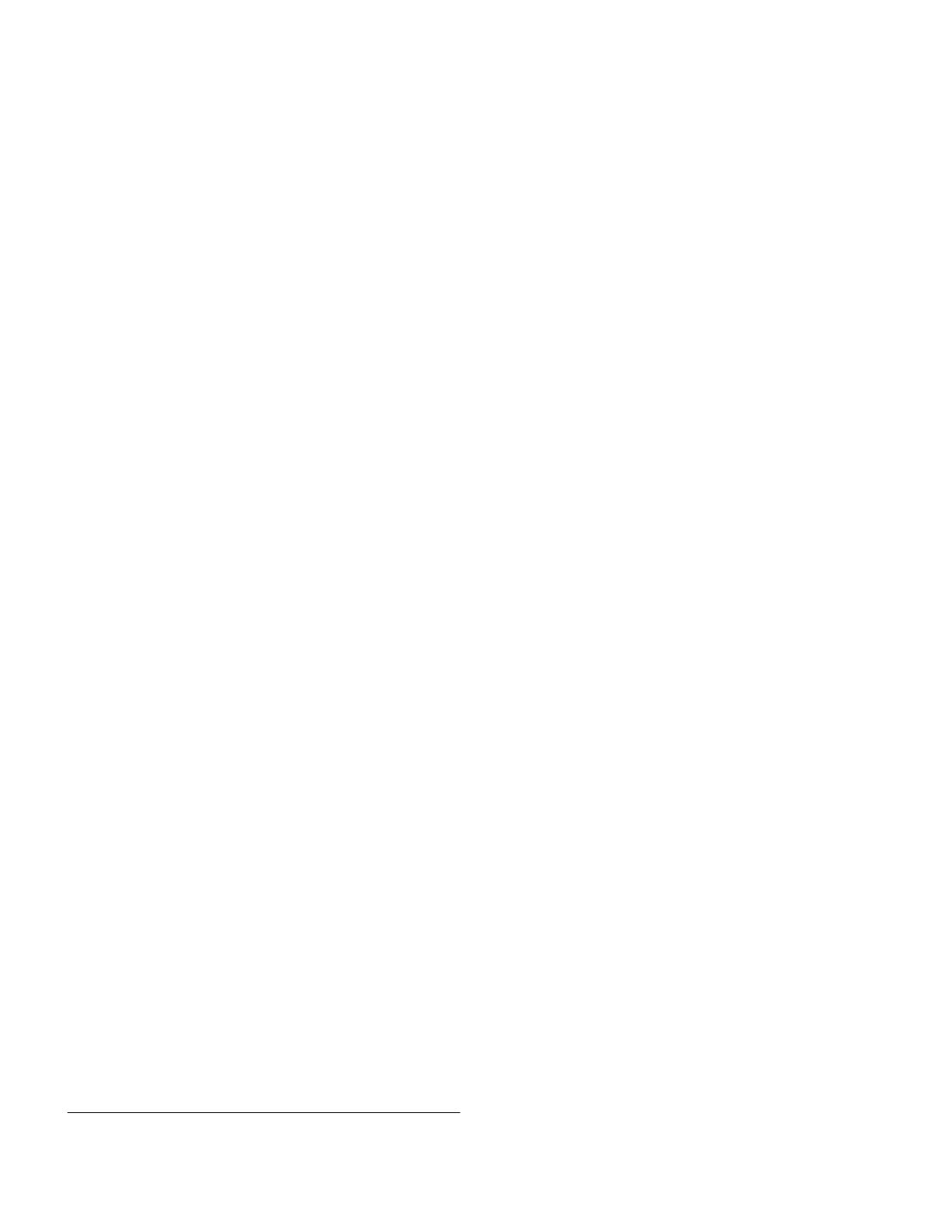
A Phased Calculation Method of Switching Loss of
SiC MOSFET Based on High Power Conditions
Zhi Zheng
School of Electrical Engineering
Xi'an Jiaotong University
Xi’an, China
Yijun Wang
School of Electrical Engineering
Xi'an Jiaotong University
Xi’an, China
Feng Wang
School of Electrical Engineering
Xi'an Jiaotong University
Xi’an, China
Fang Zhuo
School of Electrical Engineering
Xi'an Jiaotong University
Xi’an, China
Abstract—As an emerging wide-bandgap semiconductor
device, SiC MOSFET provides the advantages of high frequency,
high efficiency and high power density for power electronic
devices due to its excellent performance. As an important factor
to study the switching performance of devices, switching loss is of
great significance to its accurate calculation. This paper firstly
analyzes the turn-on and turn-off processes of SiC MOSFETs,
subdivides them into ten stages, and obtains the calculation
method of switching losses in each stage. Then the corresponding
switching loss value is obtained through simulation and
experiment. Finally, the loss value calculated by the proposed
calculation method is compared with the simulation and
experiment, which verifies the high accuracy of the loss
calculation method.
