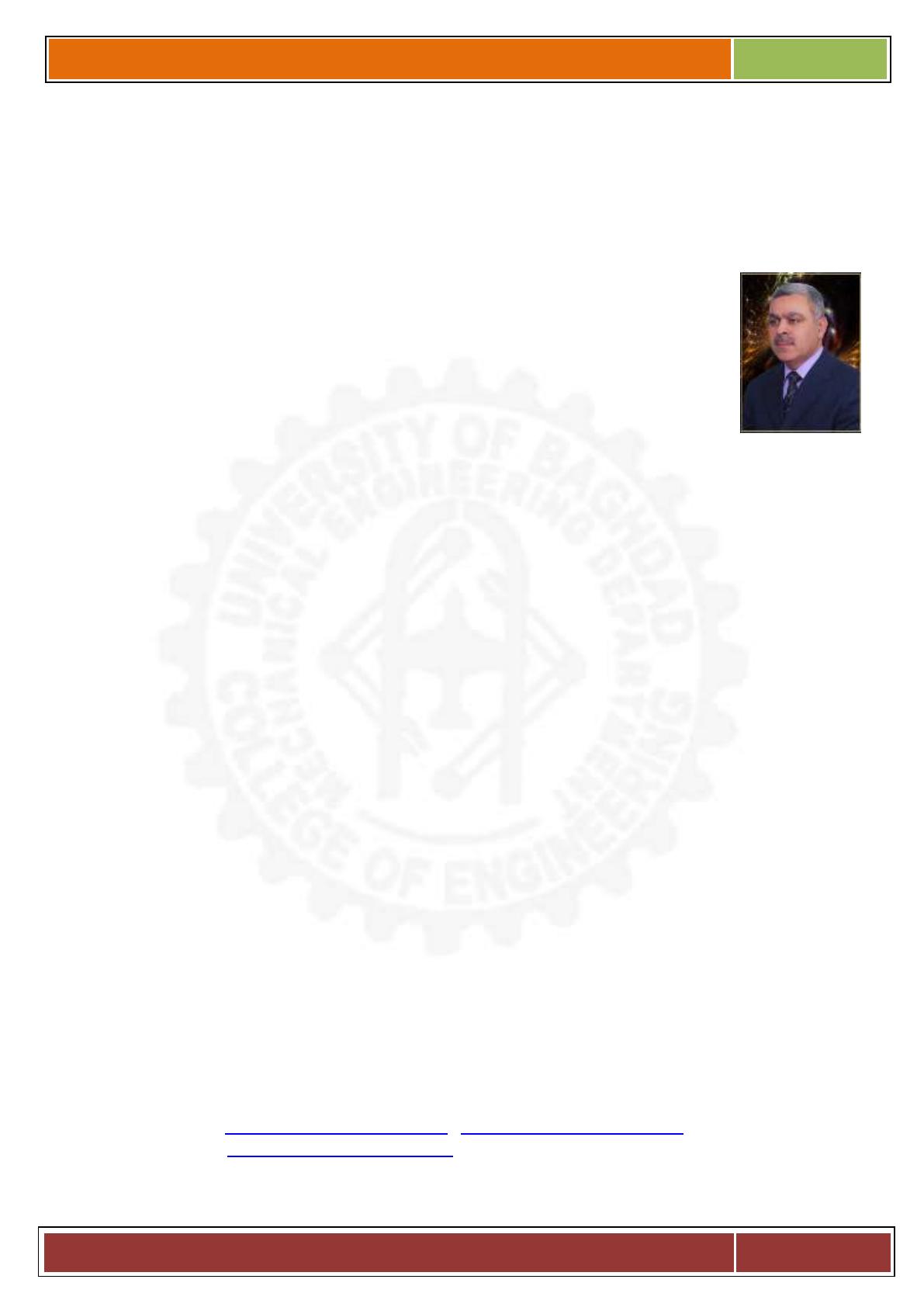
Incompressible Fluid Mechanics
Prof. Dr. Ihsan Y. Hussain / Mech. Engr. Dept. - College of Engr. – University of Baghdad
Preface
The present book is a handout lectures for the B.Sc. Course
ME202 : Fluid Mechanics / I. The course is designed for B.Sc. Sophomore Students in
the Mechanical Engineering Discipline. The time schedule needed to cover the course
material is 32 weeks, 3 hrs. per week. The course had been taught by the author (course
tutor) for more than 25 years. A short c.v. for the author is given below;
Prof. Dr. Ihsan Y. Hussain / Baghdad - 1964
B.Sc. ( 1986 ), M.Sc. ( 1989 ), & Ph.D. ( 1997 ) in Mechanical
Engineering from the Mech. Engr. Dept. – University of Baghdad
Professor of Mechanical Engineering – Thermo-Fluids
Teaching Undergraduate Courses and Laboratories in Various
Iraqi Universities ( Baghdad, Al-Kufa, Babylon, Al - Nahrain ….)
in Various Subjects of Mechanical Engineering
Teaching Advanced Graduate Courses (M.Sc. and Ph.D.) in various
Iraqi Universities (Baghdad, Technology, Babylon, Al-Kufa, Al-Mustansyrya, Al-
Nahrain…) in the Areas of ( Fluid Mechanics, Heat Transfer, CFD, Porous Media, Gas
Dynamics, Viscous Flow, FEM, BEM
Lines of Research Covers the Following Fields ;
Aerodynamics
Convection Heat Transfer ( Forced, Free, and Mixed )
Porous Media ( Flow and Heat Transfer )
Electronic Equipment Cooling
Heat Transfer in Manufacturing Processes ( Welding, Rolling, … etc. )
Inverse Conduction
Turbomachinery ( Pumps, Turbines, and Compressors )
Heat Exchangers
Jet Engines
Phase-Change Heat Transfer
Boundary Layers ( Hydrodynamic and Thermal )
Head of the Mech. Engr. Dept. / College of Engineering - University of Baghdad ( December
/ 2007 – October / 2011 )
Member of Iraqi Engineering Union (Official No. 45836).
ASHRAE Member ( 8161964 )
Head of ( Quality Improvement Council of Engineering Education in Iraq QICEEI )
Supervised ( 41 ) M.Sc. Thesis and ( 20 ) Ph.D. Dissertations
Publication of more than (70) Papers in the Various Fields Mentioned above
Member in the Evaluation and Examining Committees of more than ( 300 ) M.Sc. and Ph.D.
Students in their Theses and Dissertations
Member of the Editing Committee of a number of Scientific Journals
Evaluation of more than ( 700 ) Papers for Various Journals and Conferences
Working within the Mechanical Groups in the Consulting Engineering Bureau, College of
Engineering, University of Baghdad, and in the Dept. of Mech. Engr. , in the Mechanical
Design of Various Projects
Contact Information :
Skype Name : drihsan11
Mobile No. : +964-7901781035 : +964-7705236582