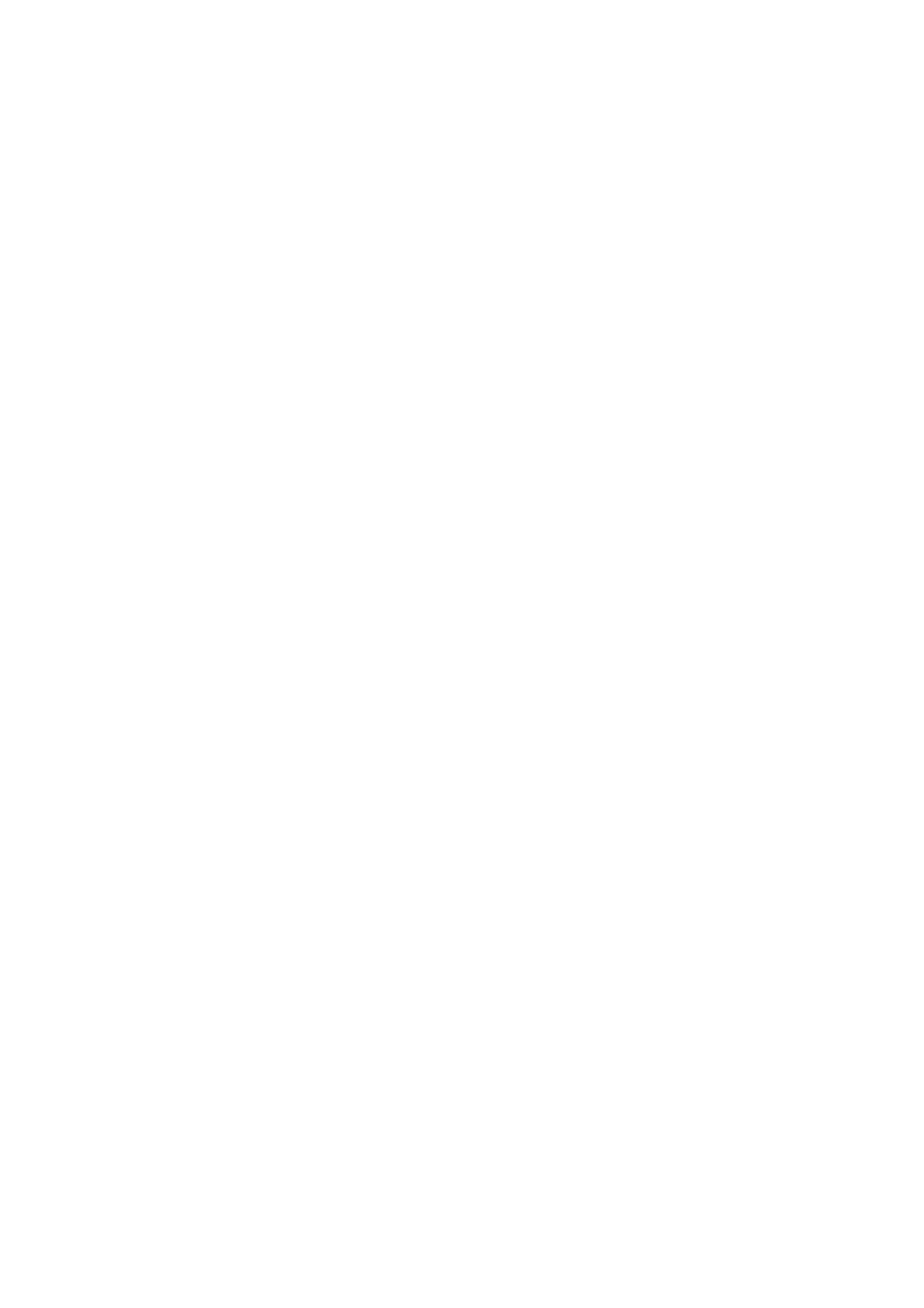
Ce travail a été réalisé au Laboratoire des Matériaux, Surface et Procédés pour la
Catalyse sous la direction des Dr. V. Pitchon, Chargée de Recherche et Dr. C. Petit, Maître de
Conférences.
Mes remerciements les plus vifs vont à mes directrices pour leur disponibilité, les
nombreux conseils qu’elles m’ont donnée et la liberté qu’elles m’ont laissée pour réaliser ce
travail. Nos conversations et nos relations humaines ont fait mon séjour à Strasbourg
inoubliable. Un grand MERCI pour tout!
Je tiens à exprimer ma profonde reconnaissance à Monsieur A. Kiennemann,
Professeur à l’Université Louis Pasteur de Strasbourg pour m’avoir accueillie au sein de son
équipe et m’avoir donne l’opportunité de travailler dans son laboratoire.
Je remercie très respectueusement Monsieur J.-M. Planeix, Professeur à l’Université
Louis Pasteur de Strasbourg d’avoir accepté la présidence de mon jury.
Je remercie également Madame C. Louis, Directeur de Recherche au CNRS et
Monsieur Pascal Granger Professeur à l’Université de Lille I pour l’honneur qu’ils me font de
juger ce travail.
Mes remerciements vont également à Monsieur L. Charbonnière, Monsieur D. Lakkis,
Monsieur H. Herschbach et Mme E. Leize, Monsieur P. Bernhardt pour l’aide et les précieux
conseils et les fructueuses conversations dans le domaine de la Spectrométrie en UV-Visible,
Spectrométrie d’adsorption atomique, Spectrométrie de masse et l’XPS.
Je remercie Mintek-Anglogold, Afrique du Sud d’avoir assuré mon financement
pendant les trois années de thèse.
Merci à l’ensemble du personnel du laboratoire pour leur accueil chaleureux.
1000 mercis à
- Maryse Bacri, pour mes devoirs de français, pour la cohabitation très agréable, pour
son soutien moral et pour les corrections de grammaire et d’orthographe de ce manuscrit.
- Suzanne Libs, pour son aide technique précieuse et pour les moments très agréables
passés au coin café.
- Yvan Zimmermann, pour les nombreuses particules d’or observées et comptées et
pour son humour.
- Raymonde Touroude, pour tout ce que j’ai pu apprendre à ses côtés.
- aux soeurs Novakovi, pour avoir bien géré mes crises de nostalgie et supporté mon
mauvais caractère.
Enfin, mes amis la vie est belle avec vous. Ma famille et mon coeur ont grandi.
Juliana, Iza Bury, Marta, Iliana, Fatima, Yvonne, Anne-Cécile, Anja et Lara – les filles
vous savez pourquoi
Darek, Julio, Seb, Miguel, Alex, Thomas, Laurent, Renaud – les garçons on est bien
ensemble.
Que tous que j’ai pu oublier me pardonnent.