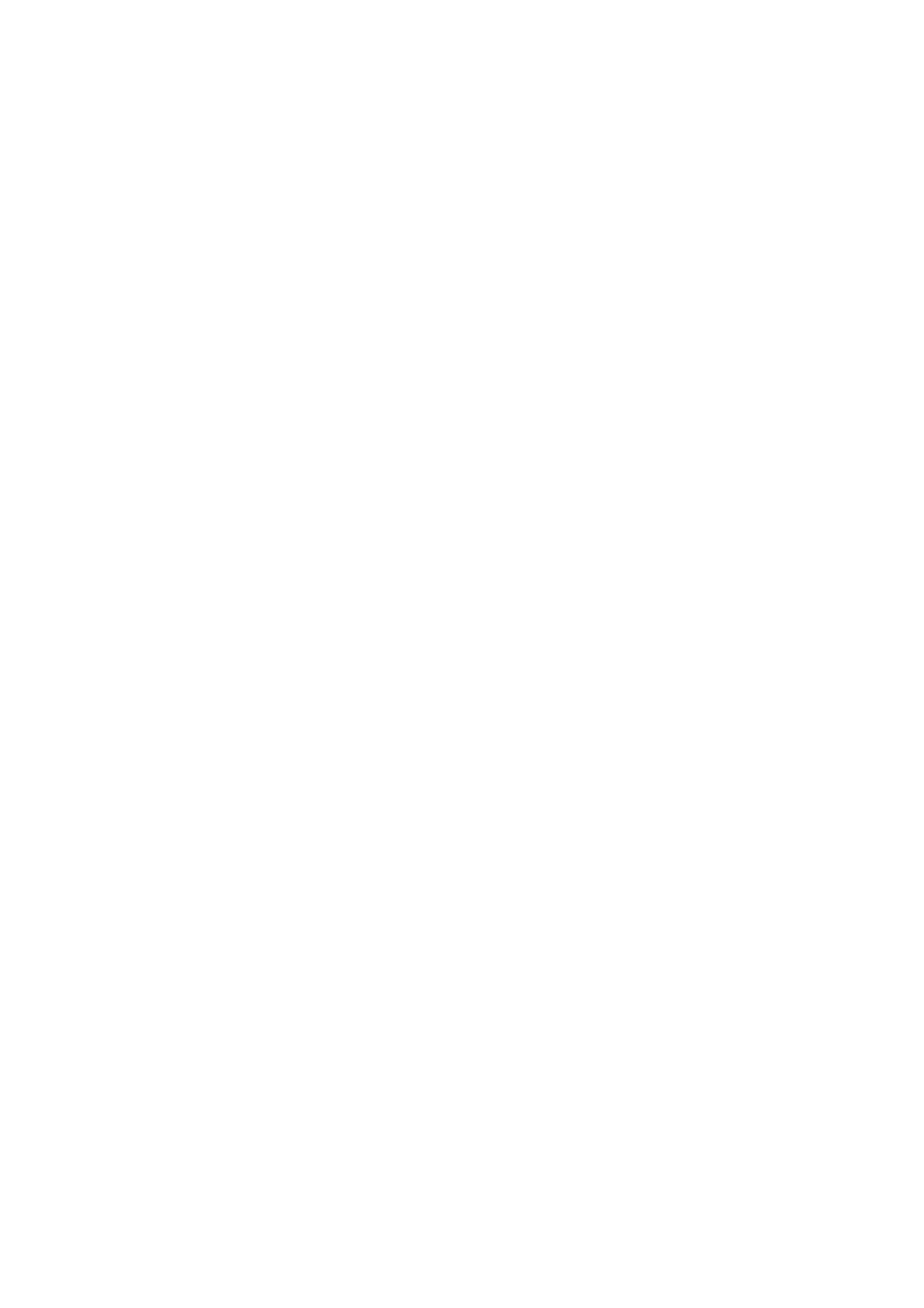
4
5.4.2 Procédé KALDO .......................................................................................... 75
5.4.3 Les aciers à oxygène ..................................................................................... 76
5.5 . Le procédé Martin ..........................................................................................76
5.5.1 Types du procédé Martin................................................................................77
5.5.2 Marche de l'opération.................................................................................... 78
5.5.3 Affinage du bain métallique........................................................................... 79
5.5.4 Les aciers Martin ............................................................................................80
5.6 Le four électrique ........................................................................................ 80
5.6.1 Type de fours électriques................................................................................ 80
5.6.2 Le four HEROULT ........................................................................................81
5.6.3 Les principales matières premières du four électrique ................................... 82
5.6.4 Marche d'une opération dans le four électrique...............................................84
5.6.5 Classification des aciers le procédé d'affinage et % C.....................................85
5.7 Coulée de l'acier........................................................................................... 85
5.7.1 Coulée en lingotières ...................................................................................... 86
5.7.2 La coulée continu...........................................................................................88
5.8 Différents types de coulées selon le degré de désoxydation.........................90
5.8.1 La coulée calmée............................................................................................ 90
5.8.2 La coulée effervescente ...................................................................................92
5.8.3 La coulée semi-calmee .................................................................................... 93
5.9 Coulée sous vide ...........................................................................................93
5.10 Défauts de lingots ......................................................................................... 93
6. Diagramme Fer-carbone.........................................................................................97
6.1 Le fer et ses caractéristiques ......................................................................... 97
6.2 Le carbone et ses caractéristiques.................................................................100
6.3 Diagramme d'équilibre Fer-carbone.............................................................101
6.3.1 Les points caractéristiques du diagramme.......................................................102
6.3.2 Définition des constituants.............................................................................. '04
6.3.3 Les transformations ..................................................................................... 111
- Aciers hypoeutectiques...............................................................................112
- Aciers eutectoides...................................................................................... 116
- Aciers hypereutectoides ............................................................................. 118
- Fontes hypoeutectiques.............................................................................. 121
- Fontes eutectiques................................................................................... 122
- Fontes hypereutectiques .......................................................................... 123
6.4 Détermination de la position des composants de la stmcture......................... 123
6.5 Diagramme d'équilibre Fer-graphite ..............................................................129
7. Désignation normalisée des aciers et fontes............................................................132
7.1 Désignation des aciers................................................................................... 132
7.1.1 Désignation des aciers ordinaires sans traitements thermiques ....................... 133
7.1.2 Désignation des aciers pour traitements thermiques........................................ 135
7.1.3 Désignation des aciers alliés ..............................................................................136
7.1.3.1 Désignation des aciers faiblement alliés......................................................... 137
7.1.3.2 Désignation des aciers fortement alliés........................................................... 138
7.2 Désignation des fontes .................................................................................... 139
7.2.1 Désignation des fontes non alliées .....................................................................140
7.2.2 Désignation des fontes alliées ...........................................................................141
7.2.3 Désignation des fontes malléables .....................................................................141