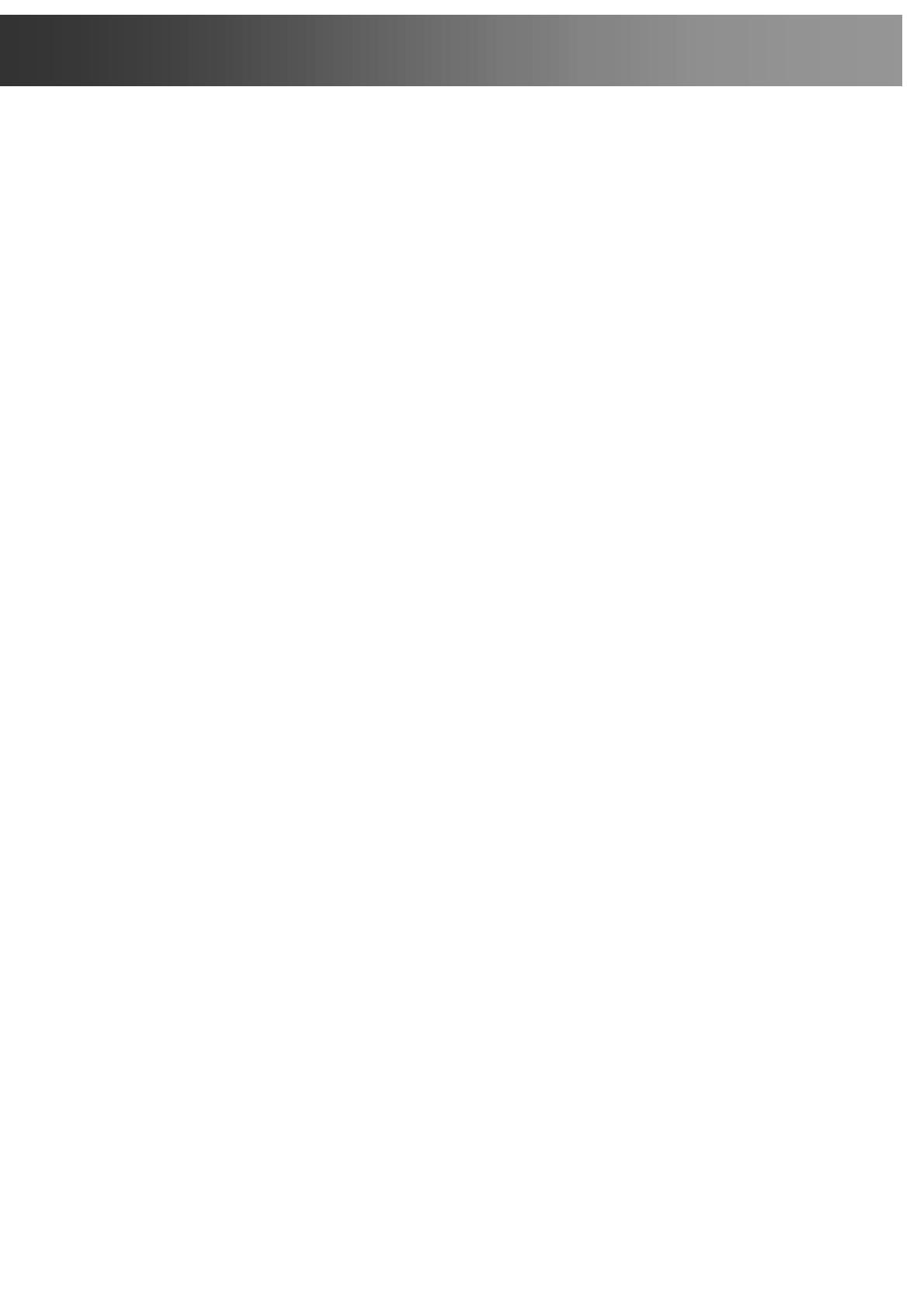
INSA Lyon – Laboratoire Ampère / Institut Saint-Louis 25
Chapitre 1
Le SiC pour l’électronique de puissance
2. Pourquoi le SiC ?
2.1. Un peu d’histoire …
Les premières mentions du carbure de silicium (SiC) remontent à 1824,
cette découverte est attribuée à Berzelius. Sur Terre, ce matériau n’existe pas
sous forme naturelle, la plupart des échantillons naturels sont d’origine extra-
terrestre, apportés par des météorites. En 1905, Moissan découvrit un de ces
échantillons sur une météorite [Mois 05], d’où le nom donné par la suite :
moissanite pour nommer le SiC.
La première synthèse de cristaux SiC a été réalisée par Acheson en 1892
[Ache 92]. Le résultat est le fruit d’une tentative de synthèse accidentelle du
diamant. Dès 1907, Round réalisa la première diode électroluminescente en
SiC [Roun 07].
En 1955, Lely développa une méthode de synthèse de SiC mono-cristallin
[Lely 55]. Par la suite, cette méthode a été approfondie par Tairov et
Tsvetkov [Tair 78]. Leurs travaux permettent la croissance par sublimation
du SiC à partir d’un germe. Cette méthode fut nommée : méthode de Lely
modifiée.
Les principales applications de nos jours sont encore dans les machines
outils de découpe qui mettent en avant les propriétés mécaniques du SiC
(indice de dureté Mohs : 9.5) (diamant : 10). Sous sa forme mono-cristalline,
le SiC est un semi-conducteur à large bande interdite.
Depuis les travaux de Tairov et Tsvetkov, le SiC a eu un intérêt
grandissant dans la réalisation de composants de puissance grâce à ses
propriétés physiques exceptionnelles. La société américaine CREE [Cree 06],
aujourd’hui leader mondial de la fourniture de substrats de SiC
monocristallin, a vu le jour en 1987. La plupart des échantillons utilisés dans
la recherche mondiale sur le SiC proviennent de cette dernière. Plus
récemment, de nouveaux fabricants sont apparus comme SiCrystal [Sicr 06],
Norstel [Nors 06] ou encore II-VI Incorporated [ii-v 06].
2.2. Propriétés du SiC
2.2.1. Cristallographie
Bien que le carbure de silicium monocristallin se compose d’autant
d’atomes de silicium que d’atomes de carbone, il existe plusieurs structures
cristallines suivant la disposition des atomes sur la base de la liaison Si-C. On
parle alors de polytype. La Figure 5 représente un arrangement tétragonal
entre un atome de carbone et quatre atomes de silicium, la distance entre
deux atomes de silicium est de 3,08 Å, et alors qu’elle est de 1,89 Å entre un
atome de silicium et un atome de carbone.