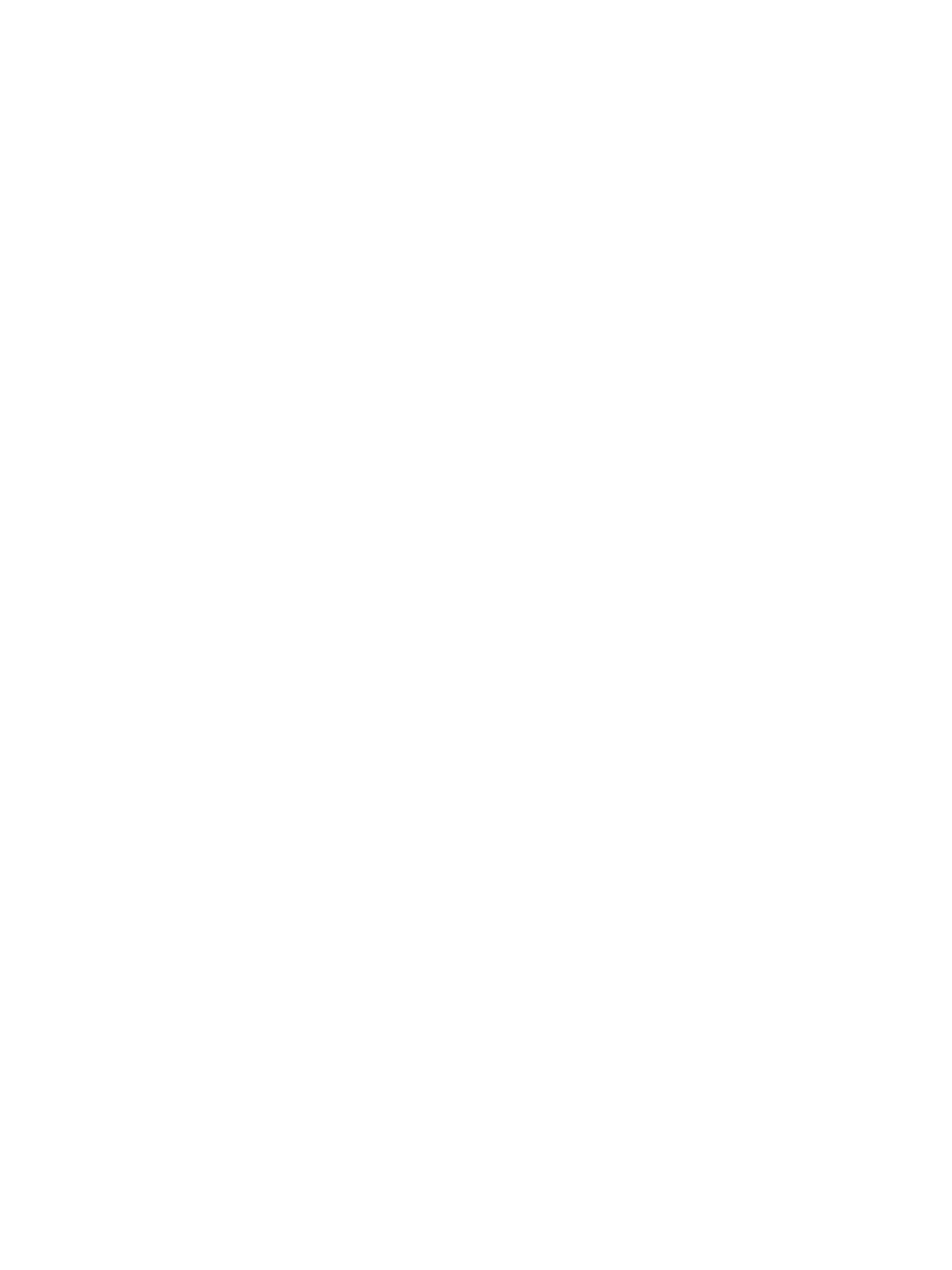
272 IEEE TRANSACTIONS ON INDUSTRIAL ELECTRONICS, VOL. 54, NO. 1, FEBRUARY 2007
Speed-Sensorless Estimation for Induction Motors
Using Extended Kalman Filters
Murat Barut, Student Member, IEEE, Seta Bogosyan, Member, IEEE, and Metin Gokasan, Member, IEEE
Abstract—In this paper, extended-Kalman-filter-based estima-
tion algorithms that could be used in combination with the
speed-sensorless field-oriented control and direct-torque control of
induction motors (IMs) are developed and implemented experi-
mentally. The algorithms are designed aiming minimum estima-
tion error in both transient and steady state over a wide velocity
range, including very low and persistent zero-speed operation. A
major challenge at very low and zero speed is the lost coupling
effect from the rotor to the stator, which makes the information
on rotor variables unobservable on the stator side. As a solution to
this problem, in this paper, the load torque and the rotor angular
velocity are simultaneously estimated, with the velocity taken into
consideration via the equation of motion and not as a constant
parameter, which is commonly the case in most past studies. The
estimation of load torque, on the other hand, is performed as a
constant parameter to account for Coulomb and viscous friction
at steady state to improve the estimation performance at very
low and zero speed. The estimation algorithms developed based
on the rotor and stator fluxes are experimentally tested under
challenging variations and reversals of the velocity and load torque
(step-type and varying linearly with velocity) over a wide velocity
range and at zero speed. In all the scenarios, the current estimation
error has remained within a very narrow error band, also yielding
acceptable velocity estimation errors, which motivate the use of
the developed estimation method in sensorless control of IMs over
a wide velocity range and persistent zero-speed operation.