Keywords—SiC MOSFET, switching loss, wide bandgap devices
I. INTRODUCTION
In recent years, power semiconductor devices have
developed from low-power, low-frequency and semi-controlled
to high-power, high-frequency and fully-controlled. As a
representative of wide band gap devices, SiC MOSFET is
applied more frequently in various power electronic devices
because of its various advantages including high voltage
resistance, high temperature resistance and fast switching. It is
widely used in various topologies in high-power scenarios [1],
[2]. The loss modeling and calculation of switching devices has
always been an important part in the evaluation and analysis of
power electronic systems. It is of great significance to the
efficiency prediction and parameter optimization of power
electronic system. But at the same time, the high switching
frequency and complex switching process make the switching
loss analysis of SiC MOSFET more complex [3], [4].
The switching loss of SiC MOSFET can be roughly
calculated through the integration of drain-source voltage and
drain current and switching time. This method is relatively
simple, but the accuracy is not high [5]. Based on the
simplified principle of charge conservation and flux
conservation in the switching process, the SiC MOSFET data
sheet can clearly track the influence of the change of a
parameter on the switching loss while avoiding complex
calculation [6]. Parasitic capacitance and parasitic inductance
are important influencing parameters when modeling the
switch [7], [8]. By considering the switching loss modeling of
parasitic capacitance and parasitic inductance as well as
experimental comparison, the relationship between switching
loss and parasitic parameters can be more accurately illustrated
[9], [10]. Calorimetry is based on relatively slow temperature
measurement and does not rely on the measurement of fast
switching conversion of voltage and current. It can be used to
accurately determine a single loss component, but it heeds high
experimental requirements [11]. Phased switch modeling loss
analysis can be used to accurately determine the loss value of
each stage, but most of the experimental verification is limited
to low-power scenarios [12].
In view of the advantages and disadvantages of the above
methods, this paper proposes a phased calculation method of
SiC MOSFET switching loss under high power conditions. The
switching process of SiC MOSFET is divided into ten stages,
and the parameters of each stage are modeled and analyzed in
detail by using the switching characteristics and considering the
influence of parasitic parameters in the circuit. On this basis,
the actual switching loss of SiC MOSFET can be calculated by
substituting the device parameters and electrical parameters
under actual working conditions. In order to verify the
reliability of the proposed method under high power density
conditions, the Ltspice simulation results and the experimental
results of dual-pulse test platform under high power density
conditions are compared and analyzed respectively, which
verifies the accuracy of the proposed calculation method.
II. OPENING PROCESS MODELING AND LOSS ANALYSIS
Silicon carbide power device is a voltage-controlled device
and acknowledging its switching characteristics is of great
significance to analyze its switching loss. In most power
electronics applications, the switching process of silicon
carbide power devices can be described by diode clamped buck
circuit based on inductive load. In this paper, the driven lower
tube in the half bridge is used as the switch tube, and the upper
tube in the off state is equivalent to a diode. Its equivalent
circuit is shown in Fig. 1. Among them, this paper will take it
as the basis for studying the phased calculation method of SiC
MOSFET switching loss under high power conditions.
Fig. 2 shows the turning on process curve of SiC MOSFET.
The turn-on process can be divided into five states according to
the gate-source voltage and the state of the device: opening
delay stage, the current rise stage, the rapid voltage drop stage,
the slow voltage drop stage and the grid charging stage. The
circuit equivalent diagram of each stage is shown in Fig. 3.
This work was supported by the Shaanxi Province Key Research and
Development Program Project: Design and Simulation of Medium and Low
Voltage DC Power Distribution Multi-Port Converters for Distributed Energy
-
170
2022 The 4th International Conference on Power and Energy Technology
978-1-6654-8079-6/22/$31.00 ©2022 IEEE
2022 4th International Conference on Power and Energy Technology (ICPET) | 978-1-6654-8079-6/22/$31.00 ©2022 IEEE | DOI: 10.1109/ICPET55165.2022.9918410
Authorized licensed use limited to: UNIVERSITE DE SOUSSE. Downloaded on December 04,2023 at 05:09:20 UTC from IEEE Xplore. Restrictions apply.