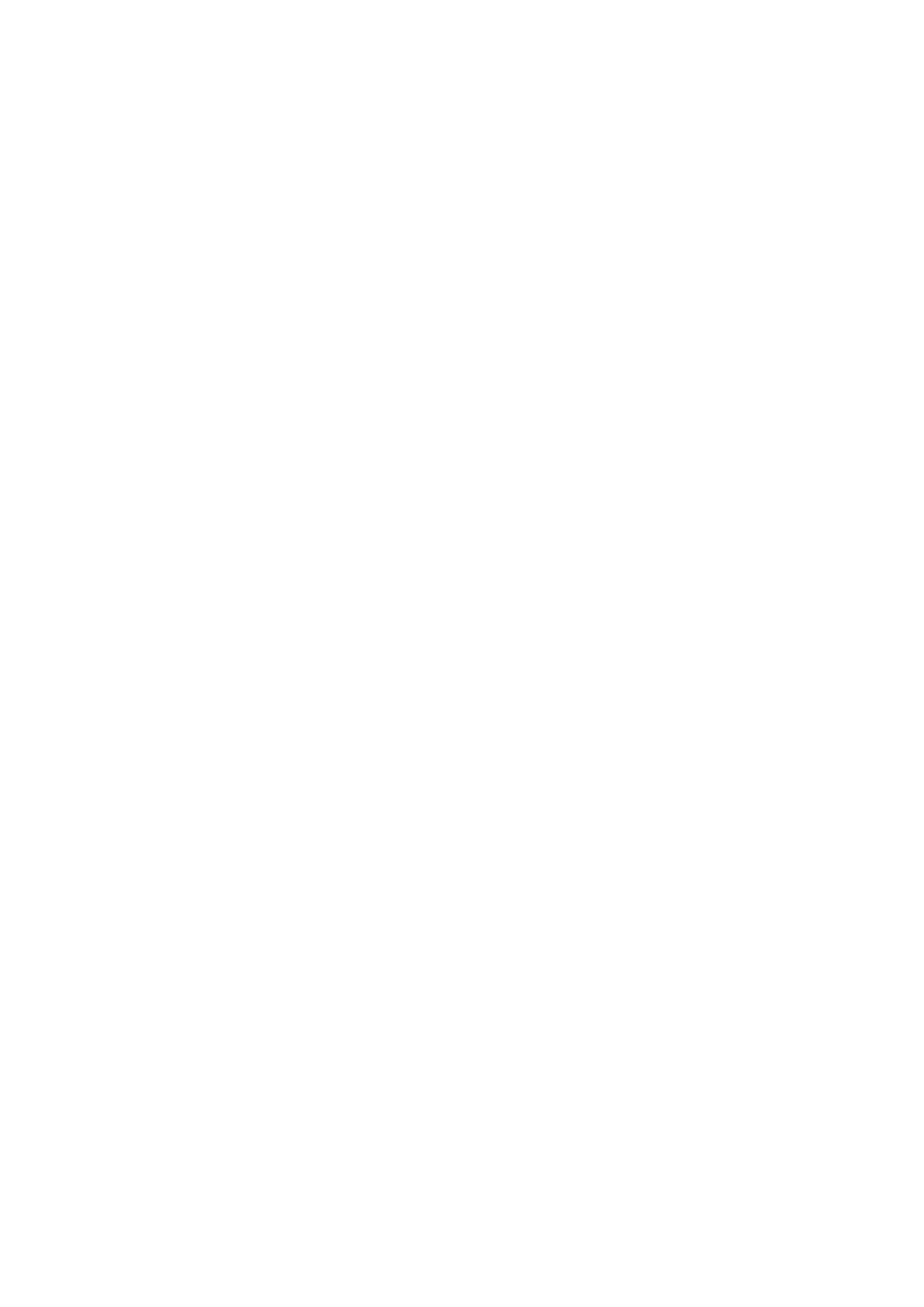
Remerciements
Les travaux de recherche présentés dans ce manuscrit ont été réalisés à l’Institut de
Chimie de la Matière Condensée de Bordeaux (ICMCB). En premier lieu, j’adresse mes
remerciements à Mr Claude Delmas pour m’avoir accueillie à l’ICMCB et pour avoir accepter
de présider mon jury de thèse.
Je souhaite également remercier MM. Yannick Champion et Philipe Serp pour avoir
accepter de juger ce travail de thèse.
Je remercie Mélanie Majimel, Cyril Aymonier et François Cansell pour l’encadrement de
cette thèse, ainsi que ARKEMA et Patrice Gaillard pour avoir soutenu ce projet de thèse.
J’adresse mes remerciements à toutes les personnes avec qui j’ai pu collaborer de près ou
de loin : Christine Labrugère, Thierry Tassaing, Ovidiu Ersen, Christelle Jaillet-Bartholome,
Alain Largeteau, Jean François Silvain, Cécile Vincent, Jérôme Majimel et les stagiaires ainsi
que les membres du CREMEM, le service DRX, tout le personnel de l’ICMCB et un grand
merci à Stephane Toulin !
Et pour finir, parce qu’une thèse c’est bien mais avec des amis c’est mieux, un grand
merci à : Sabine, Romain, Manu, Cédric, David, Nico Nico, Iona, Nico N., Etienne, Cécile,
Yohan, Antoine, Thomas, Aurélie, Cinta, Amina, Samuel, Amaury, Samuel, Cédric x2,
Mathieu, Anne-Claire…