Index Terms—Extended Kalman filter (EKF), induction motor
(IM), low/zero-speed operation, sensorless control.
I. INTRODUCTION
THERE has been extensive research in the sensorless field-
oriented control (FOC) and direct-torque control (DTC) of
induction motors (IMs) for the last two decades. Both control
methods require the accurate knowledge of the amplitude and
angular position of the rotor or stator flux with reference to
the stationary stator axis (in Cartesian coordinates). Addition-
ally, information on the rotor angular velocity is required for
velocity control over a wide speed range and in the low and
zero-speed range for position-control applications. However,
although speed sensorless drives are now well-established in in-
dustry for medium and high-speed operation [1], their persistent
operation at very low and zero speed still constitutes a persisting
Manuscript received July 20, 2004; revised July 31, 2006. Abstract published
on the Internet September 15, 2006.
M. Barut and S. Bogosyan are with the Electrical and Computer Engineer-
ing Department, University of Alaska Fairbanks, Fairbanks, AK 99775 USA
M. Gokasan is with the Electrical and Electronics Engineering Department,
Istanbul Technical University, Maslak, Istanbul, Turkey (e-mail: gokasan@itu.
edu.tr).
Digital Object Identifier 10.1109/TIE.2006.885123
challenge [2]. The problems are due to parameter uncertainties,
signal acquisition errors, and noise in the very low speed range,
with an additional difficulty encountered at zero speed in steady
state, when the stator current ceases to convey information on
the rotor angular velocity [3], [4].
Model-based methods using IM state equations and signal-
injection methods [5] using the anisotropic properties of the
machine have been competing for the improvement of the
zero/low-speed performance of sensorless IMs [2]. Speed sen-
sorless control methods based on signal injection are capable
of long-term stability at zero stator frequency; however, they
are highly sophisticated and require customized designs for a
particular motor drive [3].
Recently, for the solution of the problem zero/very low
speed, model-based estimation methods have been proposed,
such as in [6]–[8], specifically addressing persistent operation
zero speed. Among those studies [6] uses a total-least-square-
based speed adaptive flux observer which enables zero-stator-
frequency operation over an interval of 60 s, with mean and
maximum estimation error values of 1.34 and 38 r/min, re-
spectively, at zero load. The study in [7] uses model-reference-
adaptive-system-based linear neural networks, presenting
results with a maximum velocity estimation error of 95 r/min
and a persistent operation interval of 60 s at zero speed. The
study in [8] utilizes a continuous sliding-mode approach, for
which zero-stator-frequency results are obtained under load and
presented only for a very short interval of 4 s.
In addition to the aforementioned group of studies taking a
deterministic approach to the design of closed-loop observers,
there are also extended-Kalman-filter (EKF)-based applications
in the literature, taking a stochastic approach for the solution of
the problem. Model uncertainties and nonlinearities inherent to
IMs are well-suited for the stochastic nature of EKFs [9], [10].
With this method, it is possible to make the online estimation
of states while simultaneously performing identification of
parameters in a relatively short time interval [11]–[13], also
taking system/process errors and measurement noises directly
into account. The EKF is also known for its high convergence
rate, which improves transient performance significantly. Ad-
ditionally, accurate estimation and convergence in steady state
requires high-frequency signals, which are also inherently met
by EKFs with the model and measurement noises included in
the model. These properties are the major advantages of the
EKF over other estimation methods and are the reasons why
the method finds wide application in sensorless estimation in
spite of its computational complexity, which also ceases to be a
problem with the developments in high-performance processor
technology.
0278-0046/$25.00 © 2007 IEEE