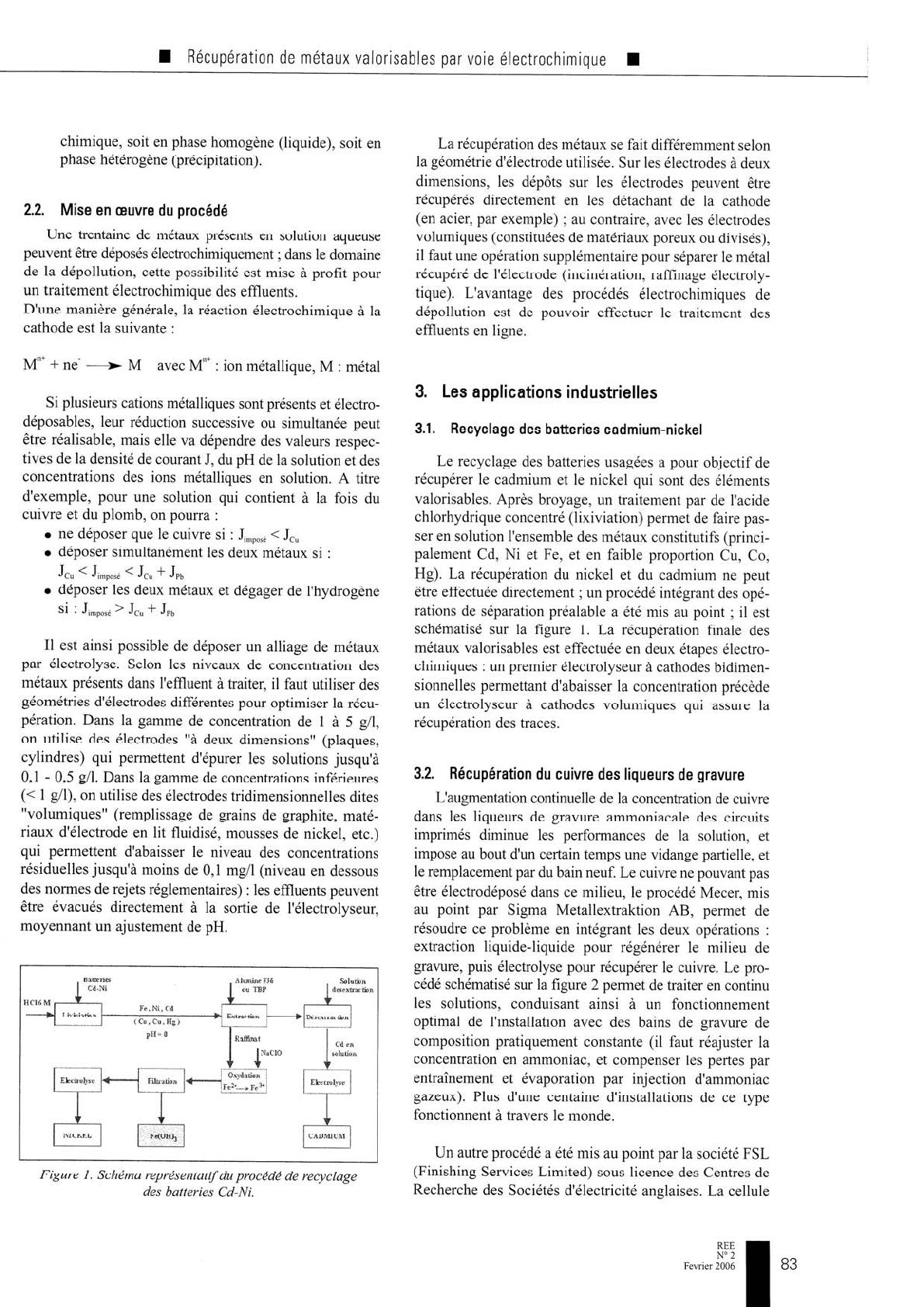
Récupération de métaux valorisables par voie électrochimique
chimique, soit en phase homogène (liquide), soit en
phase hétérogène (précipitation).
2.2. Mise en ceuvre du procédé
Une trentaine de métaux présents en solution aqueuse
peuvent être déposés électrochimiquement ; dans le domaine
de la dépollution, cette possibilité est mise à profit pour
un traitement électrochimique des effluents.
D'une manière générale, la réaction électrochimique à la
cathode est la suivante :
La récupération des métaux se fait différemment selon
la géométrie d'électrode utilisée. Sur les électrodes à deux
dimensions, les dépôts sur les électrodes peuvent être
récupérés directement en les détachant de la cathode
(en acier, par exemple), au contraire, avec les électrodes
volumiques (constituées de matériaux poreux ou divisés),
il faut une opération supplémentaire pour séparer le métal
récupéré de l'électrode (incinération, raffinage électroly-
tique). L'avantage des procédés électrochimiques de
dépollution est de pouvoir effectuer le traitement des
effluents en ligne.
