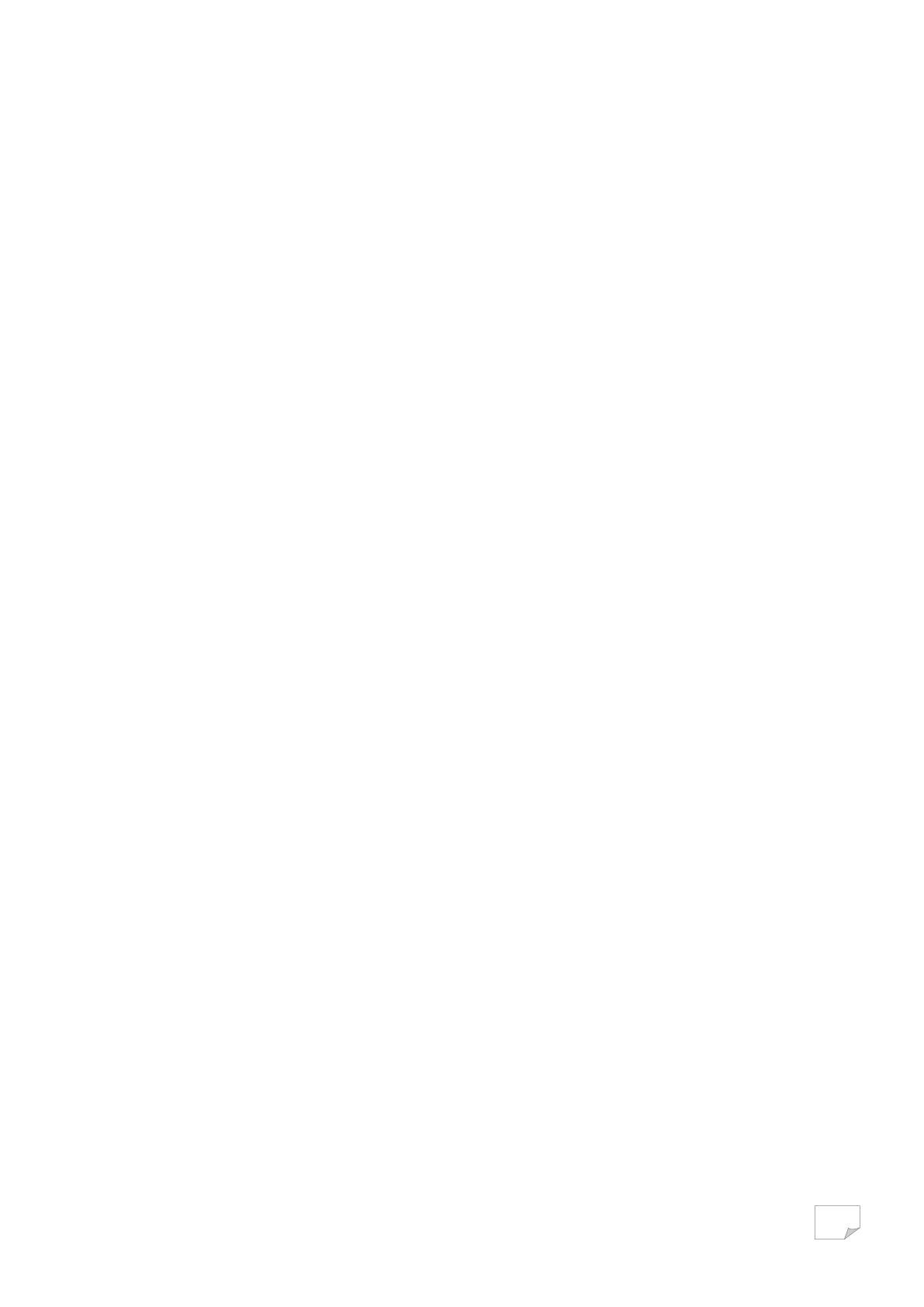
Sommaire………………………………………………………………………………………1
Introduction générale…………………………………………………………………………..5
Chapitre 1 : Cellules PV en Si et le Si en couches minces.........................................................7
Introduction……………………………………………………….............................................8
I- Les cellules PV à base de Si…………………………………………………………………8
I.1.Notions préliminaires sur le rayonnement solaire………………………………………….8
I.2.Principe de fonctionnement de la cellule photovoltaïque…………………………………..9
I.3. Caractérisation physique des cellules photovoltaïques…………………………………...10
I-4. Les différents types de cellules photovoltaïques…………………………………………13
II-Le Si en couches minces…………………………………………………………………15
II.1. Notion de couche mince………………………………………………………………..15
II.2.Silicium amorphe………………………………………………………………………..16
II.2.1.Définition…………………………………………………………………………….16
II.2.2.Dépôt du silicium amorphe…………………………………………………………...17
II.3.Silicium cristallin …………………………………………………………………….….17
II.3.1.Définition ……………………………………………………………………………...17
II.3.2.Techniques de cristallisation…………………………………………………………...18
II.3.2.1.Cristallisation en phase solide (SPC)………………………………………………...18
II.3.2.2.Technologie CSG (CrystallineSilicon on Glass)…………………………………….18
II.3.2.3.Méthode AIC (Aluminium InducedCrystallisation)………………………………..19
II.3.2.4.Cristallisation par recuit laser………………………………………………………..20
II.4. Cellules à faible budget thermique………………………………………………………20
II.5. Silicium monocristallin………………………………………………………………….22
Méthode de BRIDGEMAN……………………………………………………………22
Méthode de tirage (CZOCHRALSKI) (CZ)……………………………………………23
Méthode de la zone flottante (FZ)……………………………………………………..25
Conclusion……………………………………...…………………………………………….27