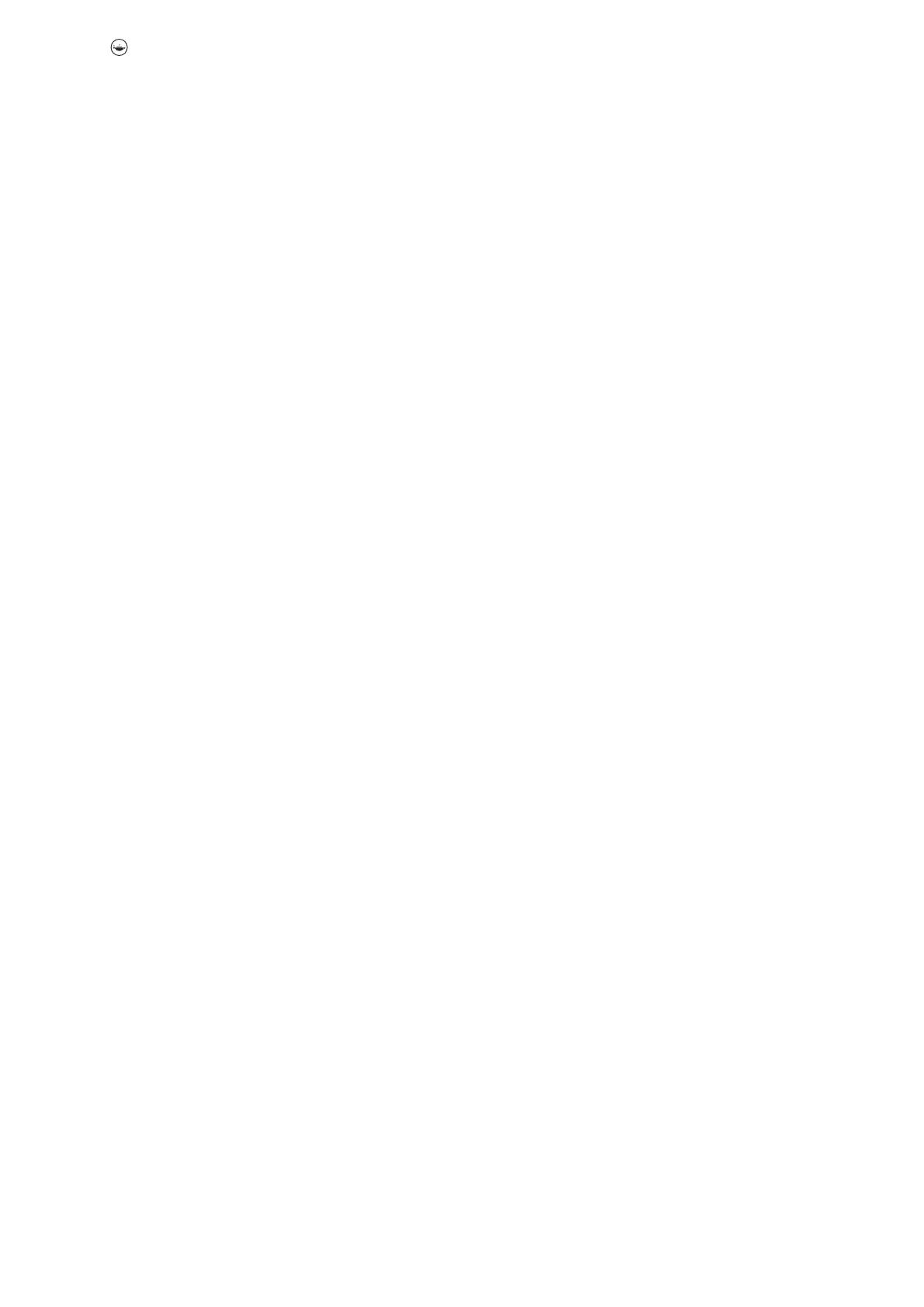
fuzzy logic and neural networks have gained more
importance to improve the electrical system perfor-
mances. In order to improve the conventional DTC
performances, few researchers have used the fuzzy
logic and sliding mode fuzzy to improve the conven-
tional DTC performances by replacing the PI control-
ler by an intelligent controller, as given in [24,25]. In
these works, the speed transient response is improved
but the torque ripples are not much reduced.