Tt + ne-M +ne M avec M " : ion métallique, M : métal
Si plusieurs cations métalliques sont présents et électro-
déposables, leur réduction successive ou simultanée peut
être réalisable, mais elle va dépendre des valeurs respec-
tives de la densité de courant J, du pH de la solution et des
concentrations des ions métalliques en solution. A titre
d'exemple, pour une solution qui contient à la fois du
cuivre et du plomb, on pourra :
. ne déposer que le cuivre si : J.... 1,0é < Jen
. déposer simultanément les deux métaux si :
JCu < Jfmposé < JCu + JPb
. déposer les deux métaux et dégager de l'hydrogène
si : Jimpose
> ir.. + i
ICU Pb
Il est ainsi possible de déposer un alliage de métaux
par électrolyse. Selon les niveaux de concentration des
métaux présents dans l'effluent à traiter, il faut utiliser des
géométries d'électrodes différentes pour optimiser la récu-
pération. Dans la gamme de concentration de 1 à 5 g/l,
on utilise des électrodes " à deux dimensions " (plaques,
cylindres) qui permettent d'épurer les solutions jusqu'à
0,1 - 0,5 g/1. Dans la gamme de concentrations inférieures
« 1 g/1), on utilise des électrodes tridimensionnelles dites
" volumiques " (remplissage de grains de graphite, maté-
riaux d'électrode en lit fluidisé, mousses de nickel, etc.)
qui permettent d'abaisser le niveau des concentrations
résiduelles jusqu'à moins de 0, 1 mg/1 (niveau en dessous
des normes de rejets réglementaires) : les effluents peuvent
être évacués directement à la sortie de l'électrolyseur,
moyennant un ajustement de pH.
Rxtteiu
Cd Ni ; 3b
,, rgp
li ('l e Ni
Li k, iitib l Ft,Ni, Cd -k- 1-1,P
C,, Cu 14
pll- a E.\irarn
I-R-,ffimf
5olntimSolution
Ë7
10
Ei.ffb't !' Filuution O.'dUMM
Ft,-. r,
; fc1+--- : o- F e} +
iD,,,,., fi,, 1- ---. : -----.. "..-- j
C'dzn('.1 en
Etffmjivt-
i--
1 : ] 1 CAD : thl 1
CADMR'h !
Figure 1. Schéma représentatif dit procédé de reclvclage
des batteries Cd-Ni.
3. Les applications industrielles
3.1. Recyclage des batteries cadmium-nickel
Le recyclage des batteries usagées a pour objectif de
récupérer le cadmium et le nickel qui sont des éléments
valorisables. Après broyage, un traitement par de l'acide
chlorhydrique concentré (lixiviation) permet de faire pas-
ser en solution l'ensemble des métaux constitutifs (princi-
palement Cd, Ni et Fe, et en faible proportion Cu, Co,
Hg). La récupération du nickel et du cadmium ne peut
être effectuée directement ; un procédé intégrant des opé-
rations de séparation préalable a été mis au point, il est
schématisé sur la figure 1. La récupération finale des
métaux valorisables est effectuée en deux étapes électro-
chimiques : un premier électrolyseur à cathodes bidimen-
sionnelles permettant d'abaisser la concentration précède
un électrolyseur à cathodes volumiques qui assure la
récupération des traces.
3.2. Récupération du cuivre des liqueurs de gravure
L'augmentation continuelle de la concentration de cuivre
dans les liqueurs de gravure ammoniacale des circuits
imprimés diminue les performances de la solution, et
impose au bout d'un certain temps une vidange partielle, et
le remplacement par du bain neuf. Le cuivre ne pouvant pas
être électrodéposé dans ce milieu, le procédé Mecer, mis
au point par Sigma Metallextraktion AB, permet de
résoudre ce problème en intégrant les deux opérations :
extraction liquide-liquide pour régénérer le milieu de
gravure, puis électrolyse pour récupérer le cuivre. Le pro-
cédé schématisé sur la figure 2 permet de traiter en continu
les solutions, conduisant ainsi à un fonctionnement
optimal de l'installation avec des bains de gravure de
composition pratiquement constante (il faut réajuster la
concentration en ammoniac, et compenser les pertes par
entraînement et évaporation par injection d'ammoniac
gazeux). Plus d'une centaine d'installations de ce type
fonctionnent à travers le monde.
Un autre procédé a été mis au point par la société FSL
(Finishing Services Limited) sous licence des Centres de
Recherche des Sociétés d'électricité anglaises. La cellule
REE
N.
Fevrier 2006