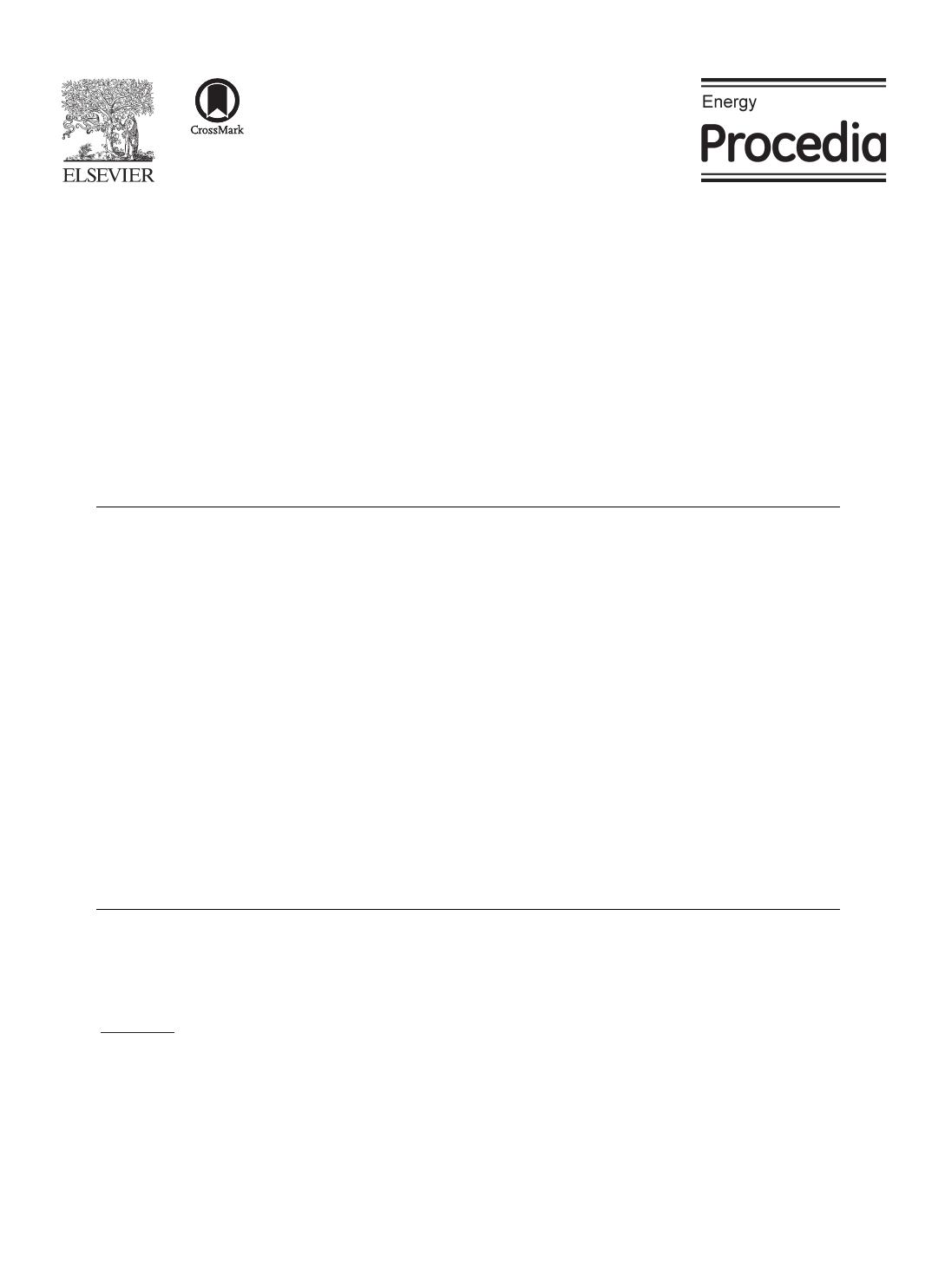
1876-6102 © 2017 The Authors. Published by Elsevier Ltd. This is an open access article under the CC BY-NC-ND license
(http://creativecommons.org/licenses/by-nc-nd/4.0/).
Peer-review under responsibility of the scientific committee of the 8th International Conference on Applied Energy.
doi: 10.1016/j.egypro.2017.03.430
Energy Procedia 105 ( 2017 ) 973 – 979
ScienceDirect
The 8th International Conference on Applied Energy – ICAE2016
Cross-Axis-Wind-Turbine: A Complementary Design to Push
the Limit of Wind Turbine Technology
Wen-Tong Chonga,
, Kok-Hoe Wonga, Chin-Tsan Wangb, Mohammed Gwania,c,
Yung-Jeh Chua,Wei-Chin Chiaa, Sin-Chew Poha
a Deparment of Mechanical Engineering, Faculty of Engineering, University of Malaya, 50603 Kuala Lumpur, Malaysia.
b Deparment of Mechanical and Electro-Mechanical Engineering, National Ilan University, Ilan 260, Taiwan, R.O.C.
c Department of Physics, Kebbi State University of Science and Technology, Aliero, 1144, Kebbi State, Nigeria.
Abstract
Situations such as low wind speed, high turbulence and frequent wind-direction change can reduce the
performance of horizontal axis wind turbine (HAWT). Certain vertical axis wind turbine (VAWT) designs have the
ability to operate well in these harsh operating conditions but they possess low power coefficient generally. In order
to tackle the mentioned problems, a novel cross-axis-wind-turbine (CAWT) is conceptualized to extract wind energy
from both the horizontal and vertical directions of the on-coming winds to maximize the wind energy generation. The
CAWT consists of three vertical blades and six horizontal blades arranged in cross axis orientation. Initial testing
showed that maximum RPM generated by the CAWT is 166% higher than the VAWT under the same experimental
conditions with well-improved starting behavior. Computational Fluid Dynamics (CFD) analysis was done to
illustrate the flow field of the deflected and channeled air stream by omni-directional shroud. The air stream deflected
upwards by the guide vane interacts with the horizontal blades. The CAWT is applicable in a wide variety of
locations, creating significant opportunities for the use of wind energy devices and therefore alleviating dependencies
on fossil fuel.
© 2016 The Authors. Published by Elsevier Ltd.
Selection and/or peer-review under responsibility of ICAE
keywords:cross-axis-wind-turbine, efficiency, renewable energy, urban energy system, wind energy, offshore wind turbine.
1. Introduction
A wind turbine is a device that converts energy from the wind into electrical power. There are
basically two types of wind turbine; the horizontal axis wind turbine (HAWT) and the vertical axis wind
* Corresponding author. Tel.: +6012-723 5038; fax: +603- 7967 5317.
E-
mail address: chong_went[email protected]u.my, chong_wentong@yahoo.com (Wen-Tong Chong) Available online at www.sciencedirect.com
© 2017 The Authors. Published by Elsevier Ltd. This is an open access article under the CC BY-NC-ND license
(http://creativecommons.org/licenses/by-nc-nd/4.0/).
Peer-review under responsibility of the scientific committee of the 8th International Conference on Applied Energy.