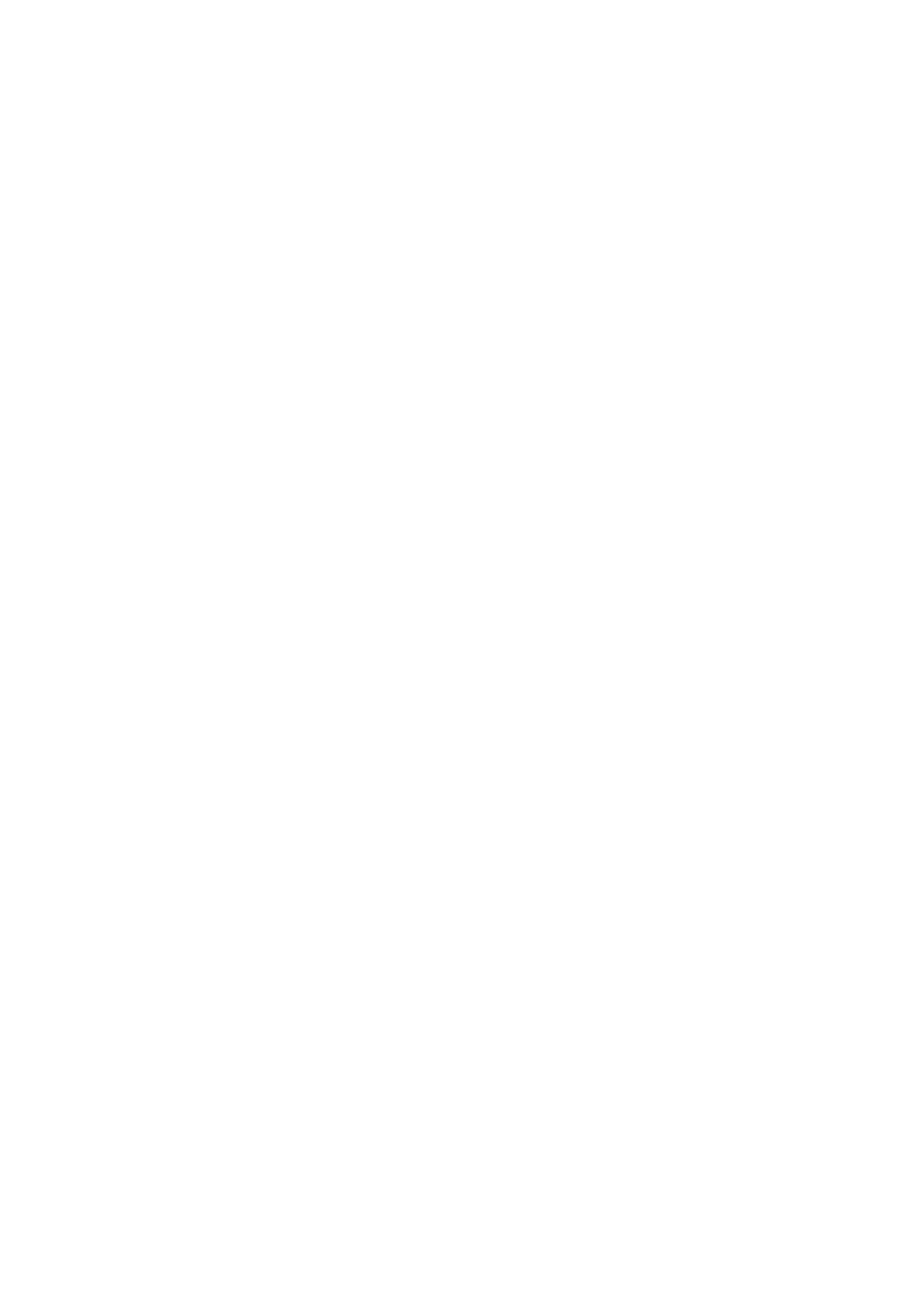
IV
2.1.1.5. Contrôler : …………………………………………………………………………...18
2.1.2. Apport du Six Sigma aux entreprises : ………………………………………………...18
2.2. Phase définition : ………………………………………………………………………...19
2.2.1. Description du processus : …………………………………………………………….19
2.2.2. SIPOC : ………………………………………………………………………………..21
2.2.3. Critical To Quality et indicateurs : …………………………………………………….22
Conclusion : ………………………………………………………………………………….22
Chapitre 3 : Phase Mesure……………………………………………………………………23
Introduction : …………………………………………………………………………………24
3.1. Système de mesure : ……………………………………………………………………..24
3.1.1. Enregistrement des données : ………………………………………………………….24
3.1.1.1. Validation de collecte des données : ………………………………………………...24
3.1.1.2. Collecte des données : ……………………………………………………………….25
3.1.1.3. Saisie des données : ………………………………………………………………….26
3.1.2. IPPM (Internal Part Per Million) : ……………………………………………...……..29
3.1.3. PPM (Part Per Million) : ………………………………………...…………………….30
3.1.4. Diagramme Pareto : …………………………………………………………………...30
3.1.5. Quality Function Deployment : ………………………………………………………..30
3.1.6. Etat de l’existant : ……………………………………………………………………..31
Conclusion : ………………………………………………………………………………….34
Chapitre 4 : Phase Analyse et Amélioration………………………………………………….35
Introduction : …………………………………………………………………………………36
4.1. Etudes du défaut inversions : …………………………………………………………...36
4.1.1. Spécification des données : ……………………………………………………………36
4.1.1.1. Inversion par équipe : ………………………………………………………………..36
4.1.1.2 Inversion par connecteur : ……………………………………………………………37
4.1.1.3 Matrice global des inversions : ………………………………………………………38
4.1.2. Analyse spécifique des inversions par connecteur : …………………………………...39
4.1.2.1 Analyse du connecteur C1E107-E : ………………………………………………….39
4.1.2.2 Analyse du connecteur C90-A : ……………………………………………………...40
4.1.2.3 Analyse du connecteur C1A102 : ……………………………………………………40
4.1.2.4 Analyse du connecteur C91-B : ……………………………………………………...41
4.1.3. Analyse générique des inversions : ……………………………………………………41
4.1.3.1. Vérification des causes potentielles : ………………………………………………..43