Improvements in the DTC performances using neural
networks based switching controller is developed in
some researches works, as given in [26]. The drawback
of Artificial Neural Network (ANN) based switching
controller is that it doesn’t give heuristic knowledge of
process in selection of optimal switching voltage vec-
tor; in addition the control algorithm is complex and
requires a processor with high computation power. To
overcome the limitations of all the cited control stra-
tegies, the fuzzy logic can be used to improve the
nonlinear system performances. The fuzzy logic pro-
cess is easy to understand due to its simple logical
structure and inference mechanism. In fact, the con-
ventional DTC uses two hysteresis controllers to con-
trol the torque and the stator flux. These controllers
generate two states, which produce the same results for
the small and the big error of the torque and the stator
flux. As consequence, the generated switching states of
the inverter cannot produce the best voltages vectors
to make the flux and the torque errors both zero. This
leads in ripples of torque and flux [27–29], and varia-
tions of the switching frequency [30]. In paper [31],
the authors present an analysis of the switching fre-
quency variation which is caused by the hysteresis
band, the motor speed and torque slope. These ripples
can be reduced if the torque and flux errors are sub-
divided into several smaller subsections on which dif-
ferent control action is taken. However, it is hard to
obtain the optimal subsection boundaries for the tor-
que and flux errors. Furthermore, the torque ripples
are affected by the width of the torque hysteresis band
[32]. These ripples change proportionally with the
variations in hysteresis bandwidth of the torque.
However, due to the discrete nature of the control
system, there might be still ripples even with the zero
bandwidth of the hysteresis controller. In addition, if
the bandwidth decreases, the inverter switching fre-
quency increases, which consequently increases the
switching losses in the semiconductors. To solve this
problem the bandwidth of the torque hysteresis con-
troller must be optimized in order to keep the ripple
level and switching frequency variations within accep-
table limits. Therefore, the Fuzzy Logic Control (FLC)
based on the language rules can be used to adapt the
torque hysteresis band in order to reduce the torque
ripples and provide a precise speed response by select-
ing the suitable voltage vector [33–35]. The Fuzzy logic
uses the people’s experience knowledge to release the
rule base and it is based on intuition and simulation
[36]. The FLC is not based on the IM model and its
parameters. It is more suitable for the imprecise pro-
cesses and does not require any mathematical models.
Also, the FLS is a more effective technique when the
system is based on a severely nonlinear mathematical
model [37]. The FLC has been proposed in several
researches work to select the optimal voltage vectors
in conventional DTC [38–41] and to solve the problem
of variable switching frequency [42,43]. Other
researchers have used the fuzzy logic in speed control
andflux observer to improve the electrical motors
performances [44–47]. In addition, the fuzzy logic is
used in some research works to improve the DTC
performances and to reduce the commutation losses
in the inverter, as given in [48–50]. In paper [48], the
authors presented a fuzzy logic controller associated to
the DTC of PMSM to reduce the ripples and the
switching losses in the inverter by arranging the inver-
ter switching. In paper [49,50], the authors present
a combination between the DTC and the fuzzy logic
control in order to provide an operation with low
ripples and to keep the switching losses at an accep-
table level, by selecting a suitable voltage vector for
each sampling period. This demonstrates that utilizing
the fuzzy logic technique, it is possible to improve the
DTC performances by reducing the ripples of the
inverter losses.
The first contribution in this paper is oriented
toward the use of a Fuzzy Logic System (FLS) to replace
the switching table and the hysteresis controllers, in
order to reduce the torque and the flux ripples, as well
as the stator current distortions. The design with the
XSG tool and the hardware implementation on the
FPGA of the proposed Fuzzy DTC (FDTC) control
strategy is the second contribution in this paper. In
this study, the torque and the flux errors and the stator
flux vector position are fuzzified into several fuzzy sub-
sets in order to select a more suitable space voltage
vector to smooth the torque and the flux ripples and
control the switching frequency variations. With the
proposed method, the transistors are only switched
when it is needed which consequently reduces the
inverter switching losses. The Fuzzy rule base provides
precise control by selecting optimal switching state of
the inverter in order to meet required torque and flux
demand by the induction motor. The performance of
the proposed method has been verified by digital simu-
lation utilizing the Matlab/Simulink environment and
the Xilinx System Generator (XSG) tool, and experi-
mental validation using an FPGA Virtex 5 and
a squirrel cage induction motor.
Traditionally, two main families of digital devices
are used to control the induction motor drive. The
first family integrates the microcontroller (STM32F3,
STM32F4, STM32F1. . .) [51,52] and the Digital
Signal Processor (DSP) [53–55] which can be
2S. KRIM ET AL.